- 8 (812) 407-37-03
- 197348, г. Санкт-Петербург, улица Аэродромная, д. 8, литер А, офис 418
- order@carbidetool.ru
Обрабатываемость сталей (теоретические основы и практические рекомендации).
(статья находится в разработке, материал будет редактироваться и дополняться)
В этой статье изложен материал об обрабатываемости различных марок сталей, даны рекомендации по обработке из различных справочников и литературы, а также даны рекомендации из практических наработок.
Под способностью материала подвергаться резанию понимают достижение при его обработке каких-либо из следующих технологических показателей: скорости резания vT при заданном периоде стойкости инструмента Т (например, v60, т.е. скорость резания при стойкости Т = 60 мин); качества обработанной поверхности; силы или мощности резания; определённой формы стружки. Обрабатываемость материалов резанием влияет, прежде всего, на период стойкости режущего инструмента и, следовательно, ограничивает предельную скорость резания (производительность обработки). Качественно обрабатываемость характеризуют по типу стружки, образующейся при резании исследуемого материала в эталонных условиях.
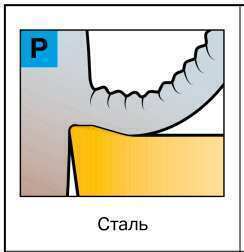
Сталь группа ISO P
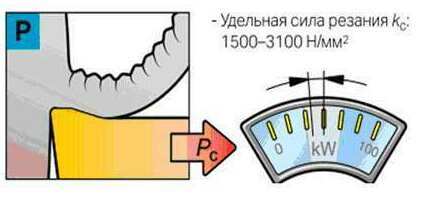
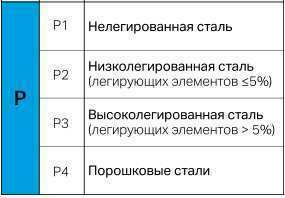
Сталь самый распространенный материал в металлообработке. Материал сравнительно хорошо обрабатывается, за исключением некоторых марок.
По химическому составу и содержанию легирующих элементов стали можно условно разделить на следующие подгруппы:
