- 8 (812) 407-37-03
- 197348, г. Санкт-Петербург, улица Аэродромная, д. 8, литер А, офис 418
- order@carbidetool.ru
Высокоскоростное фрезерование (High Speed Cutting (HSC, HSM)).
По вопросу высокоскоростного резания и сегодня существует много споров об эффективности данной стратегии, о различных нюансах и т.д., даже не существует четкого определения, что такое высокоскоростная обработка.
Говорят многие, а вот применяют не многие... а применяют правильно — еще гораздо меньше. Многие, кто слышал о такой стратегии и решили реально ее применить, зачастую не зная основных особенностей, совершают массу ошибок в процессе ее применения и, как правило, ничего хорошего из этого не получается... только поломки и большие затраты.
Многие полагают, что нужно взять инструмент из дорогого каталога и поставить максимально-рекомендуемые режимы резания... но в итоге ни чего не получается.
Давайте рассмотрим в чем особенности данной стратегии и какие основные нюансы должны учитываться (хотя в рамках данной статьи описать все важные факторы просто невозможно).
Высокоскоростная обработка (ВСО) - это методология обработки, которая фокусируется на чрезвычайно быстрых, но легких режимах резания с низким давлением. Результатом является общее увеличение скорости удаления материала.
Целью HSM является использование высоких скоростей для достижения высокой скорости удаления материала. Для успешного достижения этой цели необходимо понять восемь основных принципов:
- Жесткость инструмента и заготовки
- Балансировка инструментов
- Тестирование гармоник инструмента
- Контролируемая нагрузка на инструмент
- Короткие шаги инструмента
- Выбор инструмента
- Понимание материала
- Требования к станку
Помимо этого, существует несколько общих проблем для высокоскоростной обработки:
- Многие материалы обрабатываются в закаленном состоянии. Работа на высоких оборотах может означать больше тепла, выделяемого при резке. Некоторые металлы становятся очень твердыми при нагревании и могут привести к катастрофическому выходу из строя инструмента, если не будут приняты меры по снижению нагрева.
- Высокие скорости увеличивают риск вибрации при резке. Это резко сокращает срок службы инструмента, может легко повредить и сломать детали.
- Силы резания могут быть довольно высокими. Общая проблема заключается в том, что инструменты вытаскиваются из держателей и вызывают серьезные проблемы.
- Это высокопроизводительная обработка. Не все машины, особенно старые, готовы к выполнению этой задачи.
- Траектории, которые обеспечивают эти скорости, более продвинуты. Они требуют некоторой дополнительной подготовки, а также солидного CAM-пакета для успешной работы.
Немного истории...
В начале 30-х годов C.Salomon занимался последствиями очень высоких скоростей резки, проводя испытания с дисковыми пилами. Работая со скоростью 15000 м/мин он пришёл к выводу, что температура при обработке резанием достигает максимума и при дальнейшем повышении скорости резки обратно понижается меньше значения, критического для обрабатываемого материала.
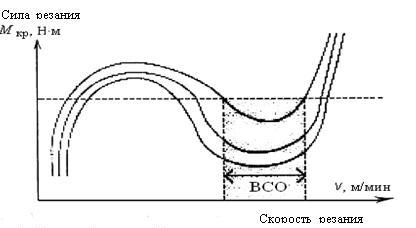
После подачи заявки на патент № 523594 (обработка на высоких скоростях резки) пройдёт ещё много времени прежде, чем данная теория найдёт практическое применение. В течении десятилетий многие учёные посвящали себя этой теории. В 1947 году это был Кузнецов с 50000 м/мин, в 1958 году – Кроненберг с 72000 м/мин и в 1972 Арндт с 132000 м/мин. Все они проводили баллистические испытания, в которых они пропускали изделия вдоль инструмента.
Но лишь в начале 1960 года удалось получить решающие основные знания по процессу резки и механизмам действия при высоких скоростях. Институту по производственной техники и режущим инструментальным станкам (PTW) технического института города Дармштадт удалось, используя магнитные шарикоподшипники, проникнуть в область высоких скоростей Vc 4700 м/мин. При этом впервые стали видны огромные выгоды для промышленного применения. Появилась возможность осуществить уменьшение времени обработки при улучшенной точности в 40 %.
В дальнейшем в этом институте были организованы исследовательские проекты под руководством профессора Шульца и разработаны базовые документы по практическому использованию этой технологии.
Ещё в начале 80-х годов эксперты не видели будущего этой технологии. Причиной этого было то, что исходили только из того, что возможному выигрышу по времени противостоял очень большой износ инструмента, который ставил под сомнение экономичность этого метода. Сегодня можно сказать точно, что аргументация была неправильная. Выгоды настолько велики, что об этом даже и не стоит больше спорить.
Высокоскоростная механическая обработка (HSM – High Speed Machining) и высокоскоростное фрезерование (HSM – High Speed Milling), в частности, в последние годы существенно изменили подход к методам механообработки. Решающим фактором в оценке процесса HSM-обработки является производительность станков, что определяет стоимость производства и повышение качественных характеристик процесса обработки.
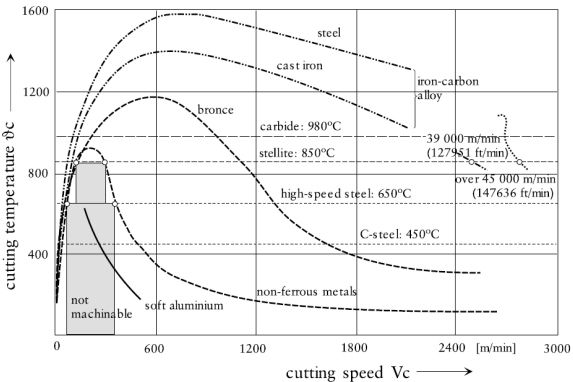
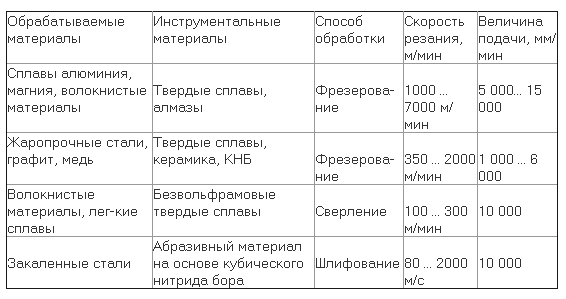
Например, при фрезеровании алюминия используются следующие диапазоны скоростей, м/мин: традиционный – менее 500; высокопроизводительный – 500 ... 2500; высокоскоростной – 2500 ... 7500; сверхвысокоскоростной – более 7500.
Одним из важных факторов при ВСО является не только снижение величины крутящего момента в зоне высоких скоростей, но и перераспределение тепла в зоне резания. При небольших сечениях среза в данном диапазоне скоростей основная масса тепла концентрируется в стружке, не успевая переходить в заготовку. Поэтому считается, что высокоскоростное фрезерование, особенно развитое в технологиях ВСО, базируется на сокращении количества тепла, возникающего при обработке резанием, которое обычно и есть причина износа инструмента.
Исследования, проведенные во время ВСО с правильно подобранными параметрами, показали, что 75% произведенного тепла отводится со стружкой, 20% – через инструмент и 5% – через обрабатываемую деталь.
Преимущество ВСО получается также за счет обработки в надкритическом диапазоне колебаний: при высоких частотах вращения, которые используются при ВСО, значительно превышают частоты собственных колебаний детали, инструмента и компонентов станка. Одновременно с этим, благодаря небольшим поперечным сечениям среза, силы резания невелики, что благоприятно сказывается на точности обработки. Кроме того – высокое качество получаемой поверхности, отсутствие дробления при резании, возможность обработки тонкостенных изделий.
Особенности ВСО предъявляют высокие требования к станку: конструкция станка должна иметь высокую жесткость, высокооборостистый шпиндель, высокие скорости перемещений, современную систему ЧПУ с высокой скоростью обработки кадров (не менее 100-200 кадров в секунду).
С учетом того, что ВСО ставит задачу обеспечения высокого качества обрабатываемой поверхности, дополнительное внимание следует уделить подбору режимов резания с точки зрения нахождения зон, где отсутствуют вибрации. Например, показаны зоны вибрации с различным числом волн N между зубьями фрезы в зависимости от глубины и скорости.



Практически для каждой комбинации СПИД (станок—приспособление—инструмент—деталь) придется находить стабильные зоны, и, в связи с отсутствием отработанных рекомендаций, их придется экспериментальным путем искать непосредственно на станке. Наиболее склонны к вибрации коневые фрезы с нулевым радиусом скругления. Для уменьшения вибраций следует выбирать фрезы с закругленной режущей кромкой.
Максимальная скорость резания при ВСО не всегда обеспечивает максимальную производительность, и связано это не с уменьшением стойкости фрезы. При фрезеровании с частотой вращения шпинделя выше 15000 об/мин появляется интервал частот, в котором резание происходит более стабильно, чем на частотах выше или ниже этого интервала, без вибраций и дробления. В этом интервале глубину резания можно увеличить в 2 – 3 раза. Вследствие прерывистого характера резания фрезерованная поверхность имеет характерную волнистость. При каждом последующем проходе выполняется резание «по следу», при этом частота врезаний зубьев накладывается на волнистость обработанной поверхности. Не очевидно, но процесс резания протекает наиболее стабильно, если волнистость поверхности и вибрация фрезы находятся в одной фазе (в резонансе), как показано на рисунке.
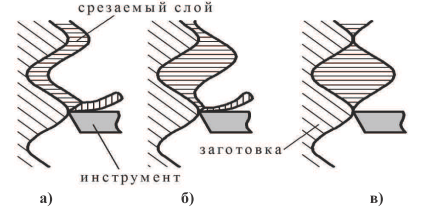
В этом случае нагрузка на инструмент постоянна, это оптимальная область частот вращения шпинделя. Напротив, наибольшая вибрация и дробление реализуются, если волнистость поверхности и частота воздействия зубьев фрезы находятся в противофазе, то есть в режиме диссонанса.
Определение оптимальных зон обработке по диаграмме стабильности.
На тестовой заготовке выполняют несколько серий проходов с разными скоростями вращения шпинделя, оставляя подачу на зуб постоянной для всех проходов каждой серии. На каждой последующей серии увеличивают глубину фрезерования и следят за нагрузкой, так как процесс резания может проходить стабильно даже при таких глубинах резания, когда шпиндель уже не сможет преодолевать возникающую нагрузку. Оптимальные параметры обработки определяют по качеству обработанной поверхности на каждом проходе.
Задавая сечение срезаемого слоя и минутную подачу, скорость съема металла на каждом проходе определяют, как показано на рисунке.
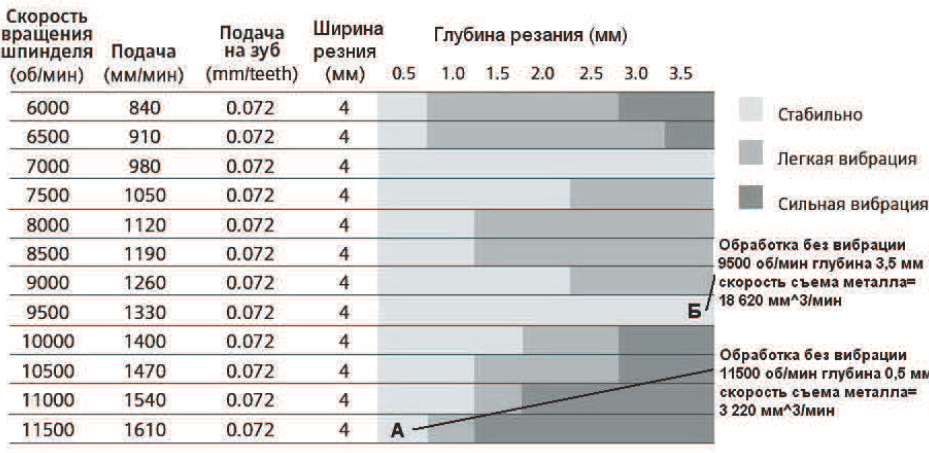
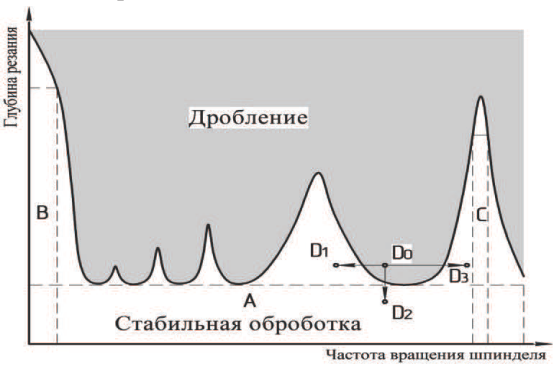
Акустический способ.
Оптимальную частоту вращения шпинделя рассчитывают также, используя программное обеспечение (ПО), с помощью которого проводится анализ акустической информации, полученной через микрофон, подключенный непосредственно к компьютеру. Используется то обстоятельство, что звук, записанный при проходе на скорости резания, при котором это дробление происходит, содержит также информацию, необходимую для прогноза частоты вращения шпинделя, при котором процесс резания стабилен и дробления нет. Использование такого ПО сокращает время и количество заготовок для поиска зон оптимальной обработки, но необходимость пробных проходов сохраняется.
Способ надежен и прост, но достаточно трудоемкий. Можно испортить не одну заготовку прежде, чем режим будет отработан, кроме того, в случае изменения хотя бы одного из параметров, например, вылета инструмента, процедуру поиска придется повторить. Использование специального программного обеспечения сокращает время поиска зон оптимальной обработки, но требует высокой квалификации оператора-наладчика и дополнительного оборудования.
Интересный эффект увеличения стойкости инструмента при ВСО наблюдается при сравнении способов охлаждения. Как показывает график, наибольшая стойкость наблюдается при использовании обдува.
Поскольку тепло концентрируется в стружке, ее надо быстро удалить из зоны резания. Низкая стойкость инструмента при охлаждении объясняется главным образом выкрашиванием, что обусловлено циклическими термическими нагрузками на режущую кромку инструмента. Постоянная тепловая нагрузка, даже на относительно высоких температурах, лучше, чем меняющаяся циклическая нагрузка.
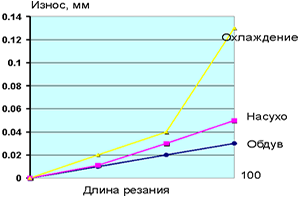
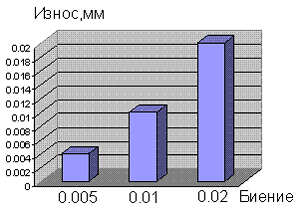
Особые требования предъявляются к точности и надежности инструмента и оснастки. В процессе ВСО на первый план ставят факторы – величина биения фрезы, вибрации, инерционные нагрузки и силы, возникающие при этом (становятся соизмеримыми с силами резания). Биение инструмента сильно влияет на износ. Это подтверждают данные экспериментов из графика на зависимости износа от биения инструмента, где видна практически линейная зависимость износа от биения при высоких скоростях резания. Наиболее предпочтительными для закрепления инструмента являются термооправки и гидропластовые патроны.
Необходимо применение инструментов с термозащитным покрытием твердой поверхности. Даже при использовании самых острых инструментов высокие температуры должны быстро отводиться от инструмента. Среди обычных покрытий TiAlN (нитрид титана-алюминия) является лучшим выбором для улучшения теплоизоляции во время сухой обработки. Но адгезионные характеристики традиционно наносимого однослойного покрытия TiAlN не поддерживают оптимальные характеристики.
