- 8 (812) 407-37-03
- 197348, г. Санкт-Петербург, улица Аэродромная, д. 8, литер А, офис 418
- order@carbidetool.ru
Обрабатываемость нержавеющих сталей (теоретические основы и практические рекомендации).
(статья находится в разработке, материал будет редактироваться и дополняться)
В этой статье изложен материал об обрабатываемости различных марок нержавеющих сталей, даны рекомендации по обработке из различных справочников и литературы, а также даны рекомендации из практических наработок.
Под способностью материала подвергаться резанию понимают достижение при его обработке каких-либо из следующих технологических показателей: скорости резания vT при заданном периоде стойкости инструмента Т (например, v60, т.е. скорость резания при стойкости Т = 60 мин); качества обработанной поверхности; силы или мощности резания; определённой формы стружки. Обрабатываемость материалов резанием влияет, прежде всего, на период стойкости режущего инструмента и, следовательно, ограничивает предельную скорость резания (производительность обработки). Качественно обрабатываемость характеризуют по типу стружки, образующейся при резании исследуемого материала в эталонных условиях.
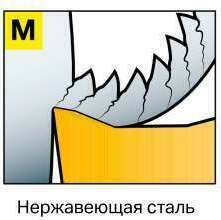
Нержавеющая сталь группа ISOM
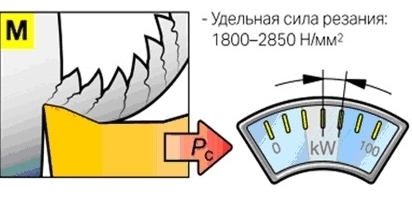
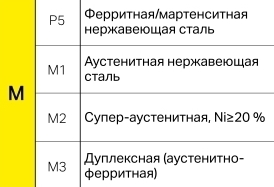
В ГОСТ 5632-72 представлена классификация нержавеющих сталей в зависимости от их структуры:
- мартенситные стали, которые имеют в качестве основной структурной составляющей мартенсит. Они содержат от 12 до 17 % Cr (хромистые стали) и имеют достаточно высокое содержание углерода (C), что позволяет подвергать такие сплавы закалке.
- мартенситно-ферритные сплавы имеют структуру, в которой, кроме мартенсита, содержится более 10 % феррита. Они включают от 13 до 18 % Cr (хромистые стали).
- ферритные стали отличаются структурой, основанной на феррите. В их составе есть от 13 до 30 % Cr (хромистые стали). Такие сплавы отличаются магнитными свойствами. Они имеют доступную себестоимость, что обусловлено низким содержанием никеля.
- аустенито-мартенситные стали имеют структуру, состоящую из аустенита и мартенсита в определенных пропорциях. Они включают от 12 до 18 % Cr и от 4 до 9 % Ni (хромоникелевые и хромомарганцевоникелевые стали).
- аустенито-ферритные сплавы имеют структуру, включающую аустенит и минимум 10 % феррита (хромоникелевые и хромомарганцевоникелевые стали).
- аустенитные стали имеют структуру, основанную на аустените (хромоникелевые стали, хромомарганцевоникелевые стали).
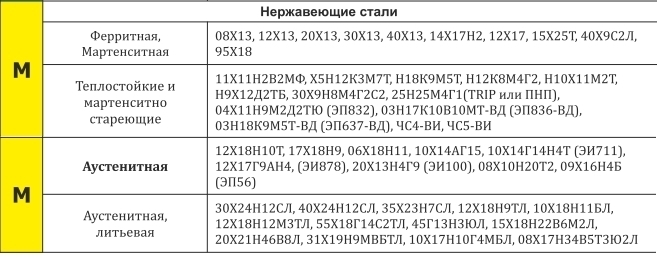
В сравнении с обычными сталями, высоколегированные коррозионно-стойкие и жаростойкие стали обладают худшей обрабатываемостью, так как содержат в больших количествах легирующие элементы: хром (15... 18 %), никель (8... 11 %), марганец (1.. .2 %). Иногда в них входят в небольших количествах титан, вольфрам, молибден, ниобий при некотором снижении содержания хрома и никеля.
Обрабатываемость нержавеющих сталей представлена ниже на графике.
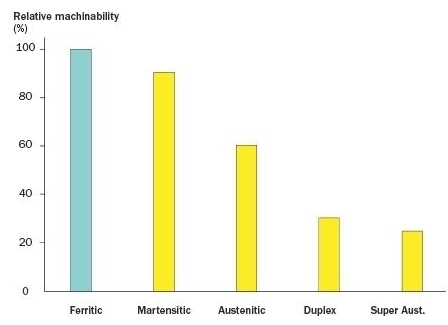
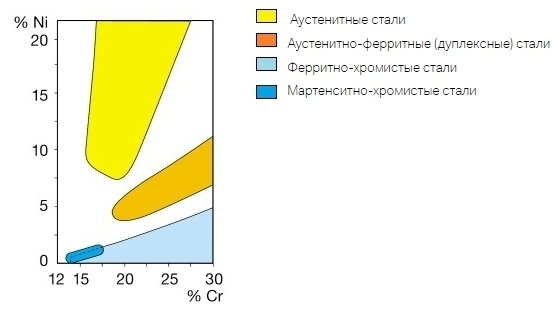
Снижение обрабатываемости этих сталей связано с изменением их механических и теплофизических свойств. Например, жаростойкие (окалино-стойкие) и жаропрочные стали аустенитного класса отличаются высокой упрочняемостью при резании. Некоторые марки сталей в процессе пластического деформирования склонны к структурным превращениям, заключающимся в переходе аустенита в мартенсит. Эти стали, как правило, имеют низкую теплопроводность, что затрудняет отвод теплоты из зоны резания в стружку и заготовку. При этом повышаются температура резания и интенсивность износа инструментов, возможно образование термических трещин на кромках инструмента (пластин).