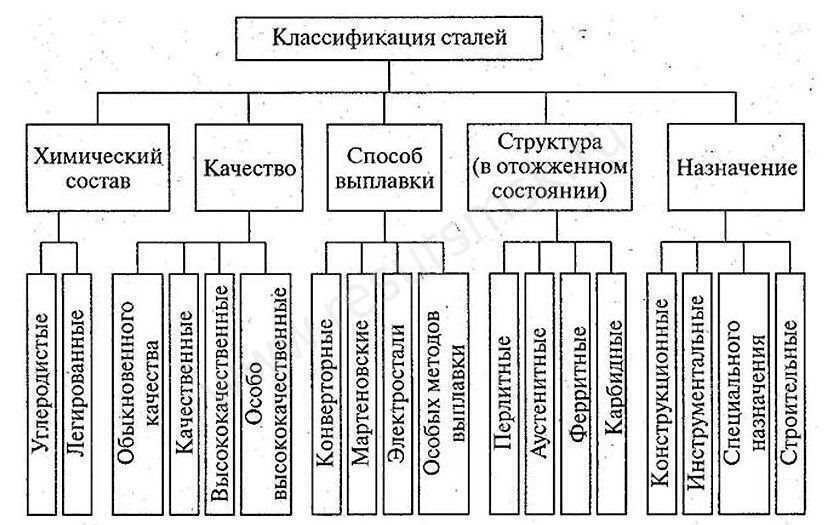
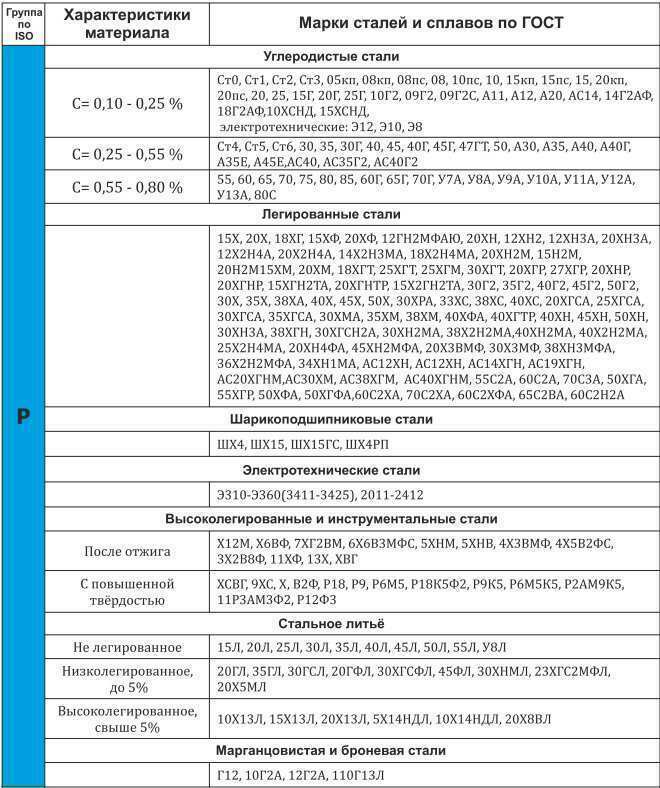
Нелегированные стали делятся на предназначенные и не предназначенные для термообработки. Низколегированные стали имеют свойства, во многом схожие со свойствами нелегированных сталей. Технически важным отличием является их улучшенная
закаливаемость, а также повышенная жаропрочность и устойчивость против отпуска. Высоколегированные стали имеют особые свойства. Стойкость к образованию окалины или специальные физические свойства реализуются только у высоколегированных сталей.
Большое влияние на обрабатываемость сталей оказывает их химический состав.
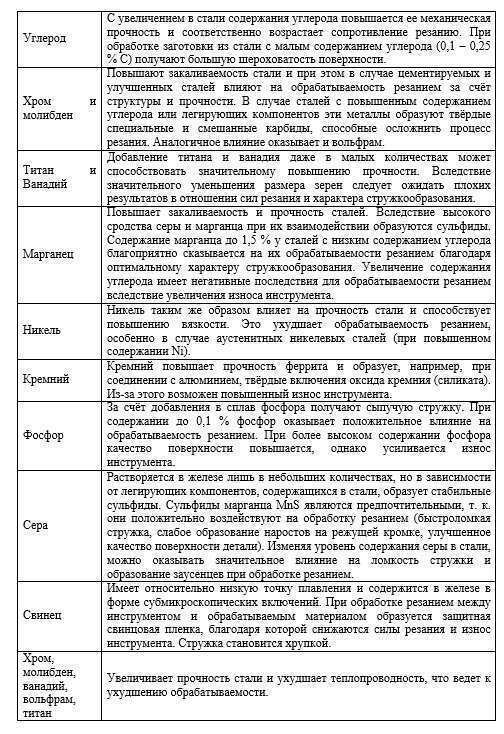
Наилучшую обрабатываемость имеют низкоуглеродистые (С < 0,2-0,25%) - автоматные стали, применяемые для изготовления деталей на станках-автоматах. Для улучшения обрабатываемости в них вводят небольшие добавки серы (0,2...0,3 %), фосфора (до 0,15 %) и свинца (0,15...0,3 %), которые снижают коэффициент трения и интенсивность износа инструмента (благодаря сере), а также улучшают дробление стружки (благодаря свинцу, фосфору). За счет этого коэффициент обрабатываемости таких сталей увеличился до Коб=1,5...2,1, производительность обработки возросла в 2 раза, уменьшились силы резания и шероховатость обработанной поверхности. Однако при этом механические свойства автоматных сталей несколько снизились.
Так, стали автоматные (А12, А20 и др.) с повышенным содержанием серы до 0 15 %) обрабатываются лучше, чем малоуглеродистые стали.