Под действием динамического напряжения сухой обработки однослойный TiAlN имеет тенденцию к растрескиванию и отслаиванию инструмента. Многослойное покрытие TiAlN, структура которого препятствует проникновению поверхностных трещин на поверхность инструмента, обеспечивает значительно улучшенные характеристики. Новые покрытия, состоящие из чередующихся ультратонких слоев покрытия TiN (нитрид титана) и TiAlN, дают еще лучшие результаты. Структура сочетает в себе хорошие адгезионные характеристики TiN, высокую термостойкость TiAlN и способность поглощать растрескивание TiCN (карбонитрида титана).
Инструменты должны иметь покрытие, снижающее коэффициент трения на поверхности инструмента (возможно, поверх твердого покрытия), чтобы уменьшить проблему нароста кромки.
Рекомендуется использовать внешнее смазывание туманом для экономичной, почти сухой высокоскоростной обработки. В этом подходе, совместимом с большинством существующих машин, используется система подачи охлаждающей жидкости с распылительной струей, которая создает нанометрическое количество охлаждающей жидкости в тонком тумане воздуха и охлаждающей жидкости, которая постоянно покрывает движущийся инструмент.
Требования к CAM системам.
ВСО предполагает работу с малыми сечениями среза, снимаемые с большой скоростью.
Это реализуется небольшими шагами между проходами, применением трохоидального фрезерования.



Когда ВСО используется для обработки сразу из закаленной заготовки и деталь имеет отверстия, их обработка сверлением представляет собой определенную проблему, вследствие низкой стойкости сверл. В этом случае эффективным способом может быть спиральная расфрезеровка отверстий. Причем, как показывает практика этот метод, как по производительности, так и по стойкости инструмента превосходит сверление.
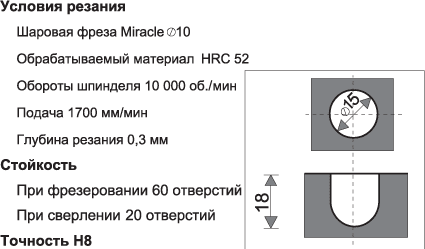
Как результат выполнения этого правила нужно быть готовым, что объем программ для ВСО значительно превосходит объемы традиционных программ силового резания и, как было отмечено выше, системы ЧПУ должны иметь возможность быстро обрабатывать программы, составляющие десятки мегабайт. Большие объемы программ требуют соответственно больших затрат времени на расчет траектории и здесь на первый план выходит скорость расчета, которую обеспечит САМ система. При разработке своей системы PowerMILL фирма Delcam уделяла этому особое внимание и на сегодняшний день она явный лидер по времени расчета и пересчета программ.
Движение инструмента должно проходить по наиболее гладкой траектории, без резких поворотов на углах, обеспечивая равномерную нагрузку на инструмент. Предпочтение должно отдаваться спиральным стратегиям, где инструмент однажды врезавшись, сохраняет непрерывный и равномерный контакт с заготовкой, или стратегиям эквидистантного смещения контура, которые сохраняют контакт инструмента с заготовкой длительное время с одним заходом и выходом.

Это же правило равномерных нагрузок диктует технику обработки внутренних скруглений. При ВСО надо стремиться исключать обработку фрезами с радиусами равными радиусам скругления на детали.
Таким образом, САМ-система для ВСО должна обеспечить:
- широкий набор вариантов гладкого подвода-отвода и связок между проходами;
- набор стратегий спиральной и эквидистантной обработки зон как на чистовой, так и на черновой обработке, и поиск оптимальной стратегии в различных зонах обработки;
- автоматическое сглаживание траекторий в углах;
- исключение проходов полной шириной фрезы и автоматическое применение трохоидального врезания в этих местах;
- оптимизацию подач для сглаживания нагрузки на инструмент.
(фрагменты страниц взяты из брошюры Garant)
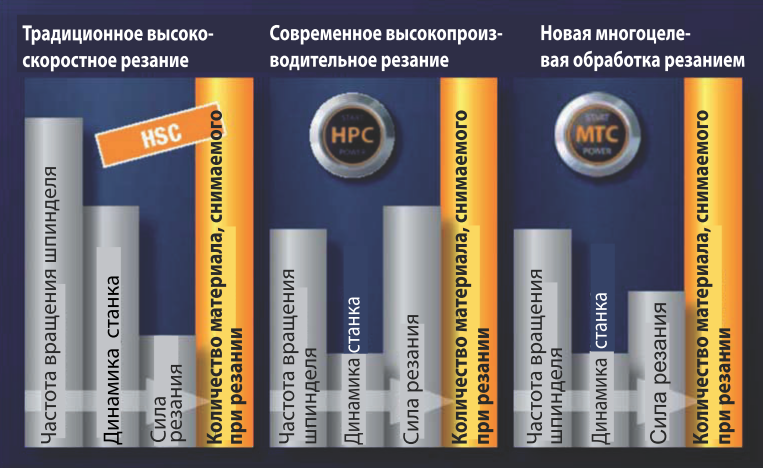

(рисунок взят из брошюры Garant)
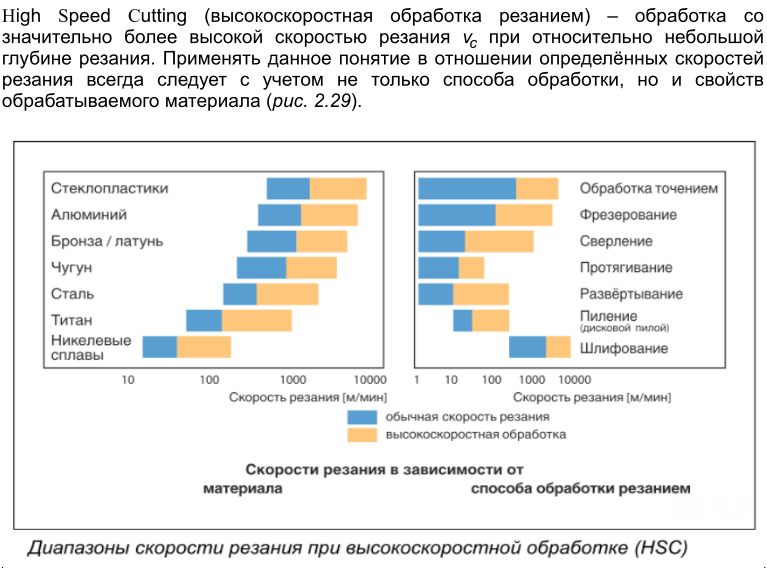
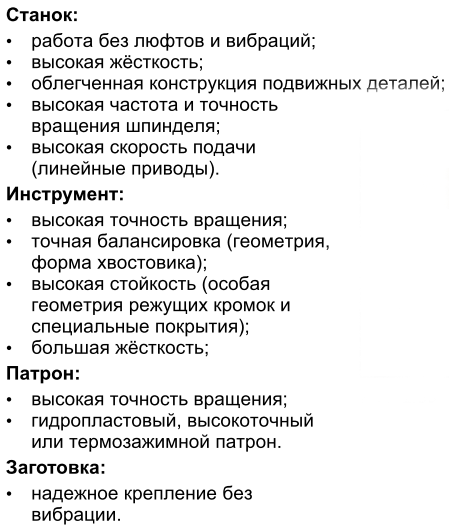
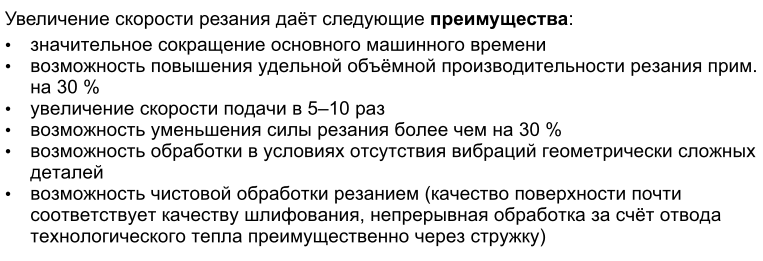
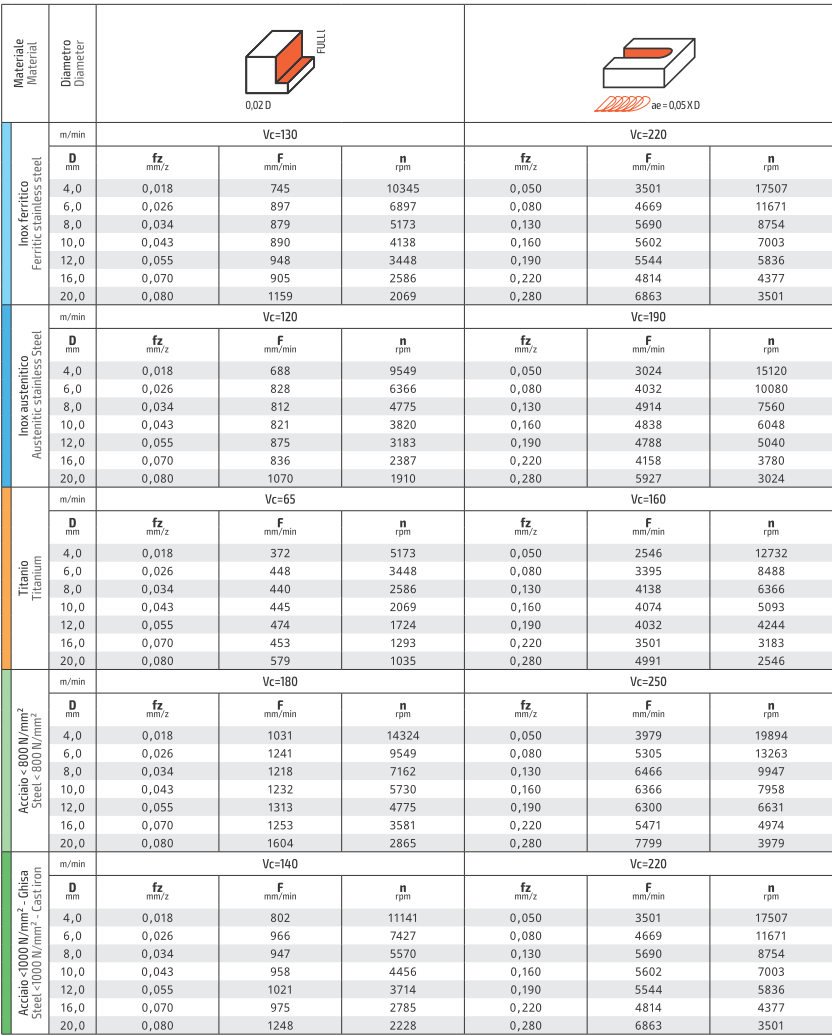
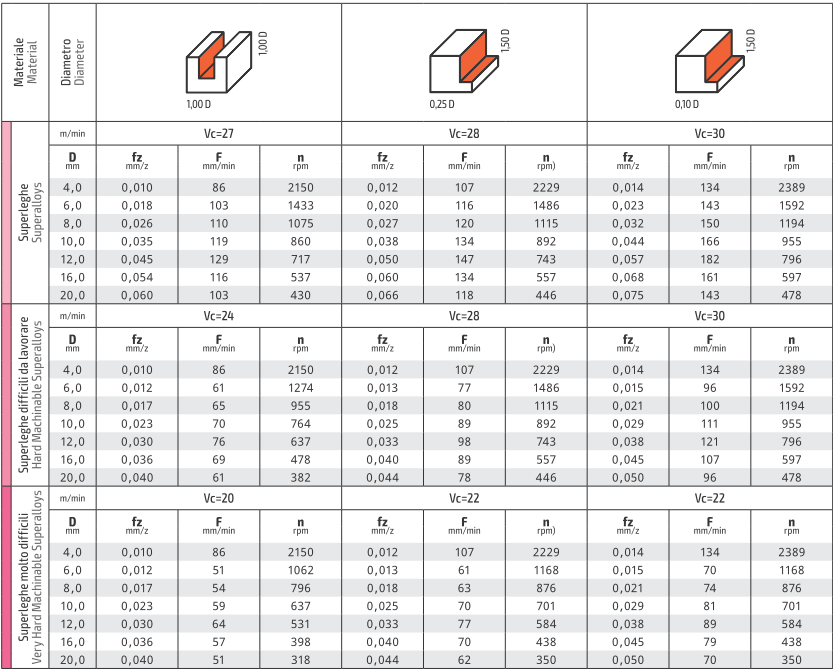
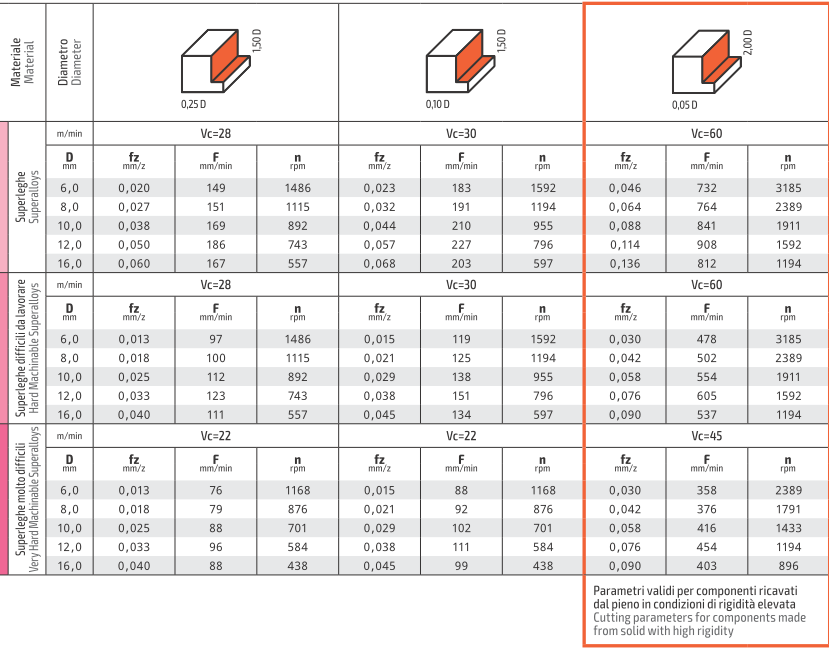
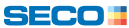
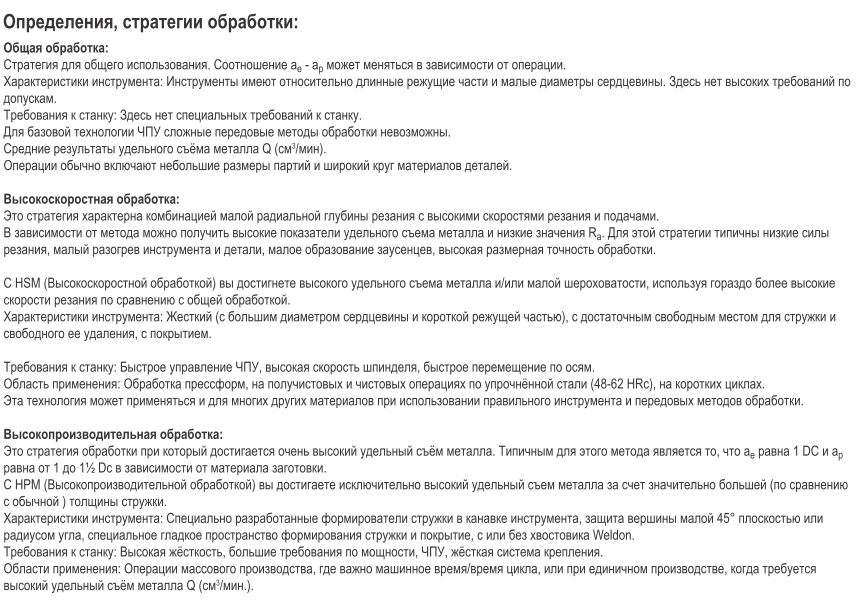
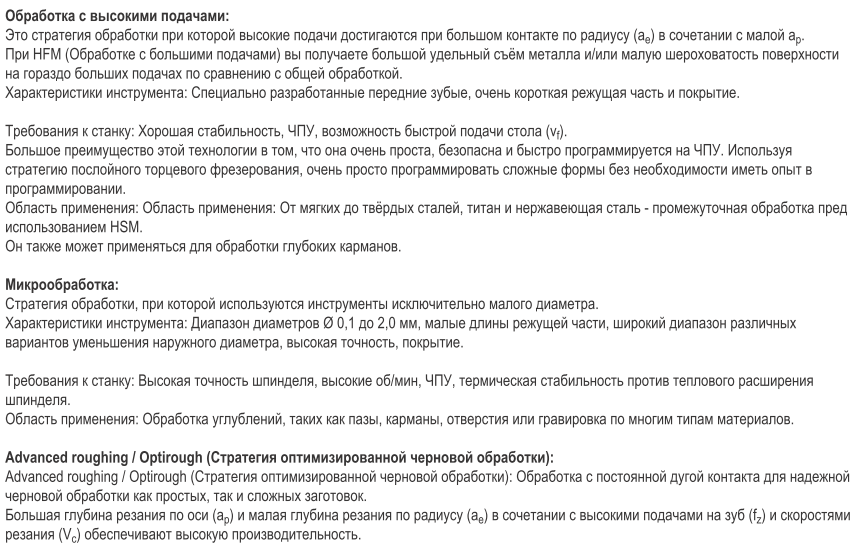
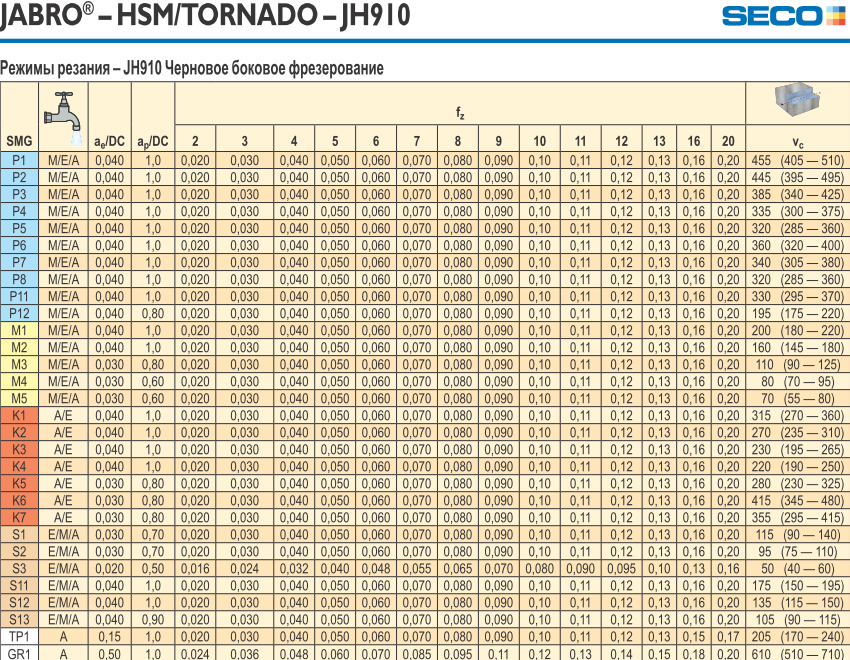
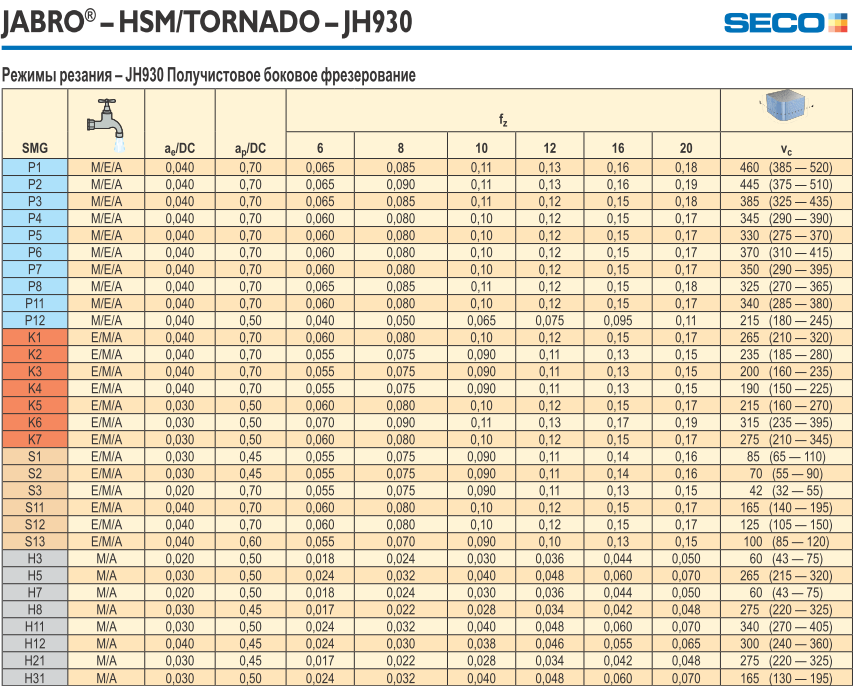
Процесс резания в высокоскоростном фрезеровании отличается от обычной обработки в основном изменённым образованием стружки и её отводом.
Понимание этого процесса очень важно для понимания всей технологии высокоскоростного фрезерования.
Так как образование стружки очень сильно зависит от обрабатываемого материала, необходимо отличать характеристики материала. В дальнейшем процесс описывается при помощи материалов, приводящих к текучей стружке, к так называемым вязким материалам. К ним относится большинство сталей, медь и медные сплавы, а также алюминиевые сплавы.
При обработке вязких материалов, т.е. при фрезеровании или точении, с точки зрения металлографии, происходит деформация из-за смещения по плоскостям скольжения. В области резки происходит длительное образование стружки, которое в дальнейшем приводит к возникновению текучей стружки. На режущем клине, т.е. на резце фрезы, одновременно идёт три процесса:
1. Пластическая деформация и дальнейшая резка материала в плоскости резания.
2. Процессы трения из-за движения между отходящей стружкой и передней гранью режущего инструмента.
3. Процессы трения из-за движения между созданной, обработанной поверхностью заготовки и задней поверхностью инструмента.
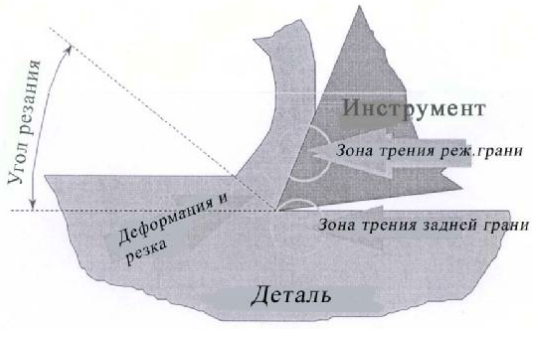
Обрабатываемый материал оказывает сопротивление пластической деформации.
Высокоскоростное фрезерование.