Стоит заметить, в определенных случаях предварительная термическая обработка на структуру - способствует улучшению обрабатываемости многих типов нержавеющих сталей.
При обработке нержавеющих сталей затруднен контроль над стружкообразованием, наиболее плохой контроль над стружкодробленим происходит при обработке аустенитных и дуплексных нержавеек, относительно хороший при обработке ферритной и мартенситной нержавеющих сталей. Обработка нержавеющих сталей сопровождается высокими силами резания и высокой температурой в зоне резания, липкие сорта склонны к налипанию на режущую кромку (образование наростов при невысоких скоростях обработки), склонны к упрочнению. Для снижения вероятности образования наростов рекомендуется обработка на скоростях более 100-120 м/мин. При черновой обработке, в случае, когда подача СОЖ строго в зону резания затруднена даже с применением высокого давления СОЖ через инструмент (державку) – рекомендуется работа без применения СОЖ для снижения вероятности возникновения термотрещин. При чистовой обработке применение СОЖ обязательно (при этом стоит заметить, что качество обработанных поверхностей, стойкость инструмента во многом зависит от качества СОЖ и схемы его подачи). Подача СОЖ под высоким давлением четко в зону резания может снизить износ инструмента до 2-5 раз. Нужно упомянуть и положительный опыт при охлаждения зоны резания углекислотой до температуры минус 50-70 градусов по Цельсию.
При работе на универсальных станках в качестве смазки (СОЖ) при обработке нержавеющих сталей часто применяют олеиновую кислоту, сало, иногда специализированные смазки (см.приложение 1).
Коды MC для нержавеющей стали
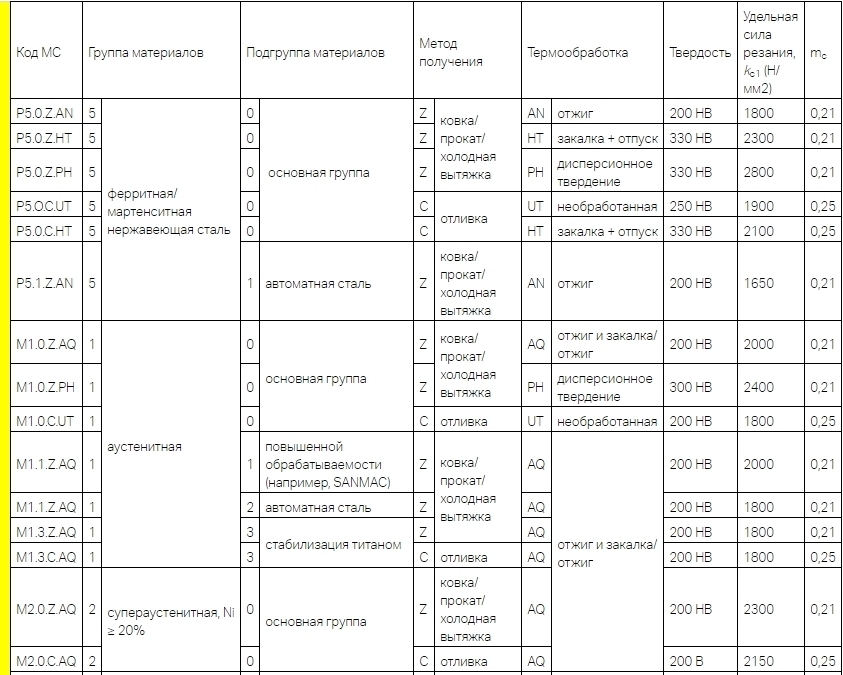
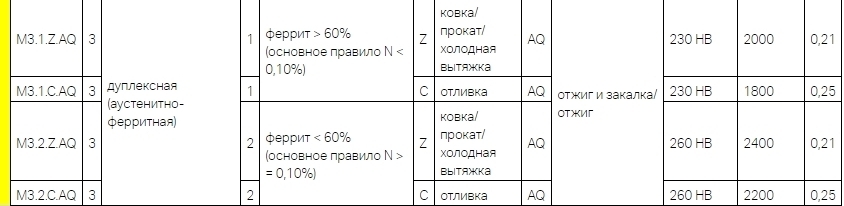
Ферритные нержавеющие стали имеют обрабатываемость, схожую с низколегированными сталями, мартенситные нержавеющие стали более склонны к упрочнению в процессе резания и вызывают очень высокие силы резания. Более высокая скорость резания и более прочный сплав в сочетании с усиленной режущей кромкой способствуют повышению стабильности. У многих производителей инструмента (в частности Sandvik, Walter и т.д. ферритные и мартенситные нержавеющие стали отнесены в группу материалов Р, исходя из схожести свойств при обработке (инструмент для их обработки также следует выбирать для сталей группы Р).