Для обтачивания на автоматах лучше подходят более мягкие сфероидизованные структуры, а для нарезания зубьев и протягивания - несколько более твердые структуры пластинчатого перлита с разорванной сеткой феррита или сорбита; они дают более чистую поверхность, но на автоматах обрабатываются труднее.
Конверторные низкоуглеродистые стали обрабатываются лучше, чем выплавленные в мартеновских и электрических печах, так как содержат в больших количествах серу и фосфор. Холоднокатаные стали, содержащие углерод до 0,3 %, обрабатываются лучше, чем горячекатаные, а при содержании углерода С > 0,4% - хуже. Кипящая сталь обладает более высокой обрабатываемостью, чем спокойная.
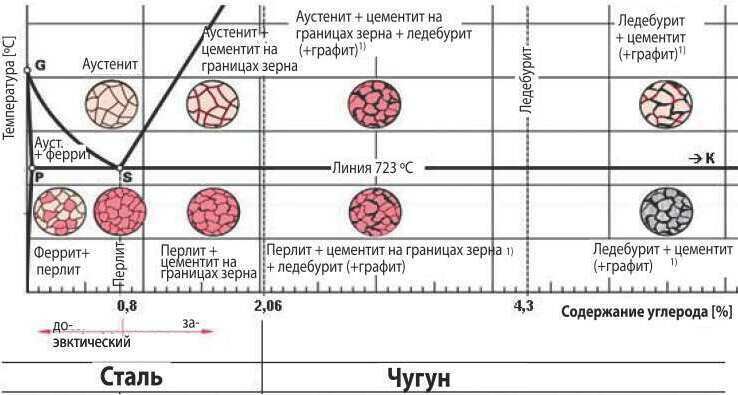
Наилучшей обрабатываемостью обладают стали со структурой перлит (феррит + цементит). Чтобы максимально улучшить обрабатываемость высокоуглеродистых сталей (С > 0,6 %), они должны иметь структуру зернистого перлита, обладающего меньшей истирающей способностью, даже если это ухудшает качество поверхности.
При обработке резанием феррит создает значительные трудности: • высокая склонность к налипанию материала на инструмент, образование наростов на режущей кромке; образование нежелательной ленточной и запутанной стружки (высокая пластичность); низкая чистота обработки поверхности и образование заусенцев на деталях.
Перлит, в свою очередь, осложняет процесс резания следующими факторами: сильный абразивный износ; повышенные силы резания.
Обрабатываемость резанием сталей с содержанием C < 0,25 % в значительной мере обусловлена вышеназванными свойствами феррита. При низких скоростях резания на режущей кромке образуются наросты. С повышением скорости резания износ инструмента постепенно увеличивается, при этом возрастает и температура резания. Учитывая эти факторы, следует выбирать инструмент по возможности с положительным передним углом. Поверхности низкого качества и с множеством заусенцев образуются прежде всего при низких скоростях резания, обусловленных технологией обработки.
Для углеродистых сталей с содержанием C от 0,25 до 0,4 % свойства перлита влияют на обрабатываемость резанием следующим образом: снижаются склонность к налипанию и образование наростов на режущей кромке; вследствие повышенной нагрузки на зону контакта возрастает температура резания и увеличивается износ инструмента; структура материала положительно влияет на чистоту обработки поверхности, на количество и форму стружки.
При дальнейшем повышении содержания углерода (0,4 % < C < 0,8 %) доля перлита увеличивается, а при 0,8 % C перлит остается единственной структурной составляющей. В целом стали считаются материалом, хорошо поддающимся резанию, только с точки зрения образования стружки и чистоты обработки поверхности. Вследствие повышенной твёрдости и прочности надлежит считаться с интенсивным износом. Для уменьшения износа следует работать с пониженной скоростью или с использованием СОЖ.