Оно сильно зависит от материала, а также от температуры и скорости деформации. (Скорость деформации зависит от скорости резания).
Сопротивление деформации падает с повышающейся температурой материала. Однако увеличивается при повышающейся скорости деформации.
В основном замечено повышение сопротивления деформации при более высоких скоростях резания.
Трение между двумя подвижными частями описывается при помощи кулоновского закона трения. Коэффициент трения при этом принимается за постоянное значение.
Однако в высокоскоростной обработке эта гипотеза не подтверждается. Коэффициент трения уменьшается при повышении скорости резки. В нижней части, т.е. в месте контакта между инструментом и материалом в отдельных экстремальных случаях, может возникнуть образование расплавленного слоя, т.е. достигается температура плавки фрезеруемого материала.
Из-за этого уменьшается трение поверхности между передней гранью и осколками материала. Сплющивание стружки уменьшает и увеличивает её искривление. Уменьшение сплющивания стружки даёт нам увеличение угла среза и приводит тем самым в целом к уменьшенному процессу деформации. Нагрев детали в основном обусловлен процессами в зоне резания и деформации.
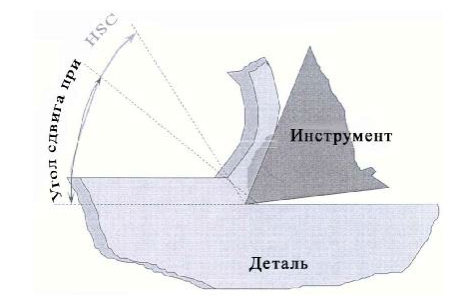
Нагрев детали из-за трения задней грани, повышающийся при увеличении скорости резки, не является столь существенным и составляет меньше 5 %.
Такой ход стружки, значительно облегчённый в HSC-области, приводит к тому, что в процессе выделяется меньше тепла, чем в обычной области. Используя смазку передней грани (нижняя сторона стружки – поверхность инструмента), реализуется либо распылительным охлаждением, либо смазкой, этот эффект можно поддерживать.
Малые частички масла, смешавшиеся с воздухом, оседают на резце инструмента раньше, чем это происходить при использовании охладительных эмульсий. Подобного эффекта при использовании струйного облива в большинстве случаев достичь нельзя, или только при использовании высокого давления. Дополнительно твёрдые сплавы охлаждаются постоянным воздушным потоком не мгновенно, а тепло отводится равномерно с использованием постоянного воздушного потока.
Износ задней поверхности инструмента также, как и в обычной области фрезерования, является доминирующим фактором износа. При увеличении скорости резки уменьшается срок службы.
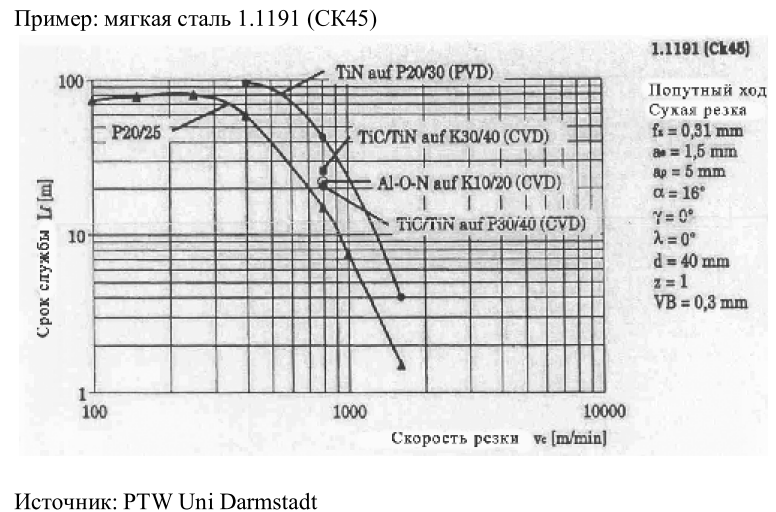
Изменение образования и хода стружки являются одними из наиболее важнейших аспектов высокоскоростной обработки. Поиск оптимальных условий в этой области зависит большей частью от следующей пары:
обрабатываемый материал и инструмент, т.е. покрытие. Наряду с термической обработкой материала большое значение имеют материал для резания, геометрия шлифования и качество, а также покрытие.
Важно:
Между областью обычной скорости обработки и высокоскоростной областью находится зона скорости резания, в которой экономная разумная обработка невозможна, т.е. ещё невозможна, так как эффект изменённого образования стружки реализовать ещё невозможно.
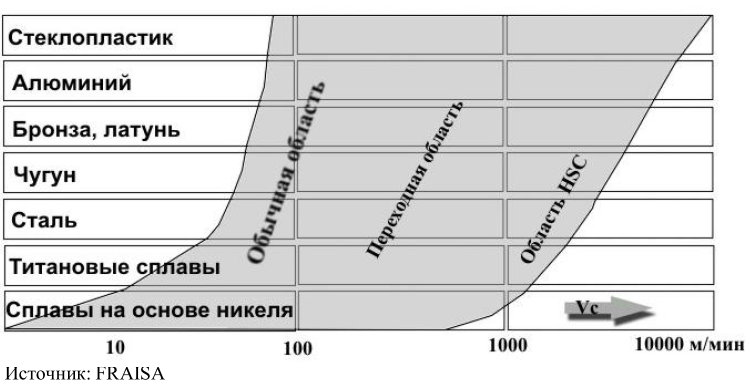
В высокоскоростном фрезеровании больше нельзя использовать традиционную формулу для расчета числа оборотов. Эта формула предназначена для концевой фрезы. А эффективный диаметр шаровой фрезы зависит от осевой подачи или от угла контура. Поэтому при фрезеровании по копиру, фрезеровании отверстия, вытяжном фрезеровании нельзя выбирать столь важную в процессе высокоскоростного фрезерования постоянную скорость резания. Особенно это влияет на износ инструмента, точность инструмента и качество поверхности. Поэтому в процессе высокоскоростного фрезерования предпочитается горизонтальное фрезерование (z-level milling), а также фрезерование контура (contur milling) из-за приблизительно постоянной скорости резания.
Горизонтальное фрезерование / плоское фрезерование шаровой фрезой:
Следующая таблица показывает наиболее часто употребляемый эффективный диаметр при различной осевой подаче.
При фрезеровании контура крутых плоскостей можно рассчитать эффективный диаметр инструмента с углом контура для шаровой и тороидальной фрезы следующим образом:




Степень гибкости инструмента определяется как соотношение выступающей из крепления инструмента длины инструмента к диаметру инструмента. Этим в основном определяются колебания при фрезеровании.
Исследования показали, что для значения К2 (коэффициент твёрдости материала) сначала примерно до HRC52 получается узкая область от 0.1 до 0.12. От HRC 52 до HRC 60 этот коэффициент падает до 0.04 – 0.05. Значение К3 (коэффициент гибкости инструмента) имеет до степени гибкости 5 (5хдиаметр) значение 1. После 5 К3 резко уменьшается. В твёрдом состоянии при определённых условиях (конический стержень и коническая степень только 2-3 градуса) можно выполнять работы, которые имеют степень гибкости 8-10. К3 тогда имеет значения от 0.1 до 0.2.

В зависимости от стабильности шпинделя, структуры инструмента или свойств материала на практике в любое время можно выявить различия. В других материалах это соотношение может улучшиться. В особенности при работе с материалами, имеющими меньшее сопротивление при фрезеровании, такие как графит, медь и т.д. можно ожидать лучших результатов. (Так как геометрия резца соответствует требованиям детали).
Избежание чрезмерного отклонения инструмента можно осуществить уменьшением выступа инструмента или использованием большего диаметра инструмента.
- → 20% уменьшения выступа понижает отклонение инструмента на 50%.
- → 20% больший диаметр (например, диаметр 10 → диаметр 12) понижает отклонение инструмента на 50%.
Следующие испытания обосновывают эти знания. Испытания проводились с диаметром шаровой фрезы 10 R5.