У ферритных и мартенситных нержавеющих сталей нормальное содержание хрома составляет от 12 до 18%. Другие легирующие элементы представлены в незначительном количестве. Мартенситные нержавеющие стали содержат относительно высокое количество углерода, что позволяет подвергать их закалке. Ферритные стали обладают магнитными свойствами. Способность к сварке и у ферритных, и у мартенситных сортов стали достаточно низкая, а стойкость к коррозии – от средней до низкой и может быть улучшена за счёт добавления хрома. В процессе их обработки в основном возникает износ по задней поверхности и реже образование лунок и наростов.
Аустенитные стали образуют основную группу нержавеющих сталей. Самый распространённый состав – 18% хрома и 8% никеля (например, сталь 18/8, тип 304). При добавлении 2–3% молибдена получается более стойкая к коррозии сталь, которую часто называют кислотостойкой (тип 316). Эта группа MC включает также супераустенитные сорта нержавеющей стали с содержанием никеля более 20%. Дисперсионно-твердеющие аустенитные стали (PH) имеет аустенитную структуру в закалённом состоянии, содержание хрома составляет> 16%, никеля> 7% и алюминия – около 1%.
Механическое упрочнение способствует увеличению твёрдости поверхности и стружки, что в свою очередь ведёт к образованию проточин. Кроме этого, оно провоцирует адгезию и, как следствие, образование наростов. Относительная обрабатываемость составляет 60%. При обработке в закалённом состоянии возможен отрыв покрытия и материала основы от режущей кромки, что в результате ведёт к выкрашиванию и ухудшению качества обработанной поверхности. Аустенитные стали дают прочную и длинную сливную стружку, которая плохо ломается. Добавление серы способно улучшить обрабатываемость и одновременно снизить стойкость к коррозии. Используйте пластины с положительной геометрией и острыми кромками. Выполняйте резание на глубину больше упрочнённого слоя и поддерживайте её на постоянном уровне. Помните, что при обработке выделяется большое количество тепла.
Дуплексные нержавеющие стали получаются при добавлении никеля в ферритную хромистую нержавеющую сталь формируется структура/матрица со смешанной основой, содержащая и феррит, и аустенит. Дуплексные стали имеют высокую прочность на растяжение и очень высокую стойкость к коррозии. Названия «супердуплексная» и «гипердуплексная» указывают на более высокое содержание легирующих элементов и ещё большую стойкость к коррозии. Как правило, в дуплексной стали содержание хрома колеблется от 18 до 28%, а никеля – от 4 до 7%. При этом доля феррита составляет 25–80%. При комнатной температуре ферритная и аустенитная фазы обычно находятся в равном соотношении.
Относительная обрабатываемость достаточно низкая – всего 30%, что связано с высоким пределом текучести и высокой прочностью на растяжение. Высокое содержание феррита – более 60% – улучшает обрабатываемость. При обработке образуется прочная стружка, которая может стать причиной повреждения нерабочей режущей кромки, а также возникают высокие силы резания. В процессе резания выделяется большое количество тепла, что ведёт к пластической деформации и интенсивному лункообразованию. Небольшие главные углы в плане предпочтительны, так как они позволяют избежать образования проточин и заусенцев. Важное значение имеет жёсткость закрепления инструмента и заготовки.
Итак, основные проблемы при обработке нержавеющих сталей:
- вязкость (характерна для аустенитных и дуплексных марок) – сложность в контроле за стружкообразованием и налипание на кромку инструмента, склонность к возникновению вибраций;
- низкая теплопроводность и высокая температура в зоне резания – необходимо эффективная система подачи СОЖ для охлаждения инструмента, в противном случае возможно возникновение термотрещин, либо вести обработку при более низких режимах резания, предъявляются особые требования по термостойкости к инструментальным материалам и типам покрытий;
- сохранение прочностных свойств – склонность к самоупрочнению в широком диапазоне температур, образование наклёпа;
- абразивный износ – легирующие элементы, наличие карбидов и интерметаллических соединений в структуре материала вызывают повышенный износ инструмента;
- стружкодробление – особое значение имеет выбор стружколомов, нанесение типов покрытий на режущую кромку инструментов (как правило, для аустенитных типов нержавеющих сталей применяются большие положительные передние углы заточки инструмента (снижение сил резания, предотвращение налипаний и образования наклепа), покрытие типа PVD (для сохранения остроты режущей кромки и снижения налипаний)
- повышенные требования к жесткости оборудования и применяемого инструмента и оснастки – при низкой жесткости СПИД склонность к вибрациям значительно возрастает, что существенно затрудняет процесс обработки и снижает стойкость инструмента (одной из интересных тем исследования является применение ультразвуковых преобразователей, которые позволяют снизить силы резания и облегчить процесс обработки).