В заэвтектических углеродистых сталях (C > 0,8 %) при медленном охлаждении на воздухе также образуются феррит и цементит. В отличие от доэвтектических углеродистых сталей ферритовая решетка не образуется, феррит присутствует только в качестве раствора в перлите. Образование перлита начинается непосредственно от границ зерна аустенита. При содержании углерода значительно выше 0,8 % на границах зерна происходит осаждение цементита, т.е. даже свободный цементит образует оболочку вокруг зерен аустенита или перлита. Подобные стали при обработке резанием вызывают очень сильный износ. Наряду с интенсивным абразивным воздействием твёрдых и хрупких структурных составляющих, возникающие высокие давления и температуры даже при
сравнительно низких скоростях резания вызывают сильный износ по передней и задней поверхностям. В связи с этим надлежит работать с низкими скоростями резания и большими поперечными сечениями стружки, а также с прочными режущими кромками.
В инструментальных, легированных и быстрорежущих сталях увеличение легирующих элементов всегда приводит к ухудшению обрабатываемости (до Коб = 0,6) и росту шероховатости обработанной поверхности вследствие образования твердых карбидов. При этом, как правило, повышаются предел прочности σв при растяжении и твердость сталей, возрастает сопротивление сталей обработке резанием. Наихудшую обрабатываемость имеют структуры: сорбитообразный перлит, сорбит и тростит после закалки и отпуска. Наилучшей по обрабатываемости структурой инструментальных сталей является зернистый перлит с равномерно распределенными мелкими карбидами после тщательной проковки и сфероидизирующего отжига. В целом же в зависимости от химического состава у высоколегированных сталей коэффициент обрабатываемости снижается от Коб = 0,65 (хромистые, коррозионностойкие стали) до Коб = 0,3 (хромоникелевые жаростойкие стали).
Говоря про особенности обработки различных типов сталей …
Низкоуглеродистая сталь… такая как Ст. 3, Сталь 20… (содержание углерода <0,25%) требует особого внимания из-за сложностей со стружкодроблением и тенденции к налипанию (наростообразование на режущей кромке). Для дробления и отвода стружки необходимо обеспечить как можно большую подачу. Необходимо использовать высокую скорость резания для предотвращения наростообразования на режущей кромке пластины, которое может отрицательно сказываться на качестве обработанной поверхности. Применение пластин с острыми кромками и геометриями для ненагруженного резания уменьшают тенденции к налипанию материалов и предотвращают разрушение кромки.
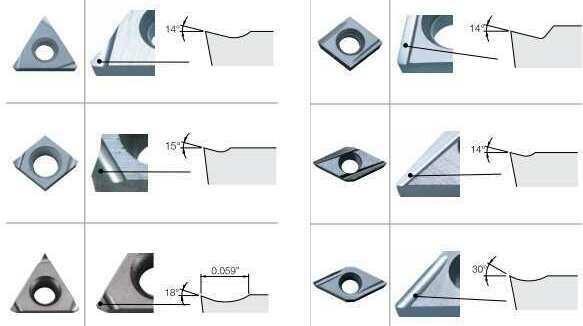
При чистовой обработке таких сталей рекомендуется применение острых полированных геометрий пластин из кермета, при этом скорость резания должна быть в пределах от 150 до 450 м/мин (в зависимости от условий обработки и производителя пластин значение скорости резания может доходить до 500-700 м/мин). Кермет обеспечивает не только превосходную остроту режущей кромки, но способствует минимальному взаимодействию материала инструмента и обрабатываемого материала, что в свою очередь способствует получению высокого качества обрабатываемых поверхностей. Кермет как правило плохо работает на скоростях ниже 100 м/мин, качество обработки и стойкость пластин заметно снижаются.
Применение высококачественных СОЖ для чистовой обработки так же способствует улучшению обрабатываемости низкоуглеродистых сталей.
При фрезеровании низкоуглеродистых сталей основной проблемой так же является образование наростов и заусенцев. Одним из вариантов решения проблемы является применение скоростной обработки, применение инструментов с острой геометрией, применение качественных СОЖ.