Цель испытаний: определить лимиты подач шаровой фрезы. На пластине материала 1.2767 размером 100*100 твёрдостью HRC54 проводились следующие испытания:
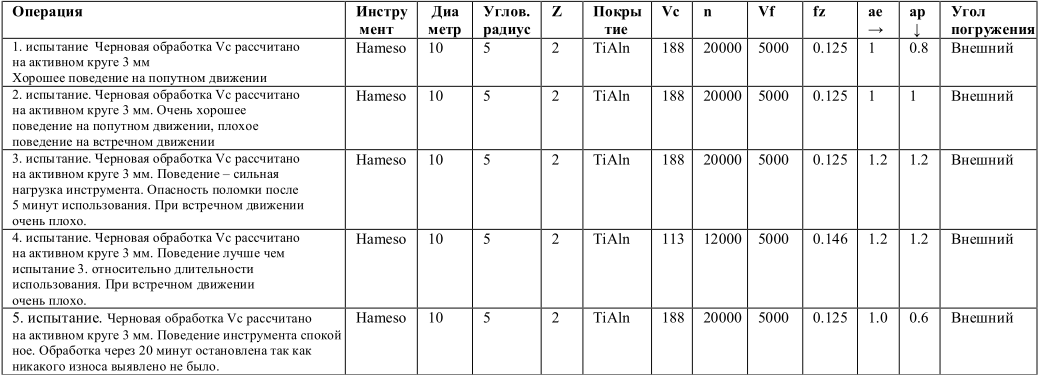
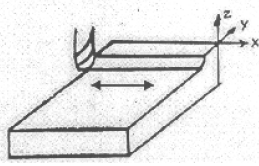
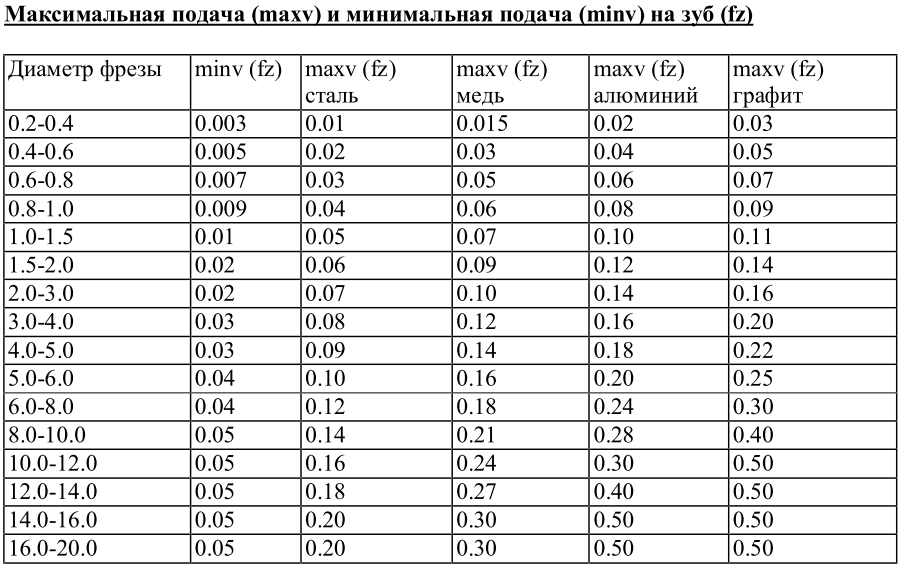
Испытания показали, что с глубиной резания Ар с 5-6%, а также боковой подачей Ае примерно с 8-10% диаметра инструмента можно работать.
При большем количестве деталей с крутыми стенками, когда номинальный диаметр 10 находится в зацеплении, скорость резания становится соответственно слишком большой (при N = 20000 RPM -->628 м/мин).
Плоские детали (в операциях с постоянным Z-level) можно таким образом с этим числом оборотов выполнять черновую обработку быстрее. Если количество переходов с крутыми стенками