Говоря про применение современных износостойких покрытий при обработке нержавеющих сталей стоит отметить:
- CVD покрытия, как правило более толстые, многослойные, лучше сопротивляются износу, но имеют менее острую кромку (скругленная) – в большей степени их применение обосновано при обработке ферритной, мартенситной нержавеющей стали, иногда и аустенитной, но как правило с применением положительных передних углов на стружколомах и в основном при черновой обработке (обдирке)
- PVD покрытия более тонкие, более острая режущая кромка – в основном при чистовых и получистовых работах и для обработки более вязких (липких) сортов нержавеющих сталей.
Работа по усовершенствованию физико-химических состав износостойких покрытий ведется постоянно, совершенствуется их состав, прочностные и термические свойства, увеличение однородности, направленности структуры покрытий, снижения коэффициента трения и т.д.
В качестве примера приведём описание свойств покрытий для токарных пластин производителем Sumitomo, при этом прослеживаются свойства и параметры, определяемые тем или иным типом покрытий и твердосплавной основы.
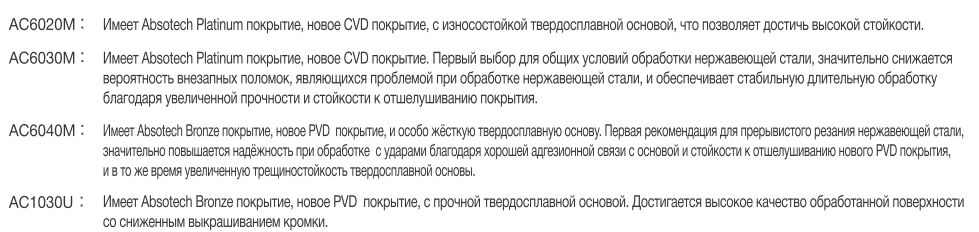
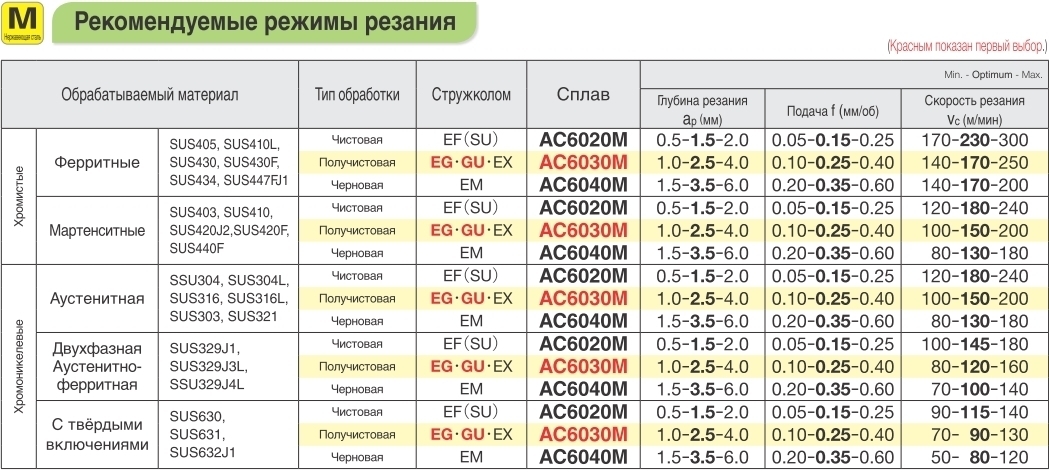
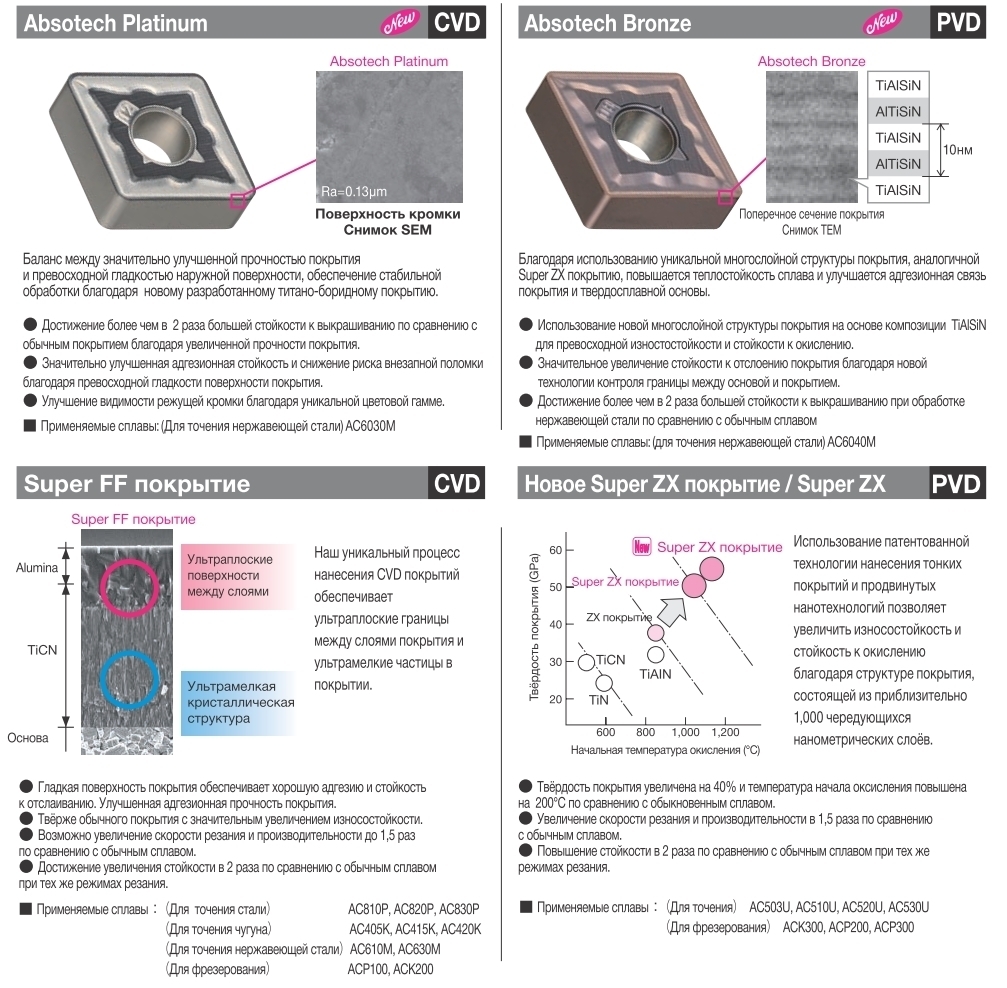
Нужно заметить, что при обработке нержавеющих материалов на современном жестком оборудовании в основном применяются твердосплавные инструменты, на старом оборудовании (универсальных станках) при низкой жесткости СПИД чаще применяются инструменты из быстрорежущих сталей (лучшие результаты дают применение быстрорежущих сталей типа Р18, кобальтированных быстрорезов HSS-E Co5-8%, а также порошковые быстрорежущие стали в сочетании с износостойкими покрытиями).
При чистовой обработке на ЧПУ станках хорошие результаты показывают пластины из кермета (но не все керметы одинаково удачны в данном случае, …в первом числе Kennametal, Kyocera, в определенных случаях Mitsubishi)