Обрабатываемость низколегированной стали зависит от содержания легирующих элементов и термообработки (твёрдости). Для всех материалов в этой группе наиболее распространёнными механизмами износа являются лункообразование и износ по задней поверхности. Поскольку упрочнённые материалы выделяют в зоне резания больше тепла, распространённым механизмом износа также является пластическая деформация. Для низколегированной стали в неупрочнённом состоянии первым выбором будет серия сплавов и геометрий для стали. Для точения упрочнённых материалов предпочтительно использовать более твёрдые сплавы, пластины с многослойными износостойкими покрытиями (в определенных случаях керамику и CBN).
Высоколегированные стали с общим содержанием легирующих элементов более 5%. В эту группу входят и мягкие, и упрочнённые материалы. Обрабатываемость снижается с ростом содержания легирующих элементов и твёрдости. Что касается низколегированных сталей, то первым выбором будут сплавы и геометрии для стали. Сталь с содержанием легирующих элементов более 5% и твёрдостью более 450 HB предъявляет дополнительные требования в плане стойкости к пластической деформации и прочности кромки. Часто для сталей, в состав легирующих элементов которой входят хром, титан, марганец - рекомендуется применение прочных сплавов пластин с многослойными износостойкими покрытиями подобными для обработки чугунов, поскольку преобладающим становится износ по задней поверхности, выкрашивания.
При фрезеровании сталей высокой твёрдости важное значение приобретает взаимное расположение заготовки и фрезы для предотвращения выкрашивания режущей кромки (во избежание излишнего увеличения толщины стружки на выходе, а также по возможности проводить черновую обработку без применения СОЖ).
Нужно заметить, что в каталогах различных производителей инструмента мартенситные нержавеющие стали (типа 20Х13, 40Х13, 65Х13, 14Х17Н2, 95Х18 и др.) часто вносят в таблицы раздела группы Р. При обработке подобных материалов назначаются инструменты (марки сплавов) соответствующие для обработки сталей из раздела ISO группы Р. Мартенситная структура твердая, и вызывает в основном износ по задней поверхности. Применение твердых сплавов с многослойными износостойкими покрытиями, которые в сочетании обеспечивают и хорошую термостойкость, и высокую износостойкость позволяют вести обработку таких сталей без особых сложностей. Коэффициент обрабатываемости таких сталей в отожженном состоянии, или в закаленном и отпущенном состоянии при твердости 270-340HB для твердого сплава составляет Кʋтв.спл.=0,6-0,8.
Обрабатываемость многих сталей улучшается в результате отжига и отпуска, которые приводят к снижению действительного предела прочности при максимальном выделении из твердого раствора и максимальной коагуляции карбидов. Плохо обрабатываются стали и как с очень низкой твердостью, так и с высокой.
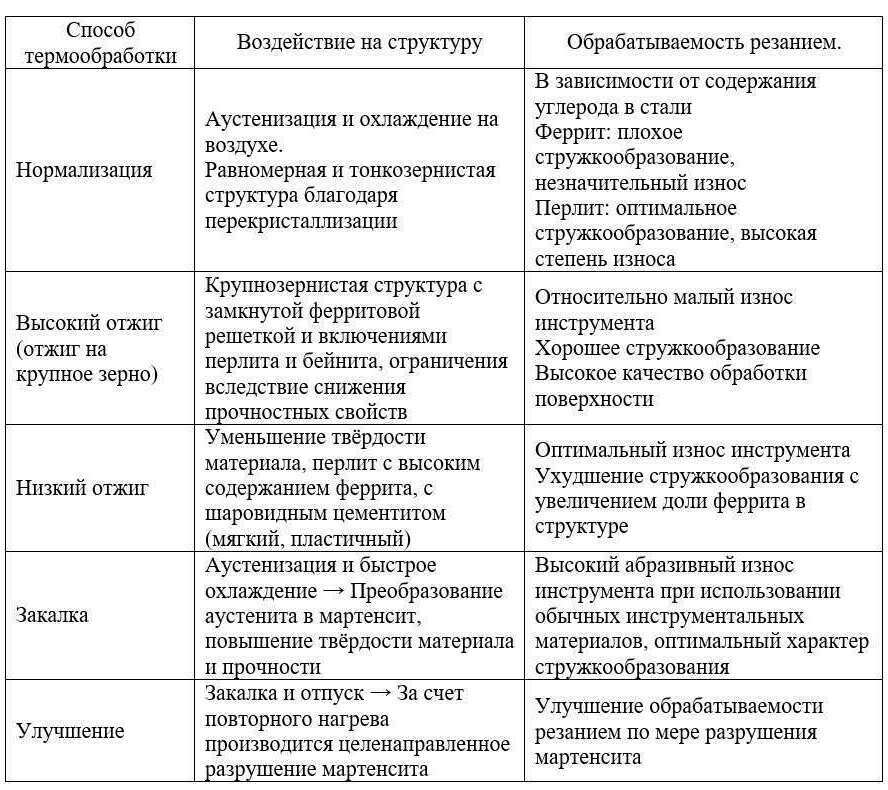
При закалке стали в случае увеличения действительного предела прочности ее обрабатываемость ухудшается, несмотря на то что, например, у аустенитной стали после такой термической обработки во многих случаях твердость снижается. Для многих марок сталей, жаропрочных материалов обрабатываемость улучшают правильно подобранными режимами термообработки.