большое, Z-подача Ар не должна быть больше 5% диаметра, так как угол обхвата на боковой части больше, чем в обычном процессе черновой обработки.
Наиболее чётко это просматривается на примере №5: прерывистая подача на глубину оказывает большое влияние на срок службы и спокойный ход.
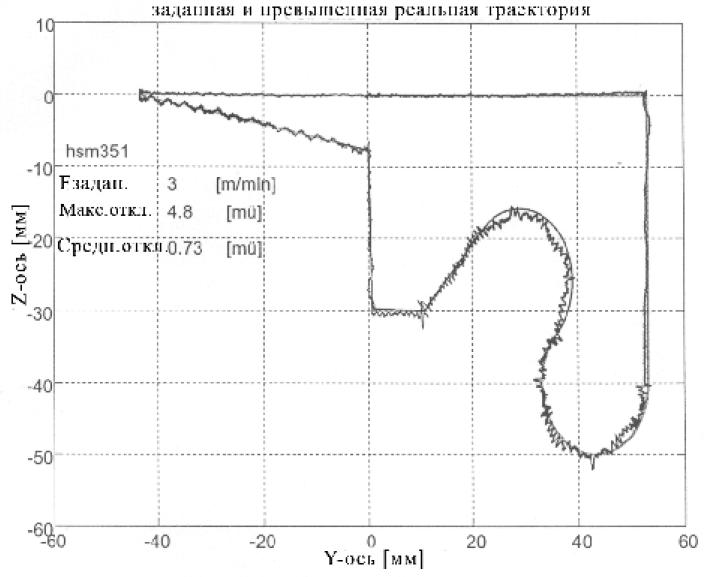
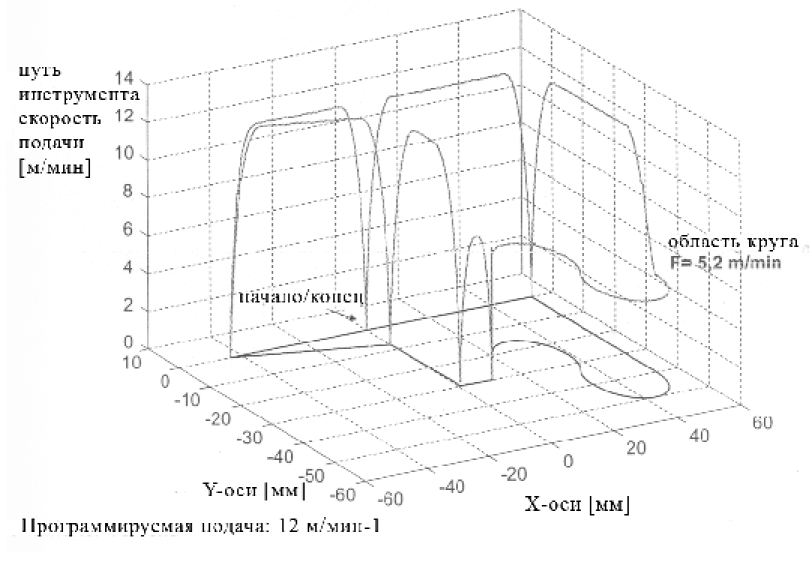
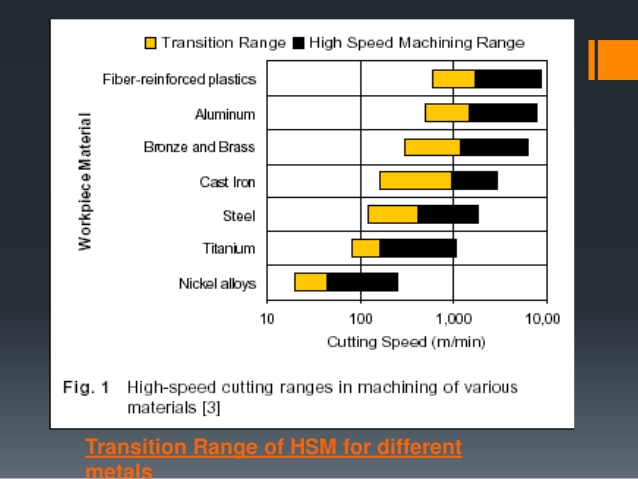
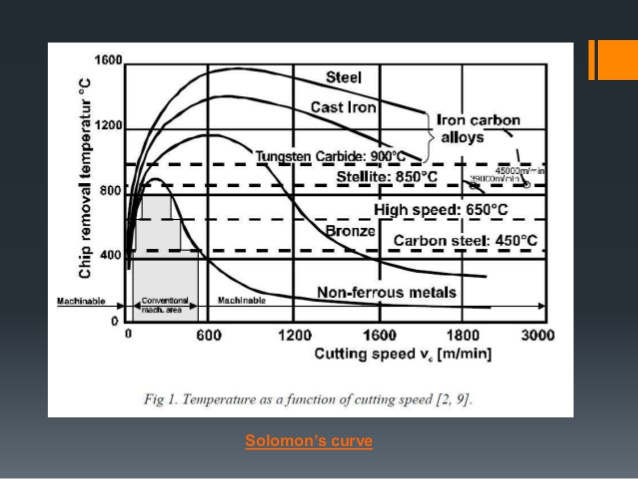
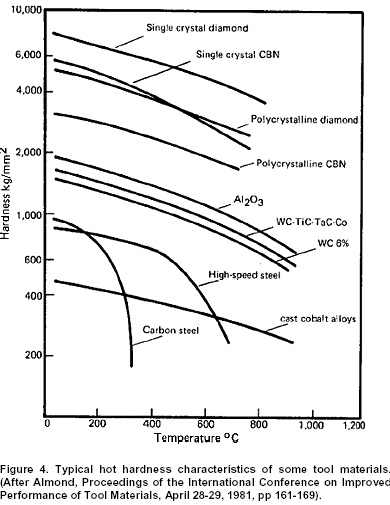
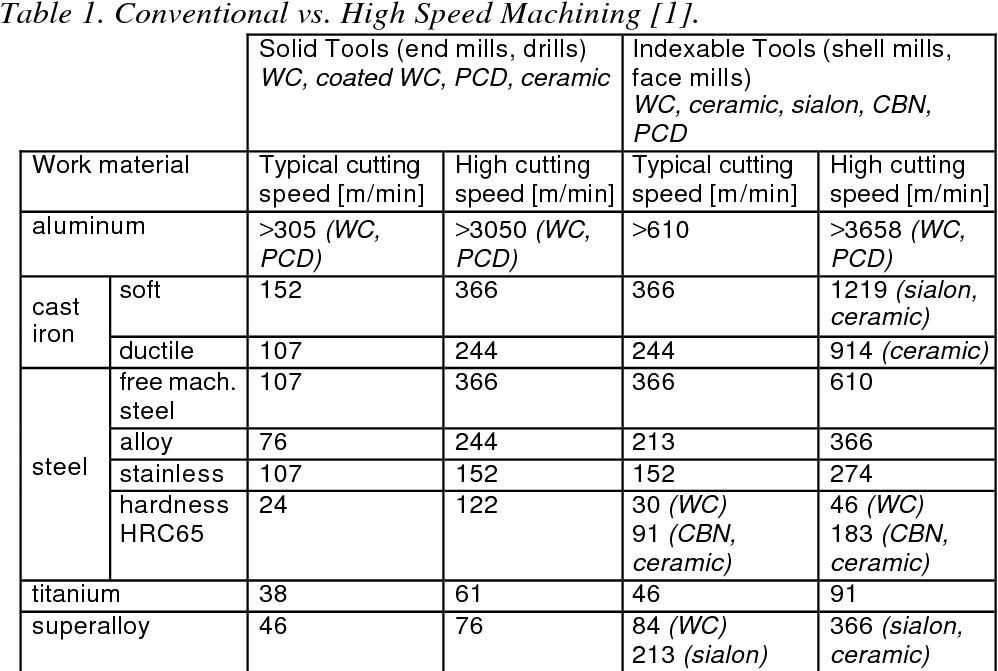
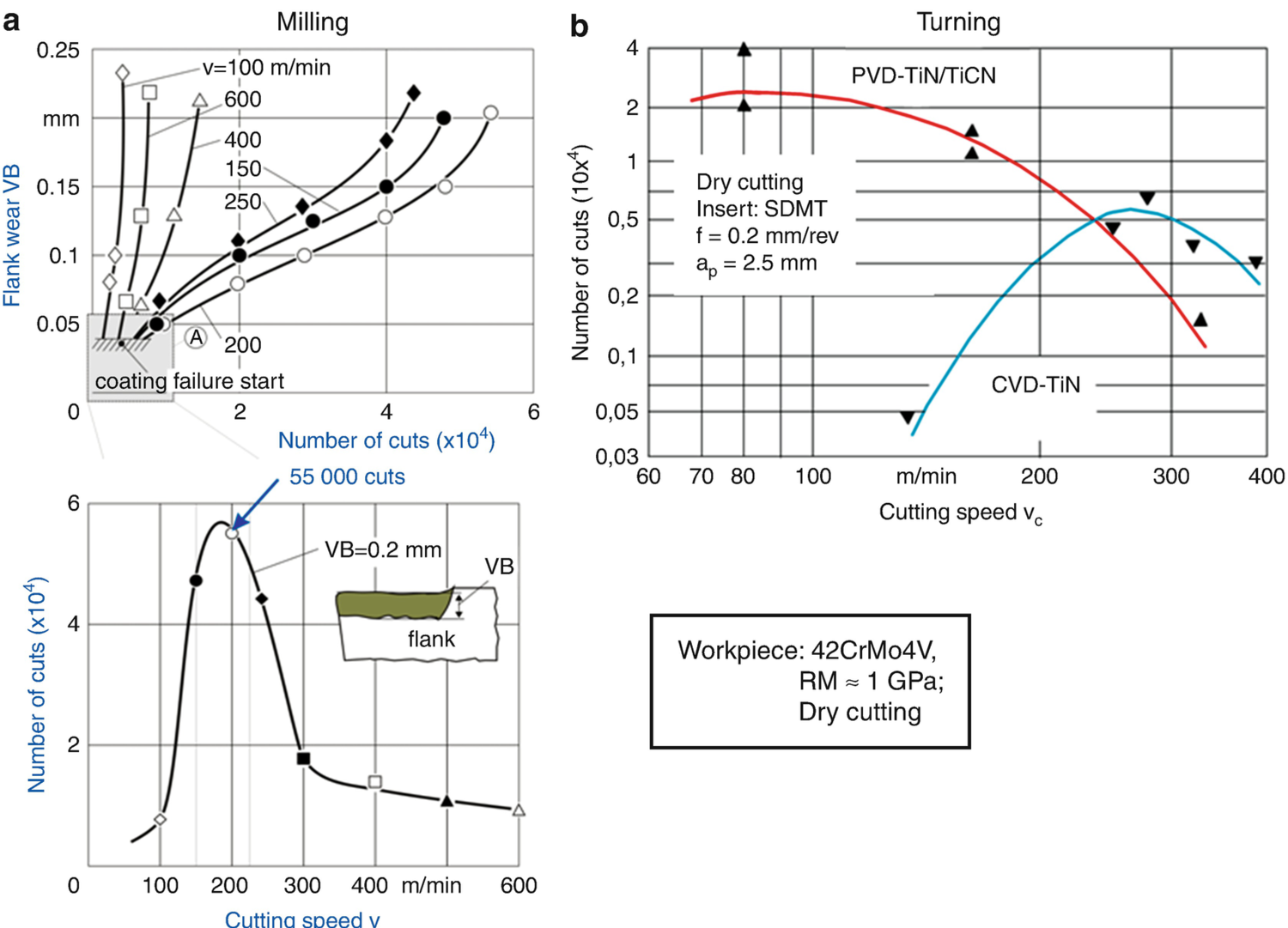
Интересные статьи:
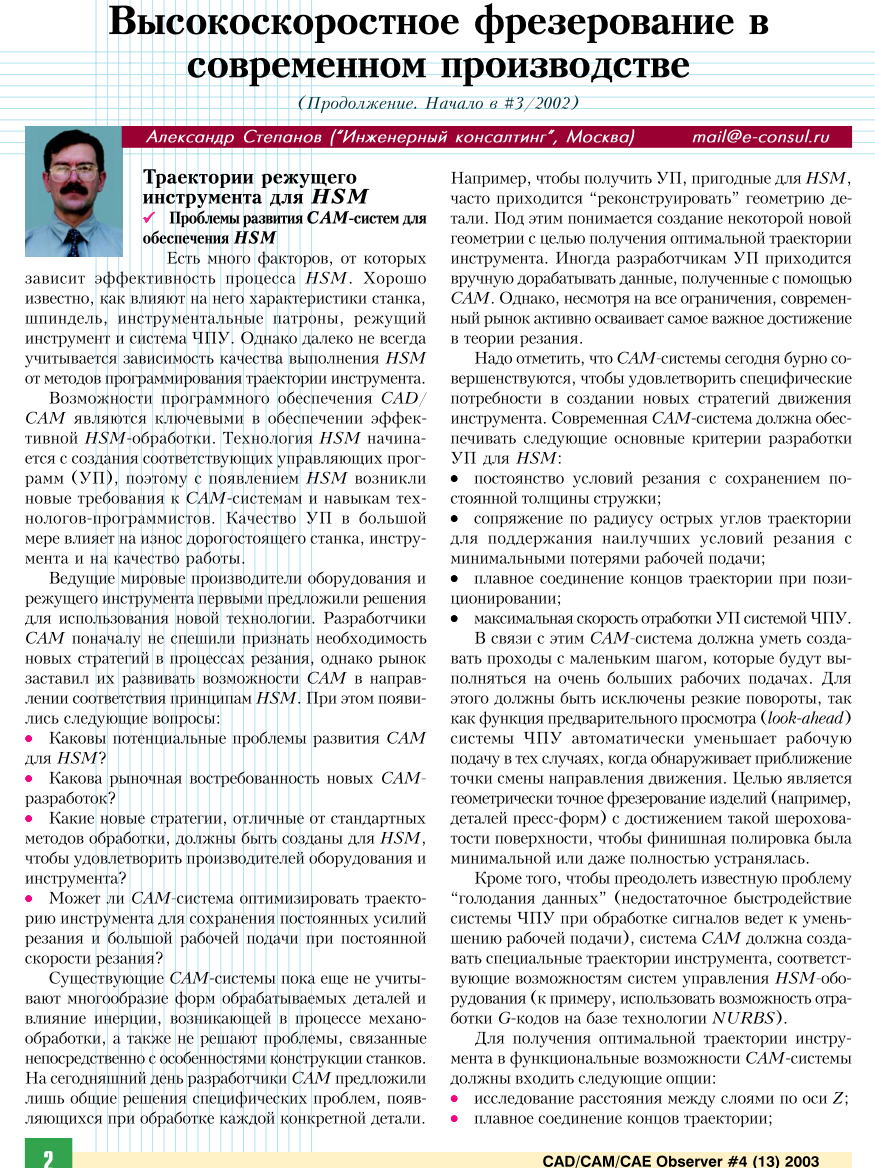
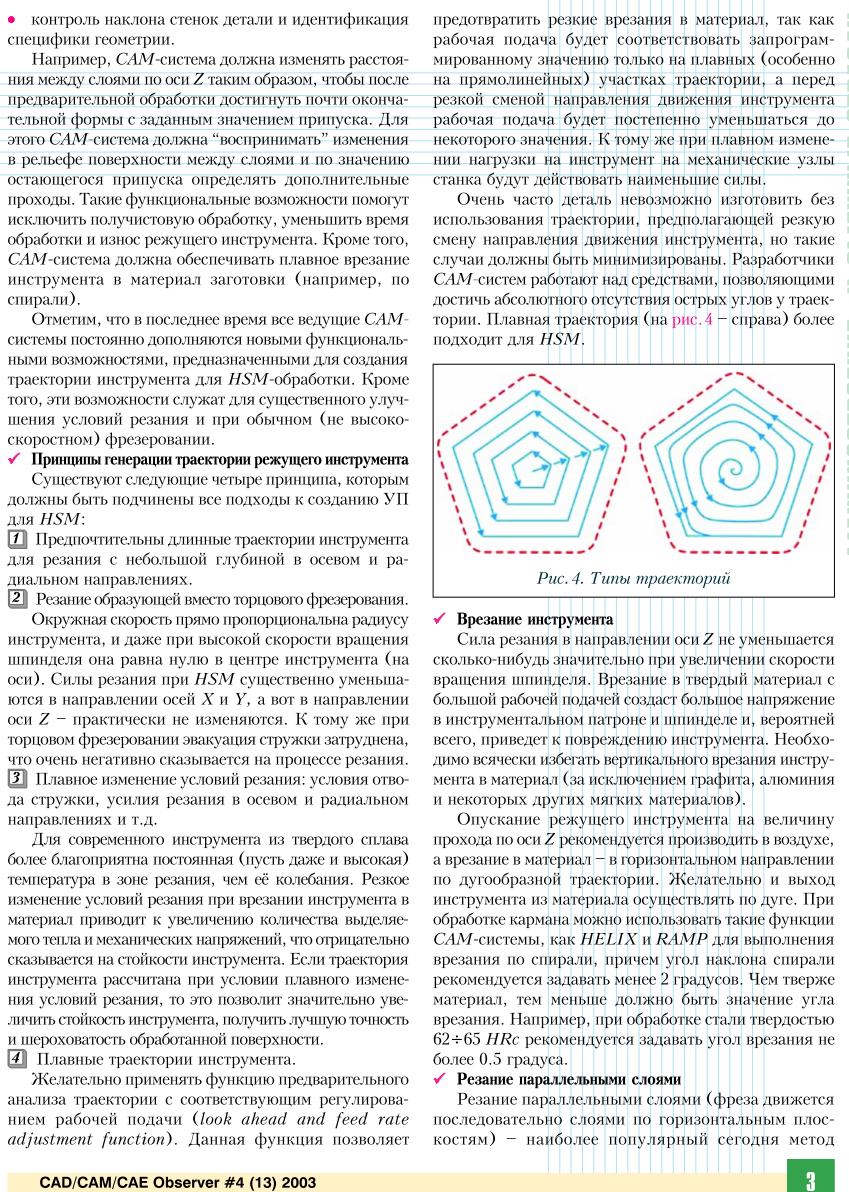
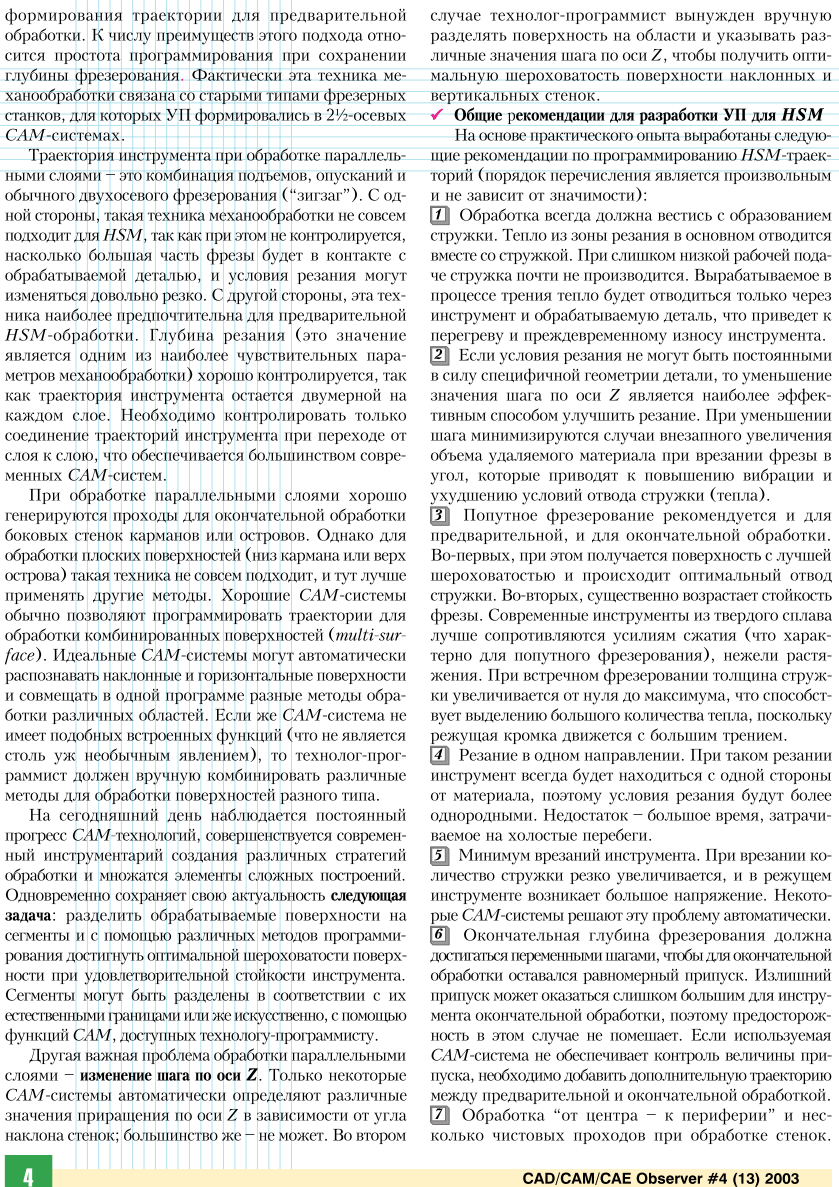
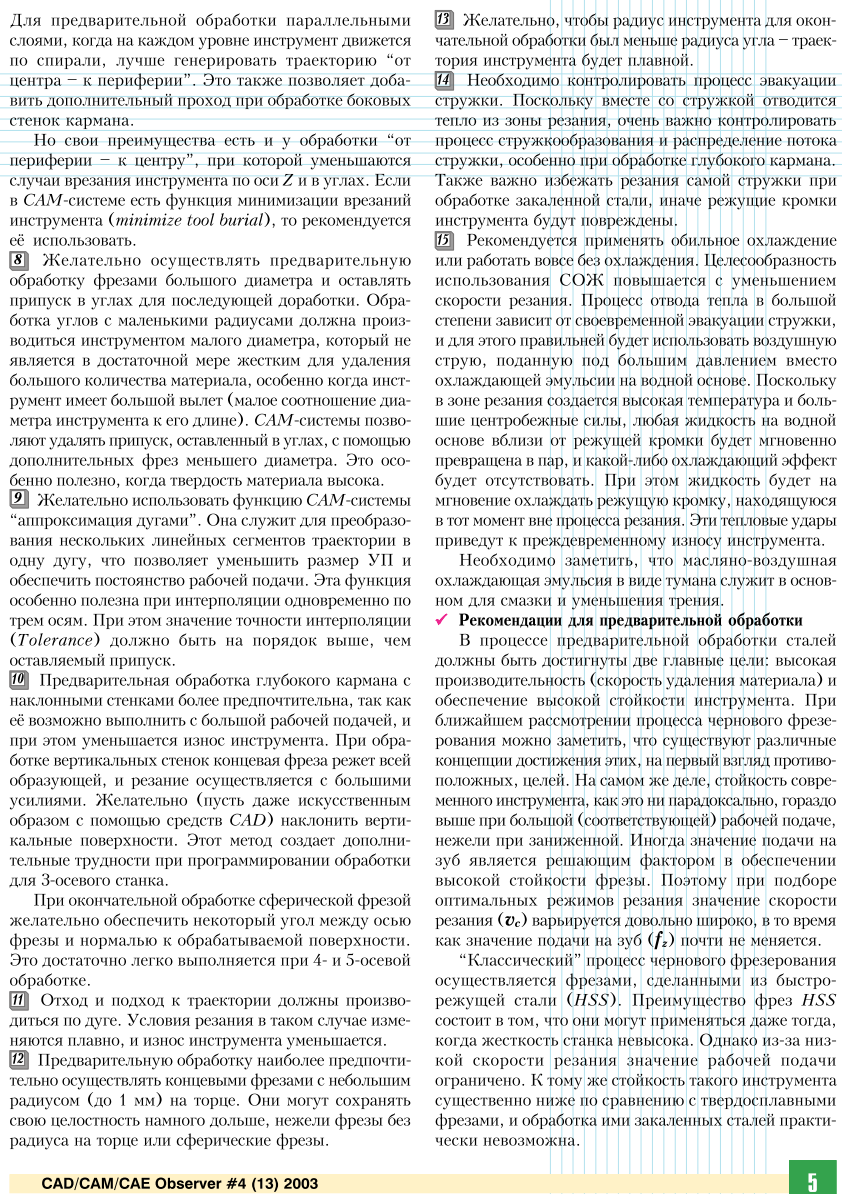
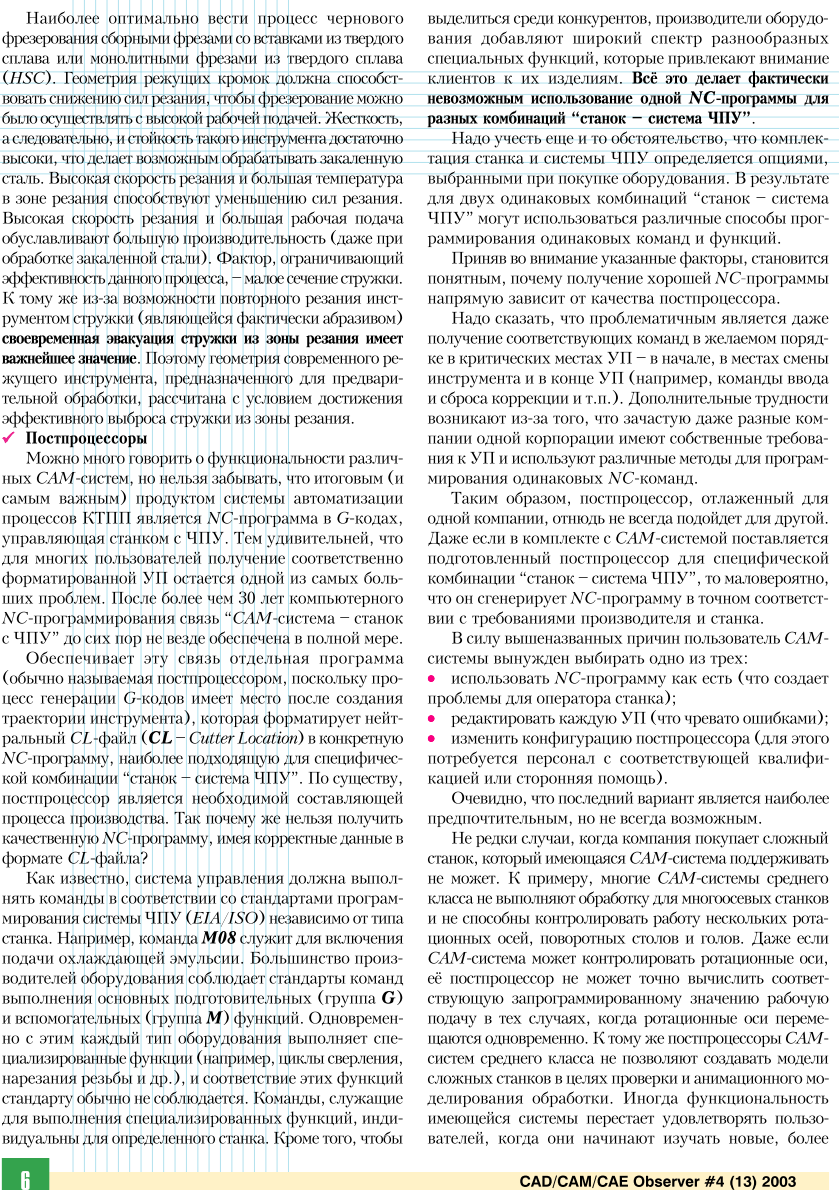