Среди старых инструментов с применением твердого сплава (сменные пластины или напайки) наибольшее распространение для обработки нержавеющих сталей получили сплавы ВК8 (для черновой обработки, как более динамически прочный сплав) и ВК6 и ВК6-ОМ – чаще применяемые для чистовой обработки. Нужно отметить, что данные сплавы были разработаны в основном для обработки на невысоких скоростях. На более высоких скоростях резания рекомендуется применять резцы со сплавом пластин на основе карбидов титана, таких как Т14К8.
Говоря про определение оптимальных режимов резания, стоит вспомнить об одной из фундаментальных работ доктора технических наук, профессора А.Д. Макарова «Оптимизация процессов резания» 1976 г. Москва «Машиностороение». Профессор А.Д. Макаров предложил модель оптимизации по оптимальной температуре резания в зоне контакта, при которой для разных групп инструмент и обрабатываемая деталь, есть оптимальная температура в зоне резания, при которой скорость износа режущей части инструмента, так же является оптимальной. Причем значение скорости резания, глубины, подачи разные для различных их соотношений в зависимости от вида обработки, при этом каждому выбранному типу обработки соответствует своя оптимальная температура в зоне резания, при которых наблюдается наименьшая интенсивность износа инструмента, обусловленная различными факторами.
В качестве примера по изучению влияния различных параметров резания при обработке нержавейки 12Х18Н10Т приведем небольшой пример из данной книги.
В нашей статье «Экономическое обоснование режимов резания и эффективности производства (о проблеме с разных позиций).» есть ссылка, что бы скачать эту книгу – рекомендовано, для более глубокого понимания назначения оптимальных режимов резания.