Иногда термообработка является единственным из вариантов ведения обработки стали резанием инструментом из быстрореза или из твердого сплава (к примеру с применение плазмотронов).
Ярким примером такой стали можно указать аустенитную сталь Гадфильда (110Г13Л), сталь обладает высокой пластичностью и степенью износа, сильно упрочняется в процессе резания, твердость упрочненного слоя становится соизмеримой с твердостью инструмента.
И только применение термообработки снимает наклеп. Из стали 110Г13Л изготавливаются такие детали как гусеничные траки для тракторов, коронки землеройных машин, била, щеки (тиски) дробилок, рельсовые крестовины и стрелочные переводы, шарики и пластины мельниц, различные решетки, штыри и втулки и т.д.
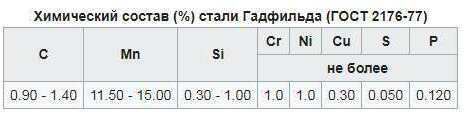
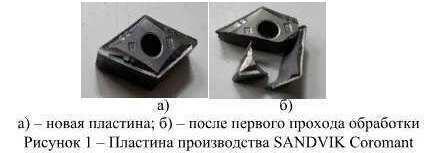
В современном производстве в основном применяются пластины CBN для обработки стали 110Г13Л. Только кубический нитрид обеспечивает и высокую производительность и хорошую стойкость инструмента.
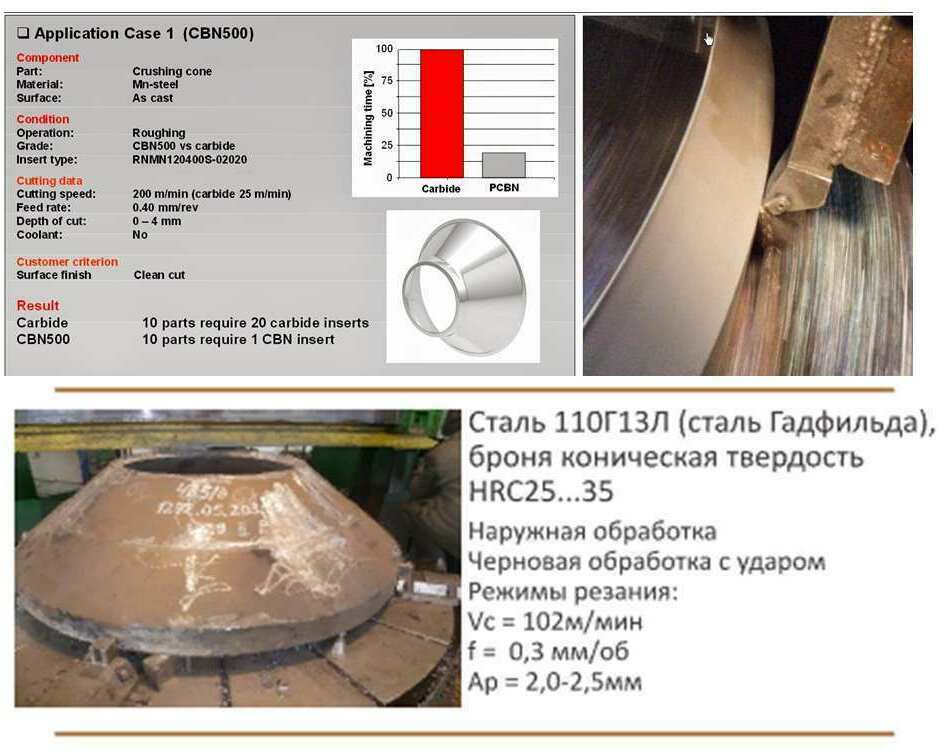