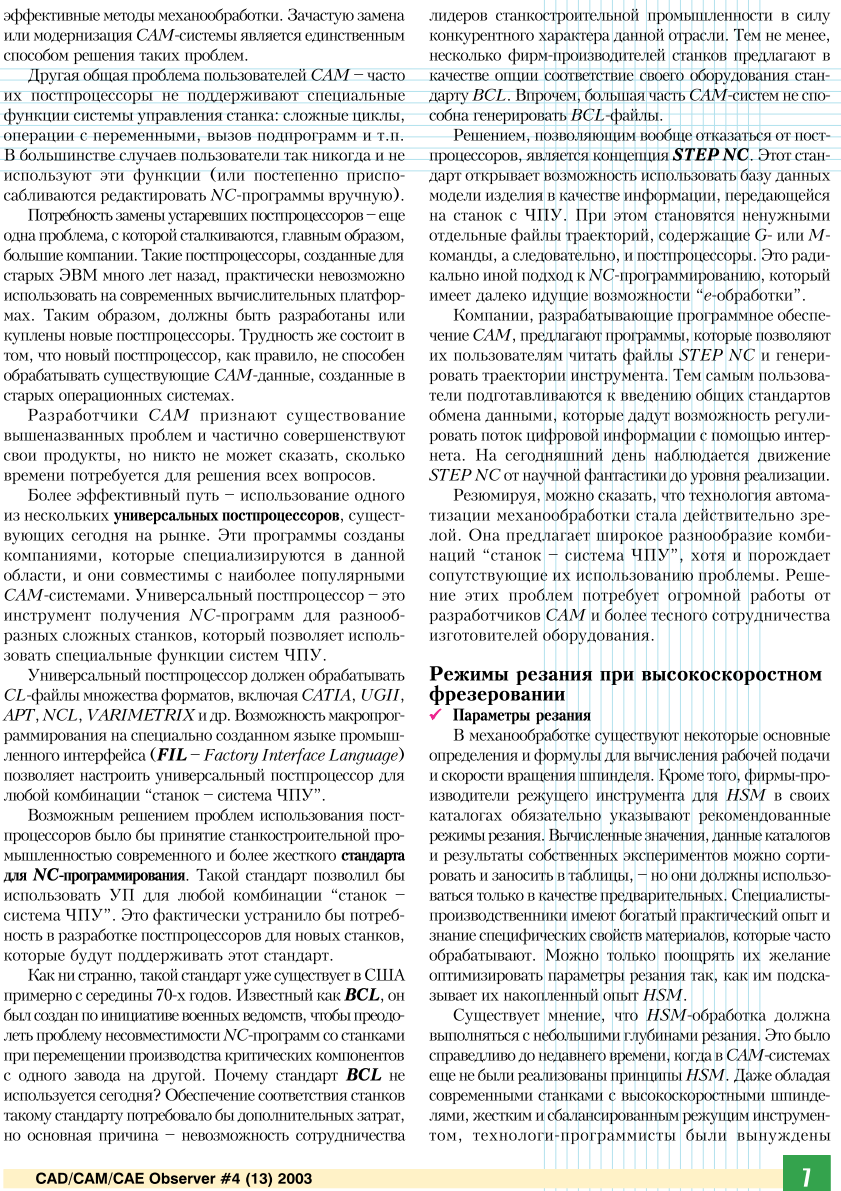
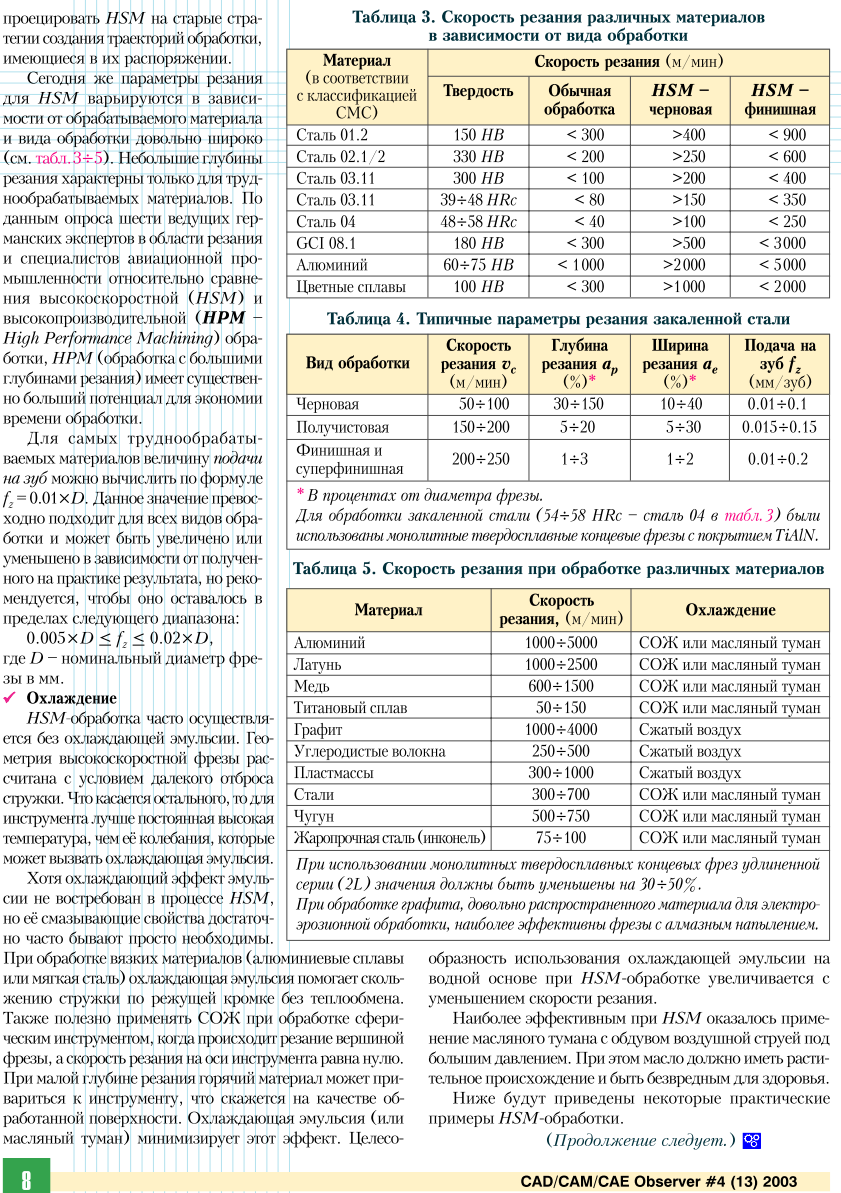
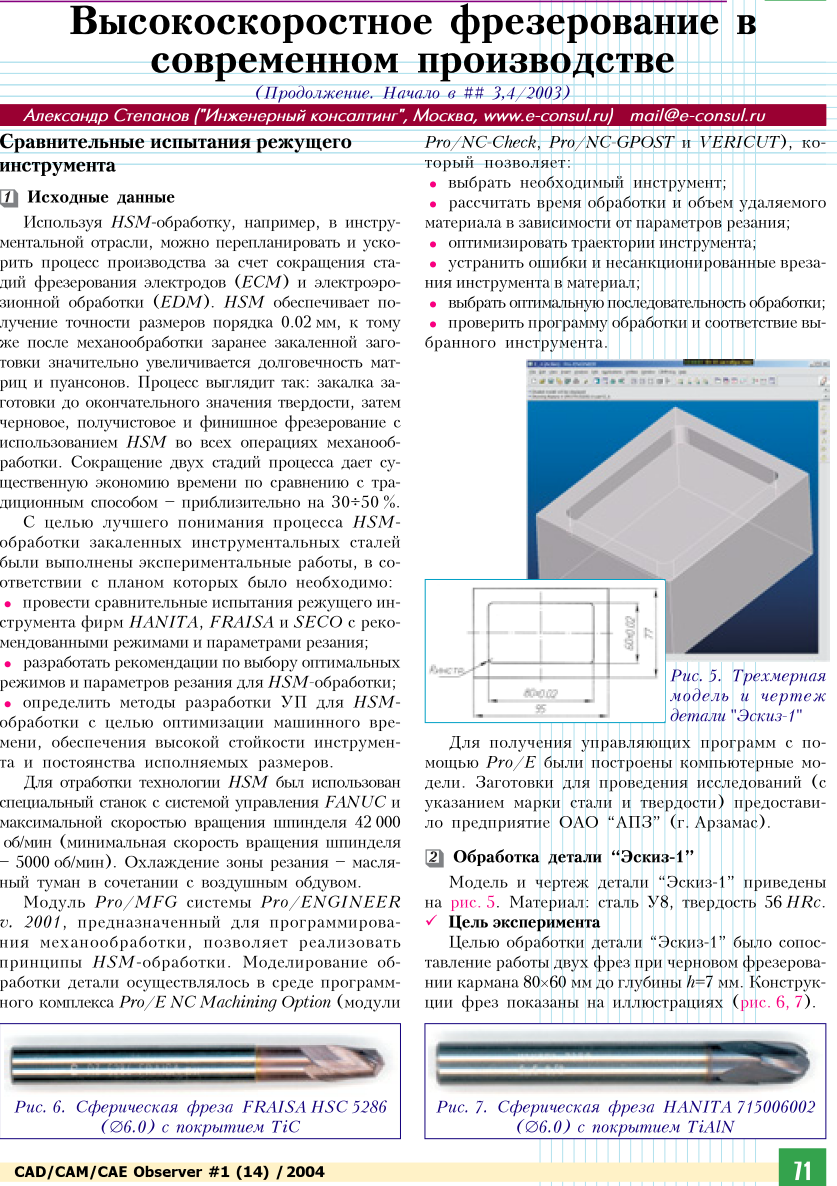
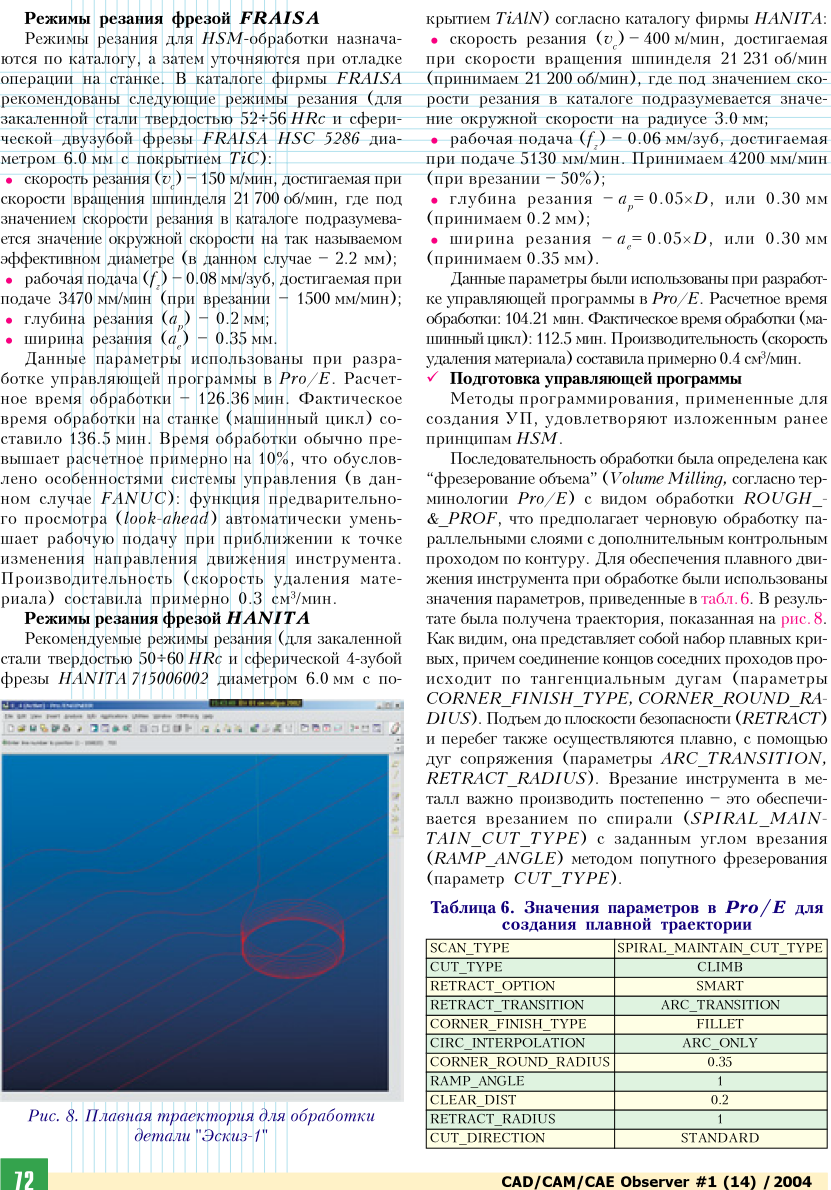
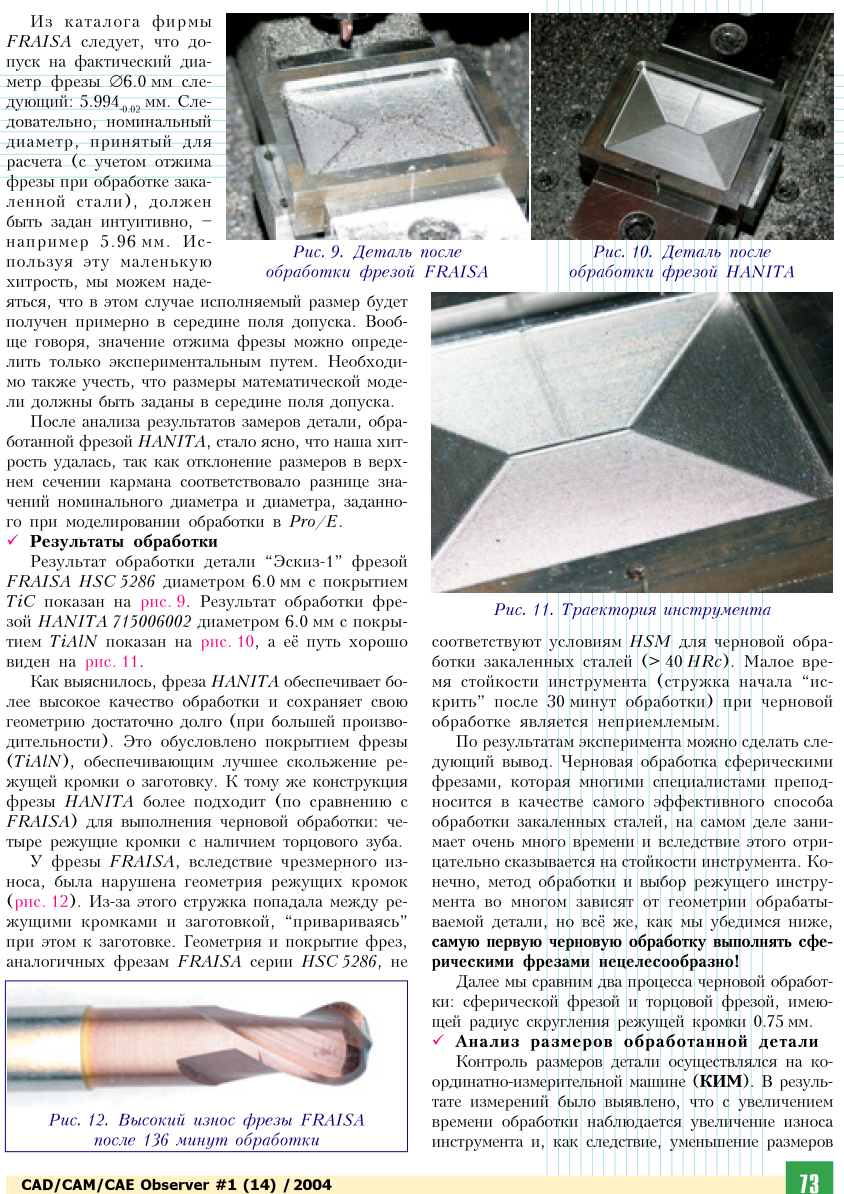
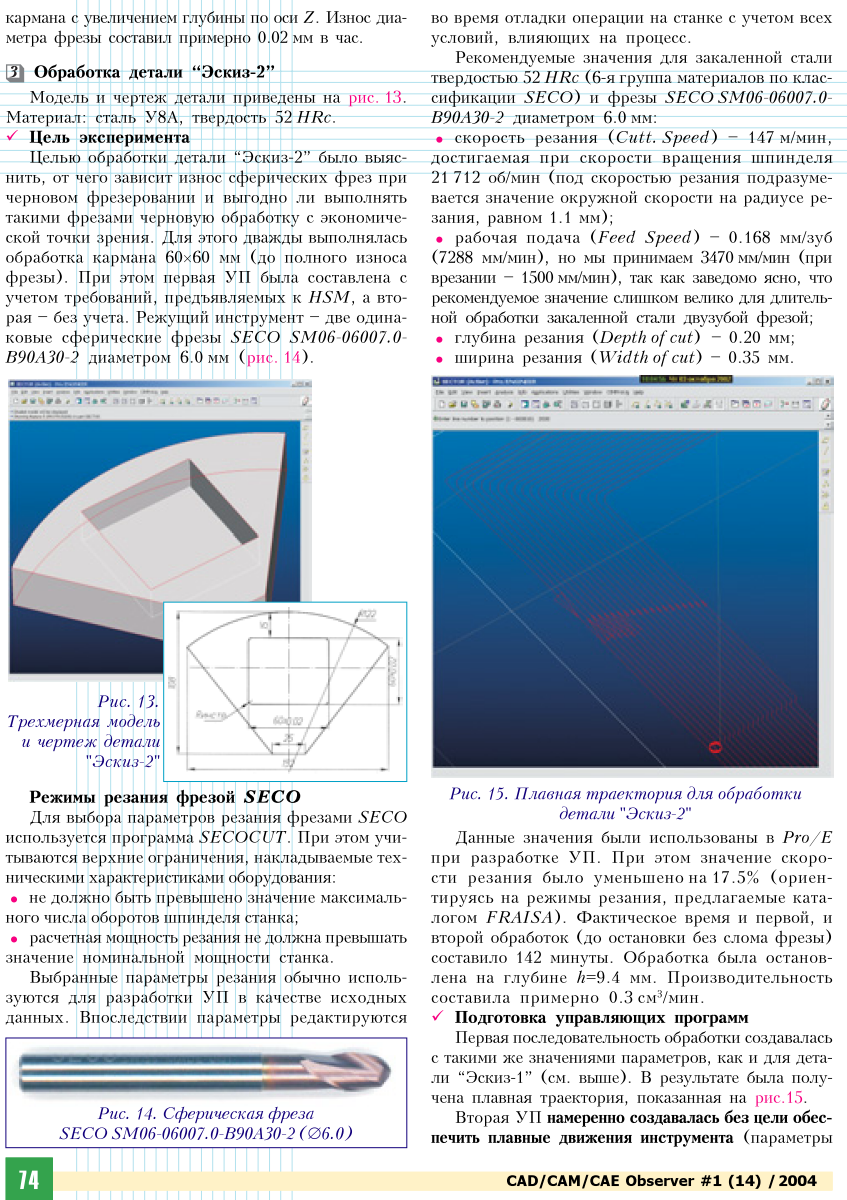
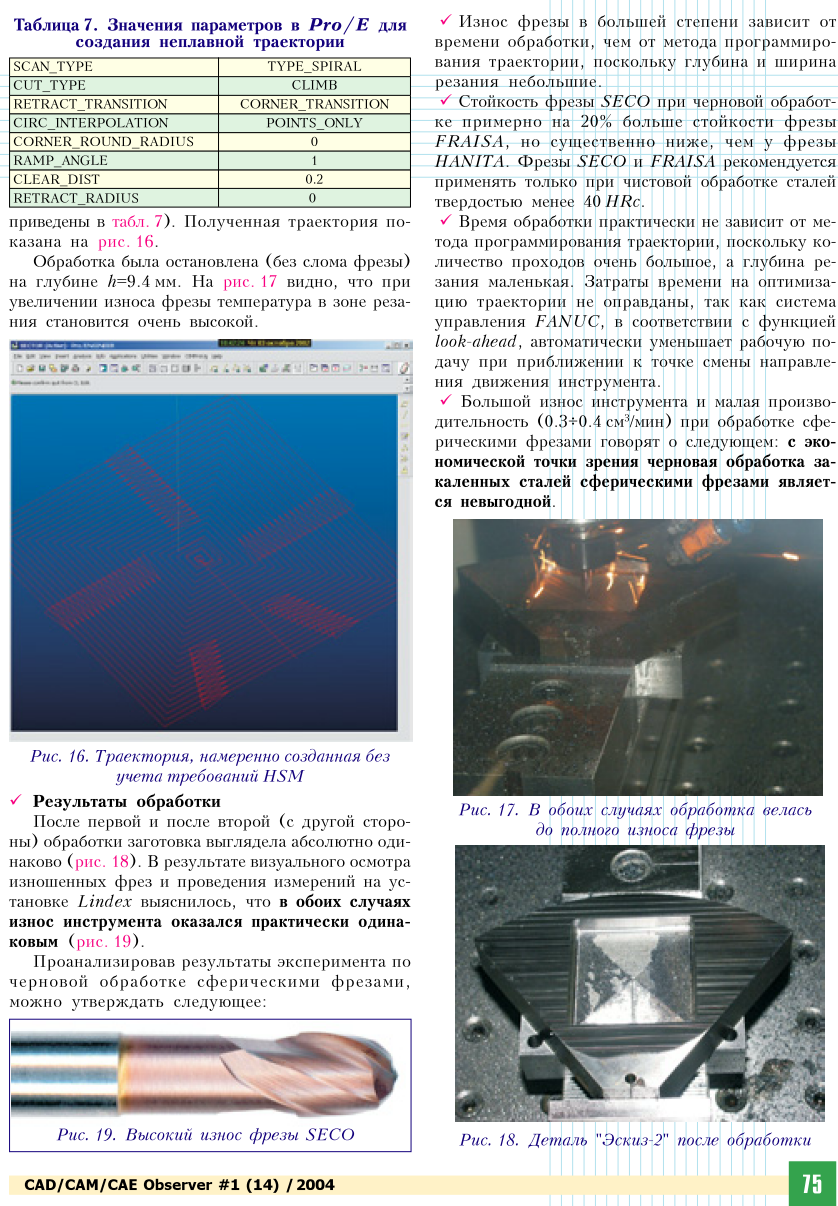
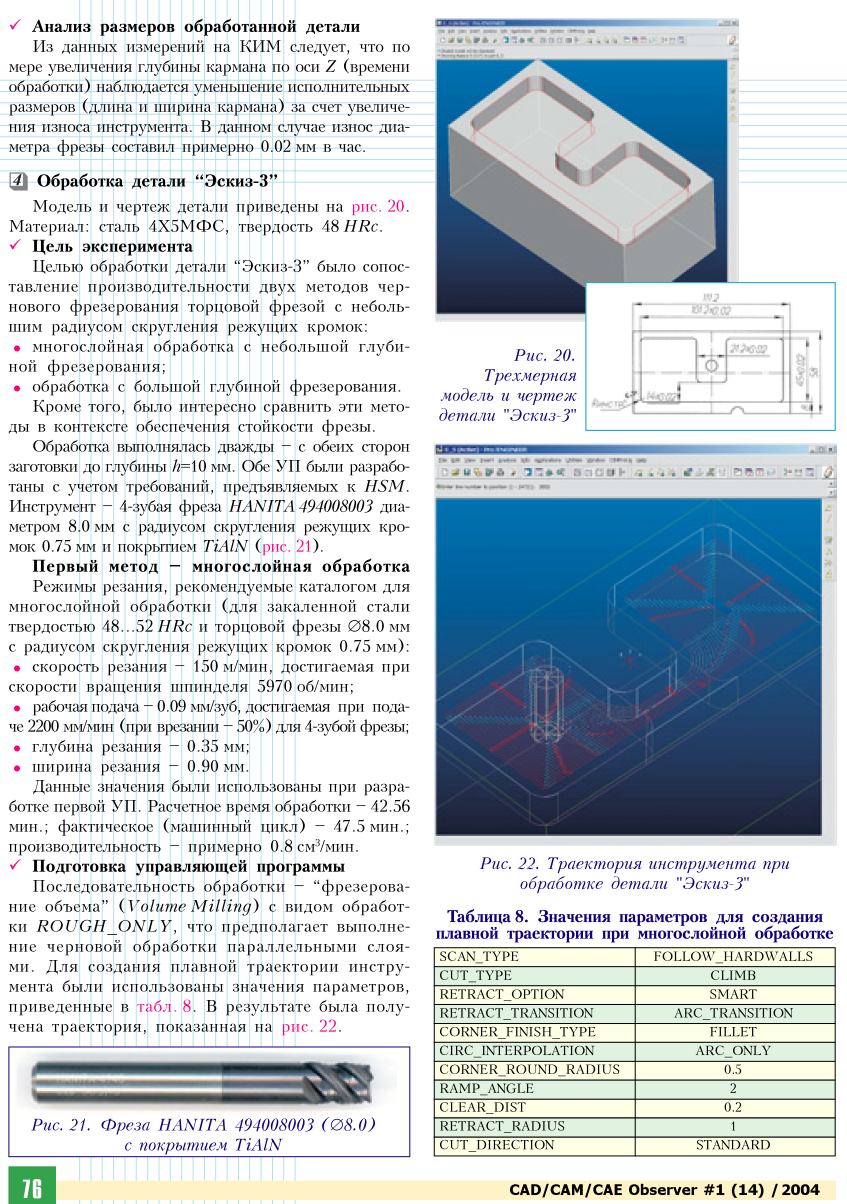
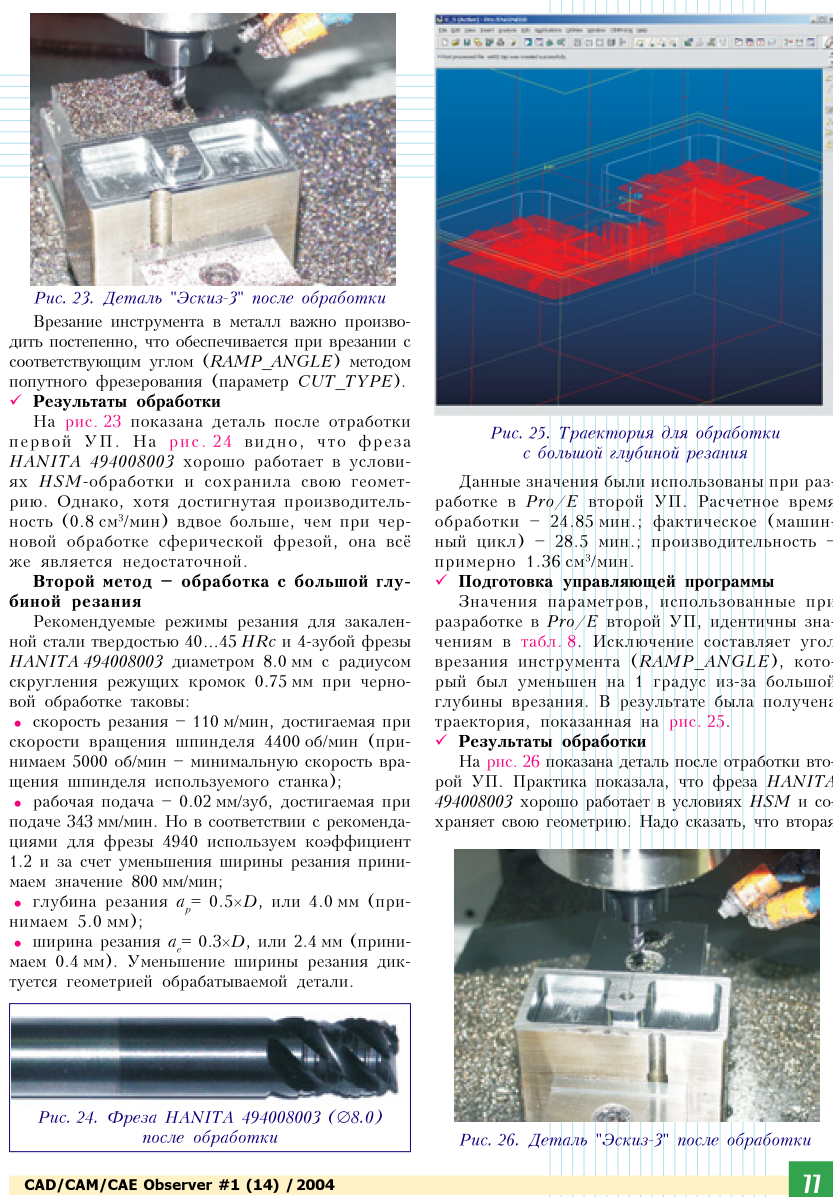
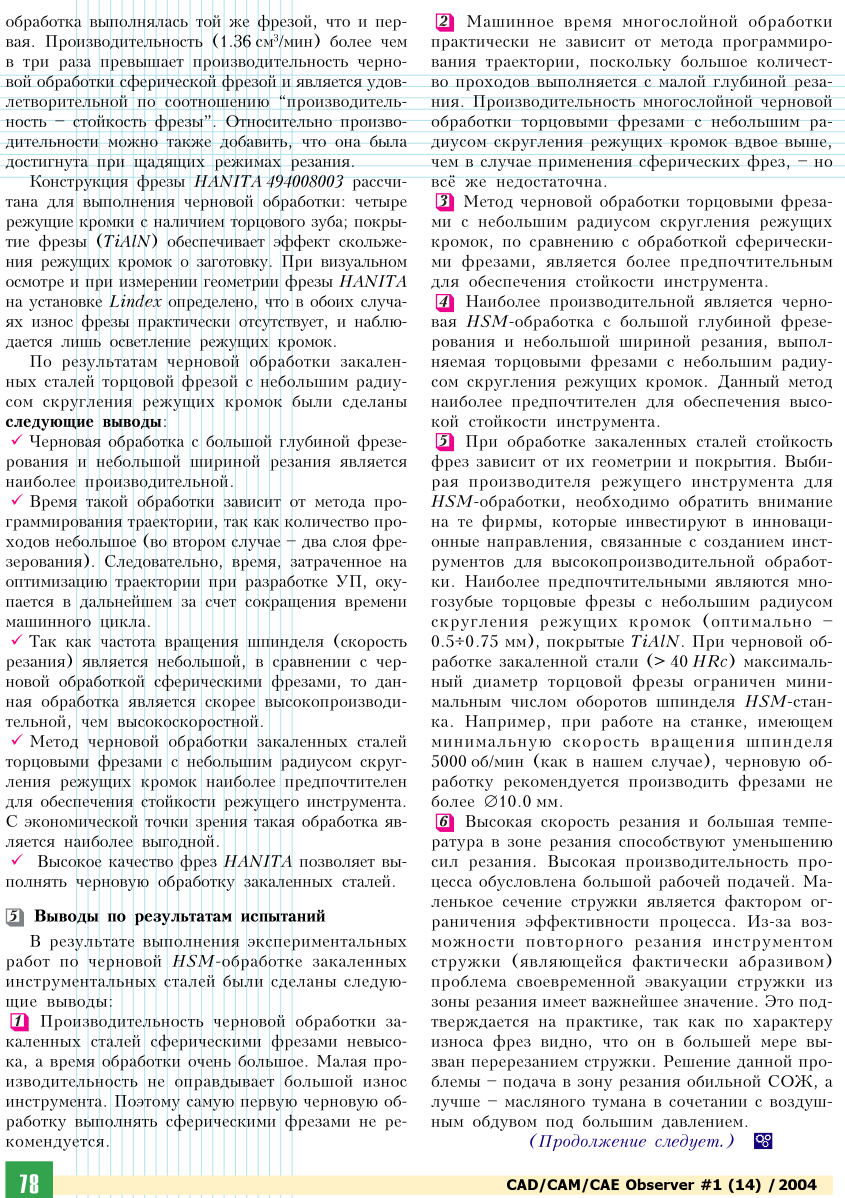
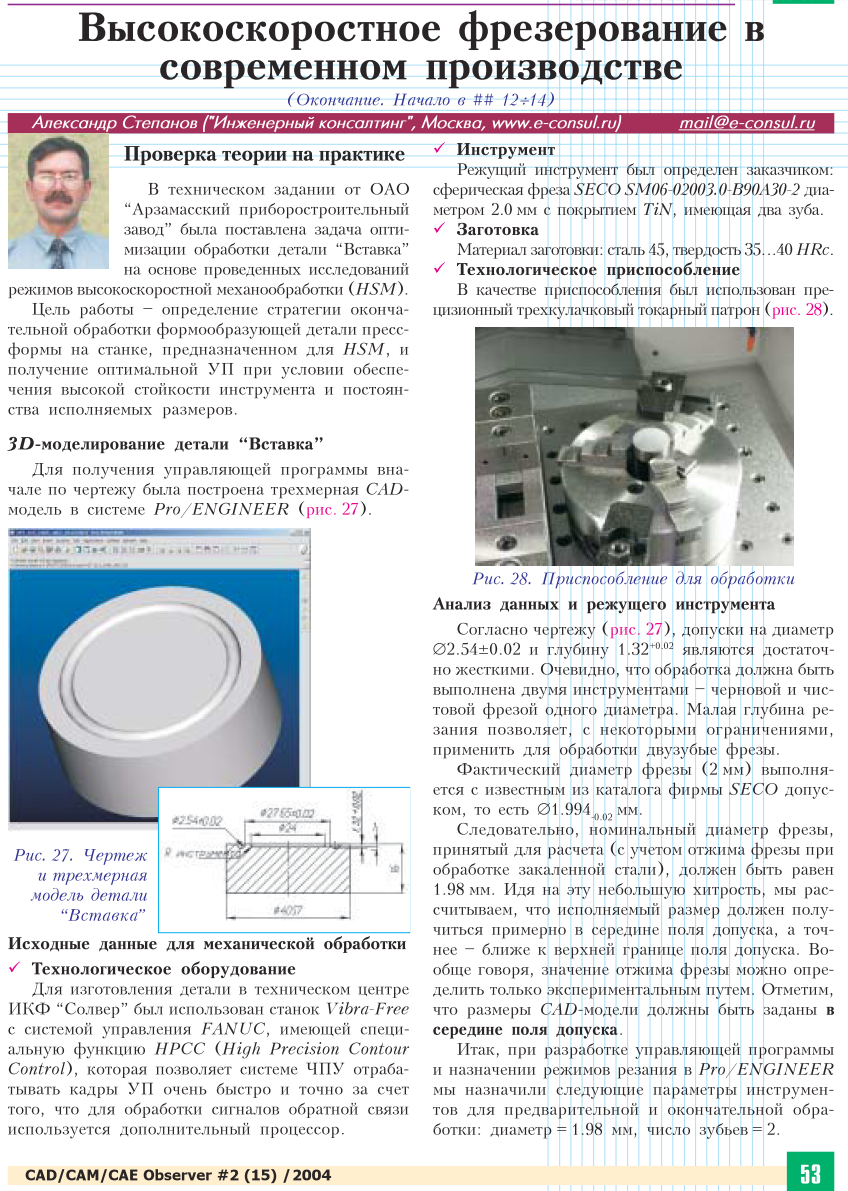
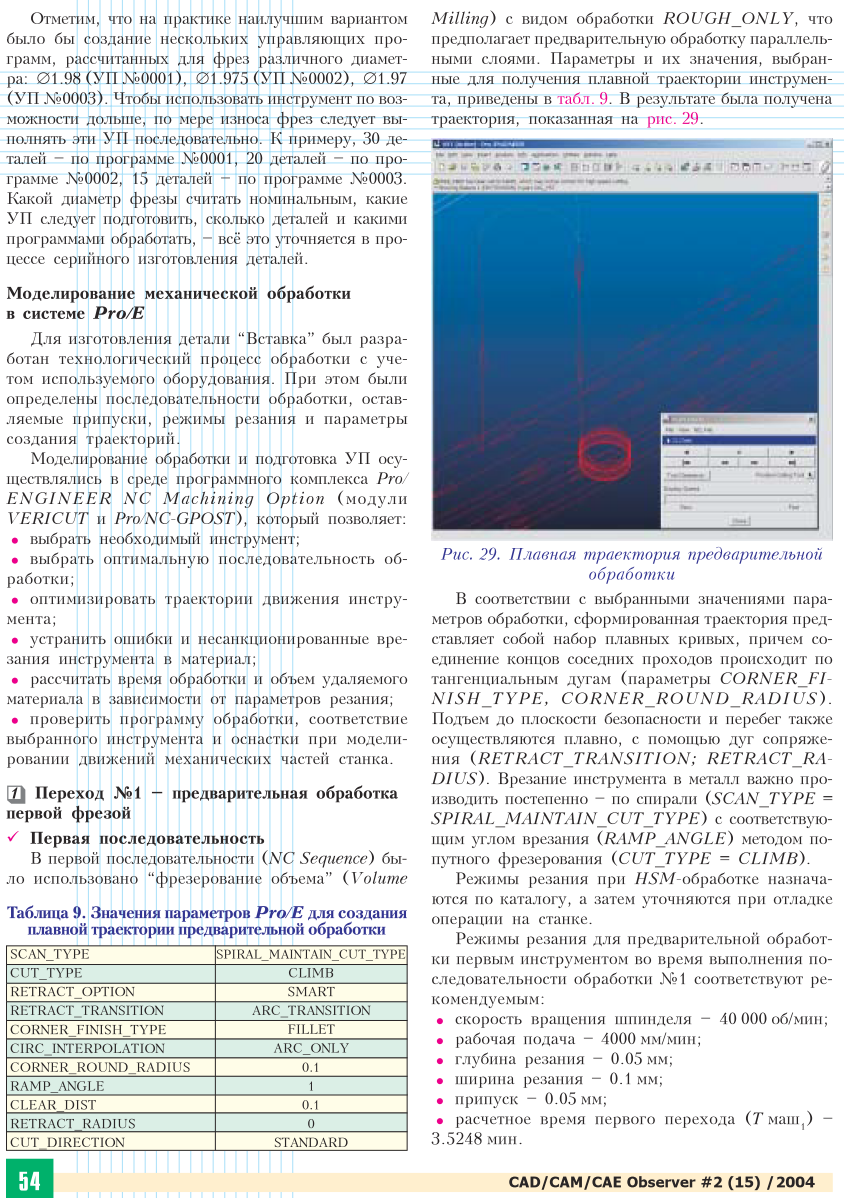

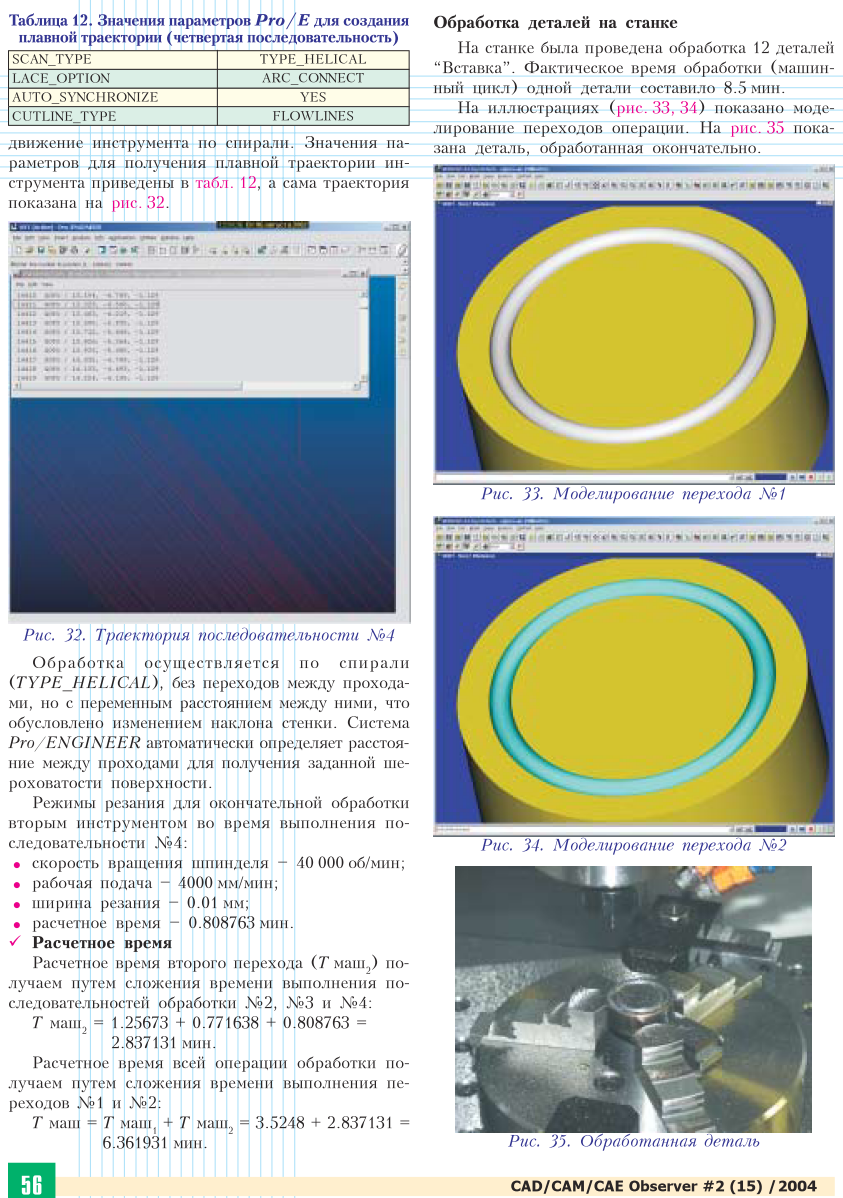
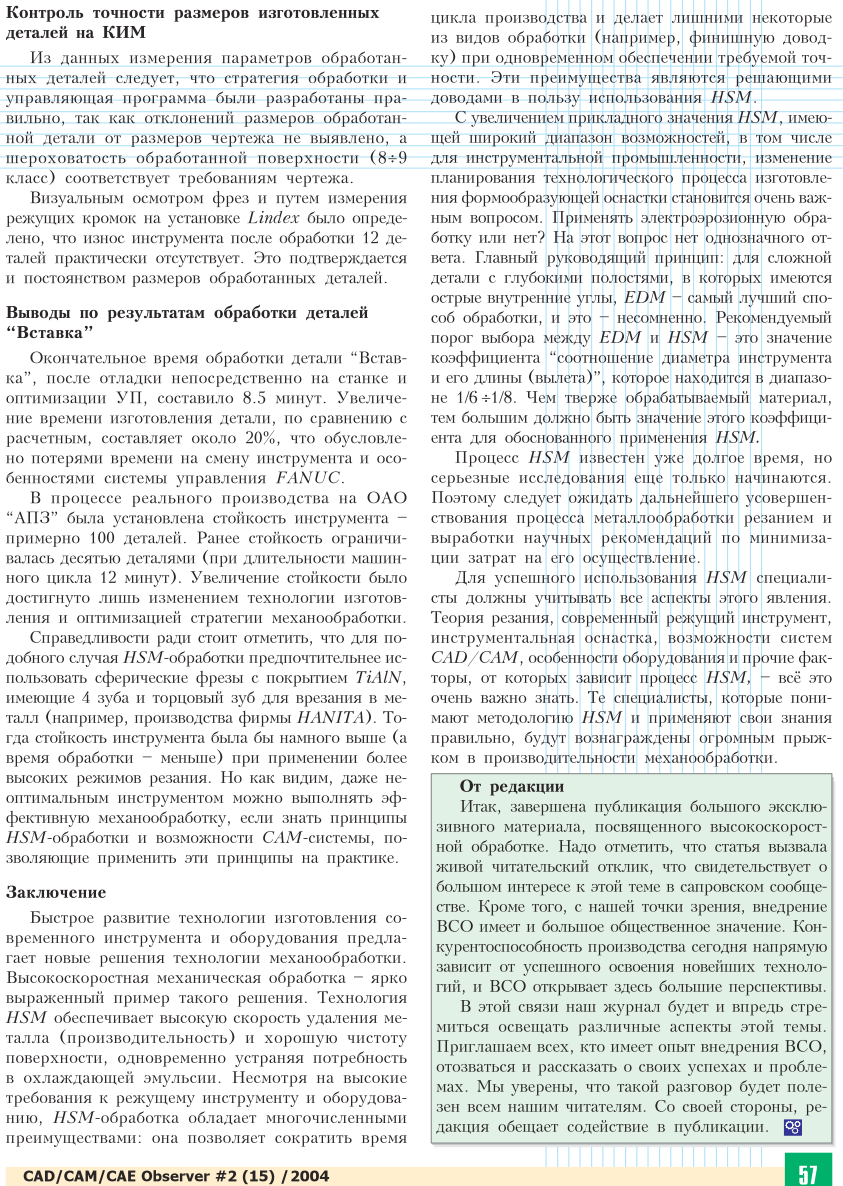
Демонстрационные видео:
New DTC Line for Trochoidal milling
Обработка видео...
HURCO high speed cutting at 20.000 mm/min at TECHNISHOW 2014
Обработка видео...