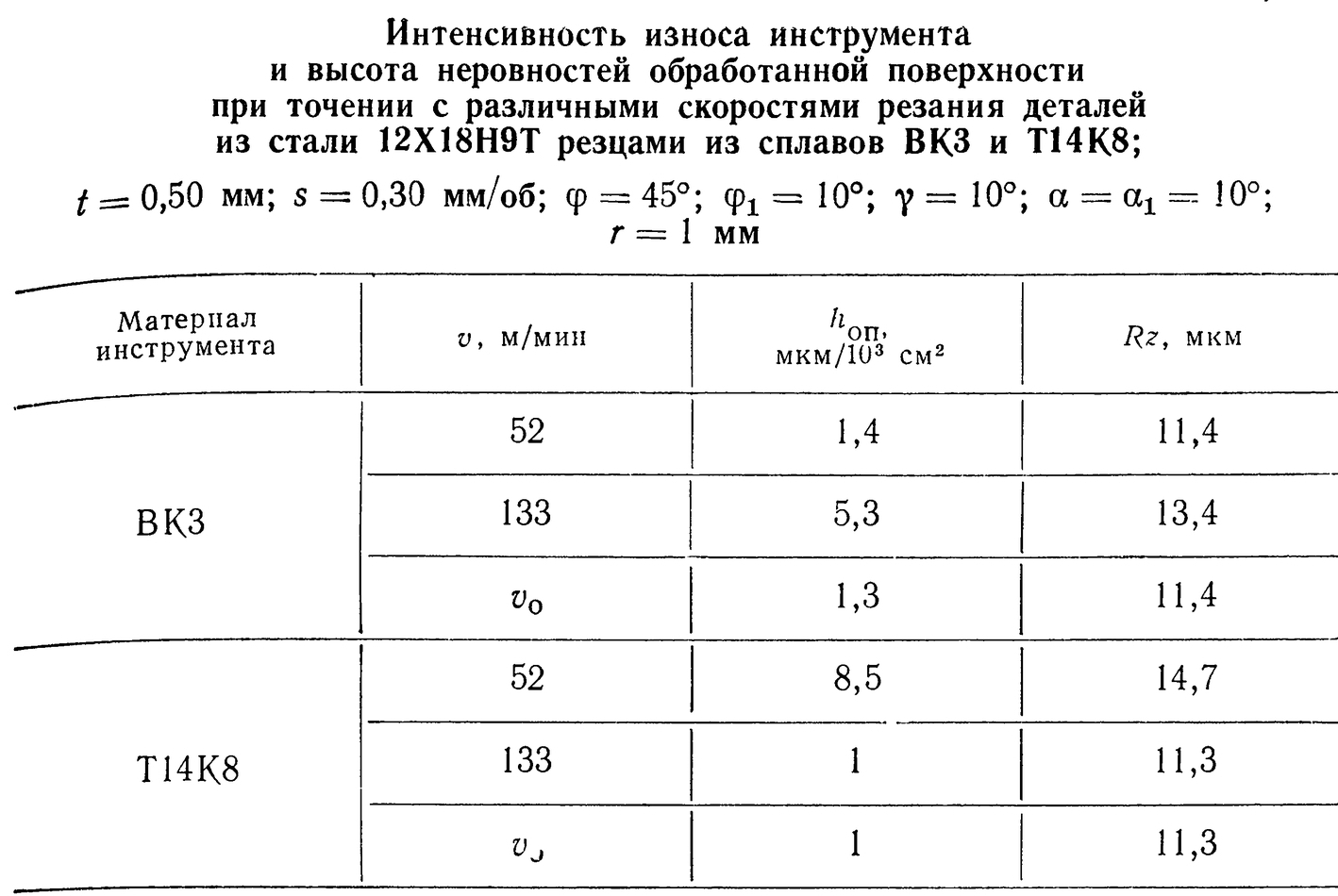
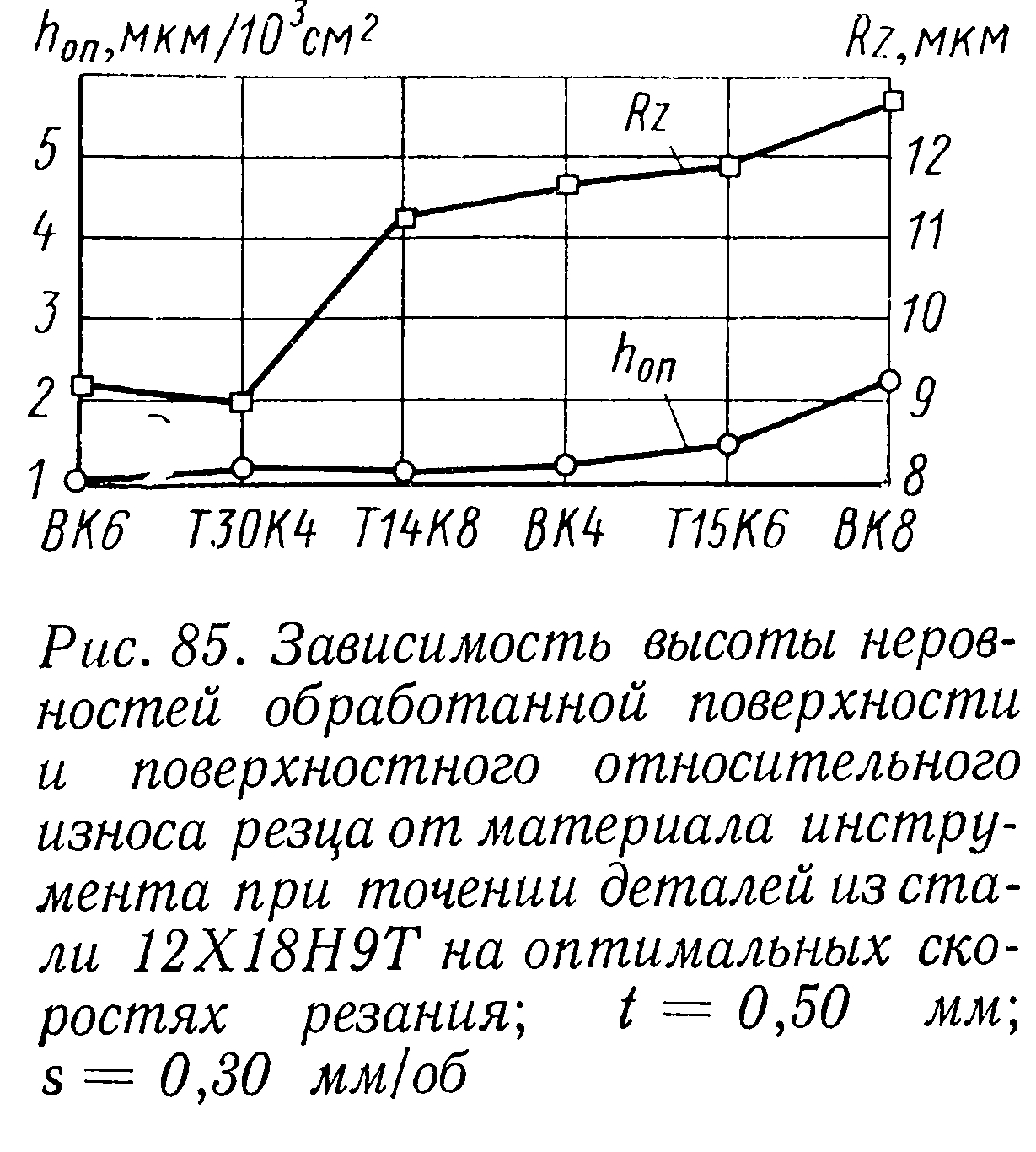
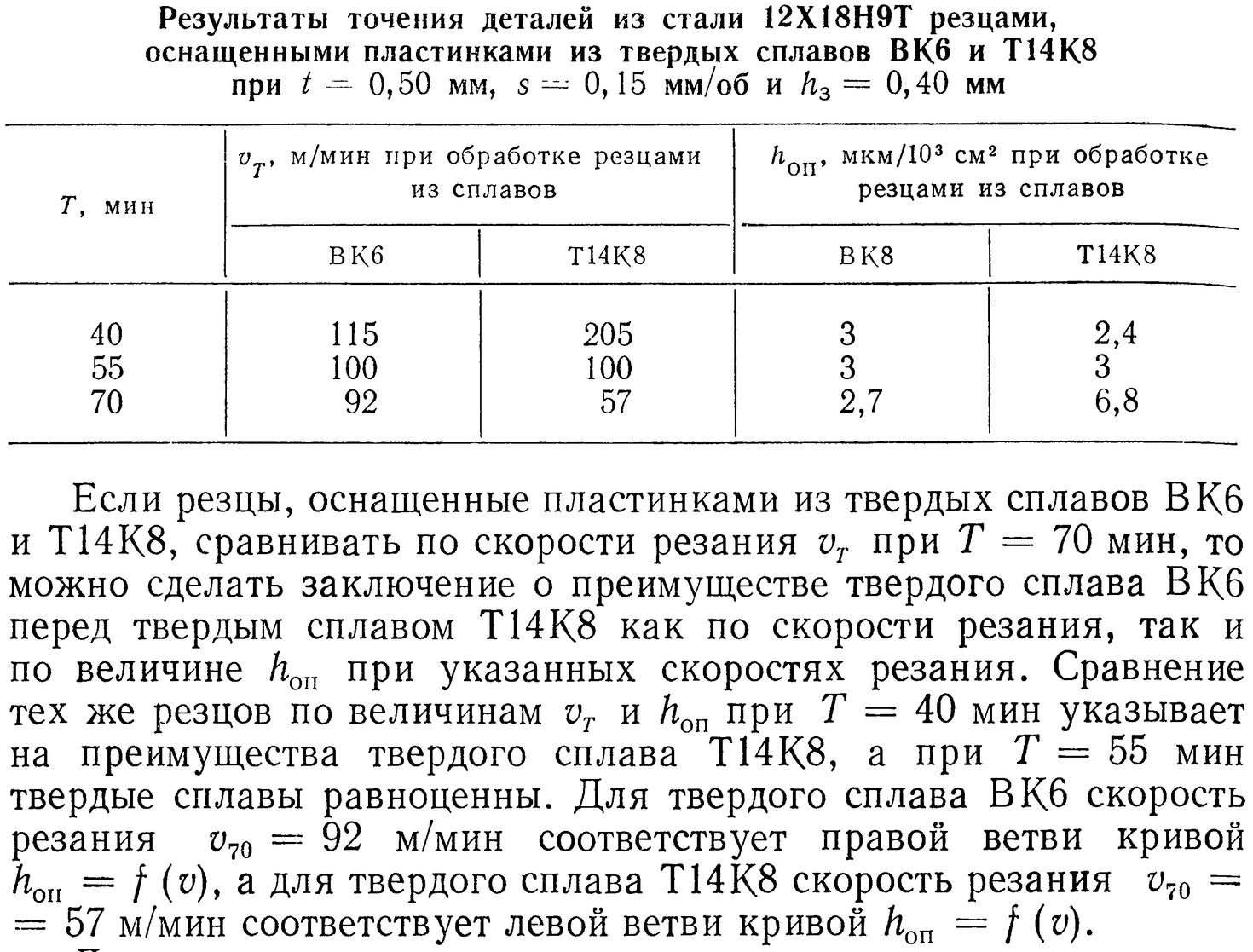
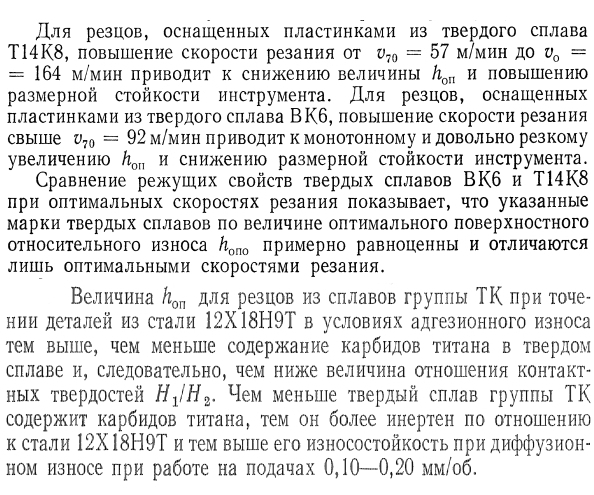
Приложение 1
Специализированные смазки применяемые при обработки нержавеющих сталей и прочих жаропрочных материалов
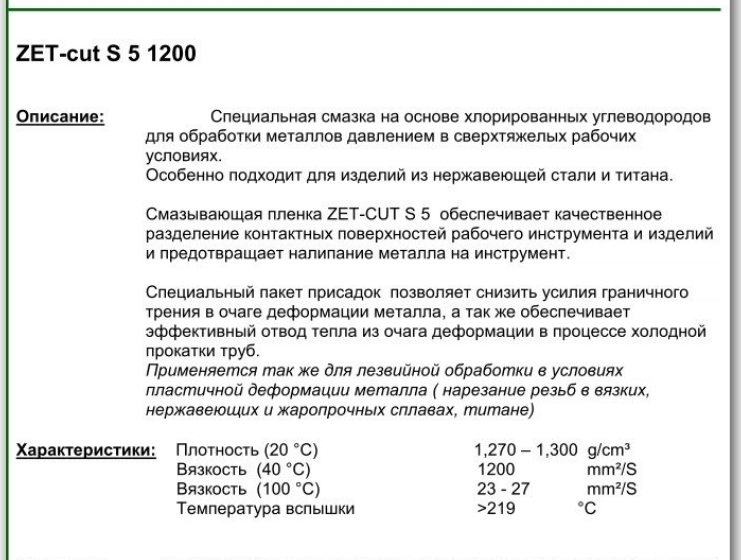
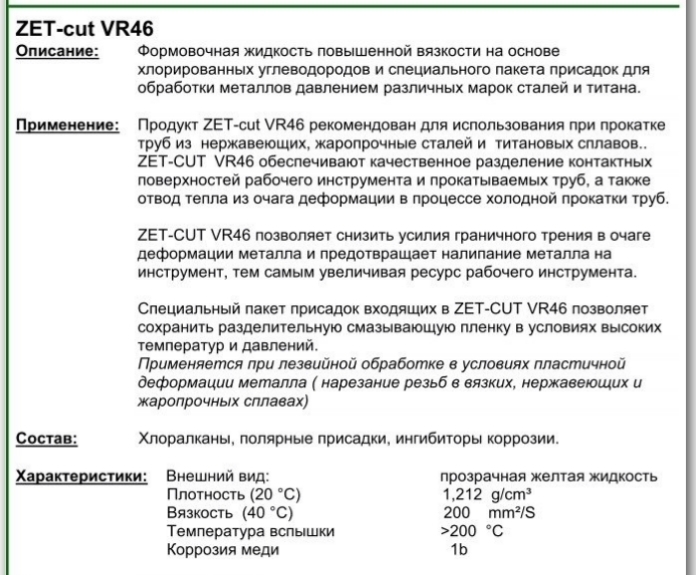
Использование материалов сайта возможно только с письменного разрешения администрации сайта и активной гиперссылкой на источник.
Свяжитесь с нами
Оставьте свое сообщение и мы свяжемся с вами, чтобы предложить лучшие условия сотрудничества!
Звоните: (812) 407-37-03
Пишите: order@carbidetool.ru
ООО «ТУЛЭКС» ИНН 7838092179, г. Санкт-Петербург, улица Аэродромная, д. 8, литер А, офис 418