CNC Fräsen - 5-Achs HSC (High Speed Cutting) CNC Milling
Обработка видео...
Высокоскоростная обработка стального циклоидального колеса на трехкоординатном фрезерном станке
Обработка видео...
Высокоскоростное фрезерование никель хромового сплава
Обработка видео...
SGS Tool Company Series 43 (S-Carb)
Обработка видео...
TENDO E compact - The Universal Hydraulic Expansion Toolholder
Обработка видео...
Mitsubishi Materials VF-MHV Variable Flute SCEM
Обработка видео...
Walter Prototyp Proto max Ultra
Обработка видео...
Fraisa NX-NVDS milling 50 HRC H13
Обработка видео...
Mastercam machines 304 SS with Widia and Dynamic motion Technology
Обработка видео...
Источники:
Потапов В.А. Проблемы вибрации при высокоскоростном фрезеровании алюминия в авиакосмической промышленности и способы их решения // По материалам журнала «MODERN MACHINE SHOP», январь 2001.
Виттингтон К., Власов В. Высокоскоростная механообработка // «САПР и графика» №11, 2002.
Степанов А. Высокоскоростное фрезерование в современном производстве // CAD/CAM/CAE obcerver № 3, 2002.
О некоторых особенностях фрезерования в режиме высокоскоростной обработки (ВСО) д.т.н. проф. Оленин Л.Д., Очкин Д.И. Университет машиностроения
Использование материалов сайта возможно только с письменного разрешения администрации сайта и активной гиперссылкой на источник.
Свяжитесь с нами
Оставьте свое сообщение и мы свяжемся с вами, чтобы предложить лучшие условия сотрудничества!
Звоните: (812) 407-37-03
Пишите: order@carbidetool.ru
ООО «ТУЛЭКС» ИНН 7838092179, г. Санкт-Петербург, улица Аэродромная, д. 8, литер А, офис 418