Обработка пластинами из тв.сплава тоже возможна, но на более низких режимах резания, при применении пластин с соответствующими износостойкими покрытиями. Самый оптимальный вариант применения пластин с позитивной геометрией, с покрытием MT CVD типа TiCN + Al2O3 или TiCN + Al2O3+TiN, с увеличенным по толщине слоем Al2O3. При стабильных условиях резания и чистовой обработке возможно применение мелкозернистых износостойких сплавов…был опыт использования пластин ISCAR сплав IС907 на скорости в пределах 20-30 м/мин с глубиной резания 1-1,5 мм, и подачей 0,1-0,15 мм/об…стойкость была в пределах 20-30 минут.
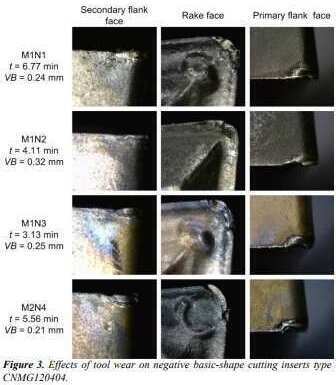
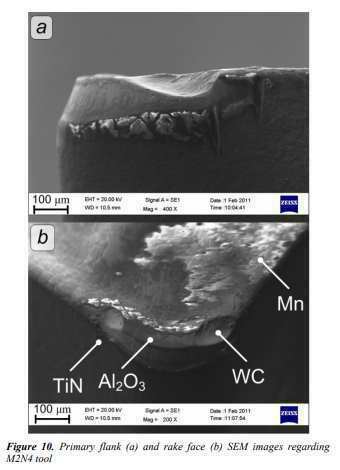
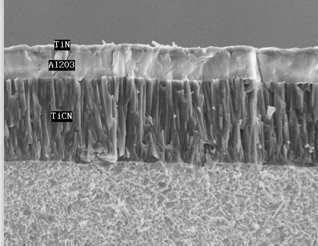
Нажмите на картинку для увеличения
При ведении фрезерной обработки стали 110Г13Л предпочтительна стратегия схожая с обработкой закаленных материалов, как вариант применение стратегий ВСО, и применение инструментов с износостойкими покрытиями для обработки материалов высокой твердости.
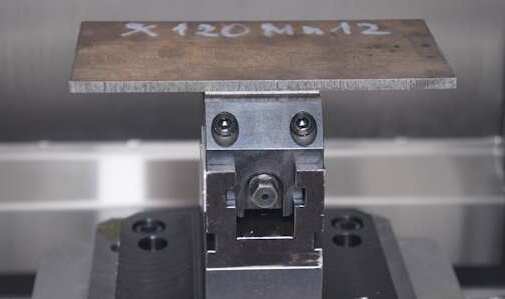
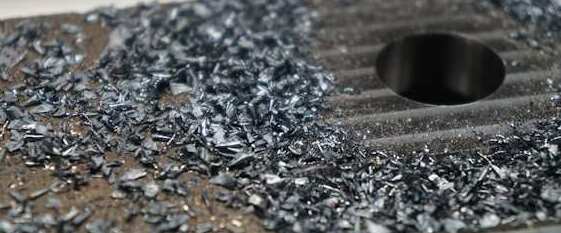
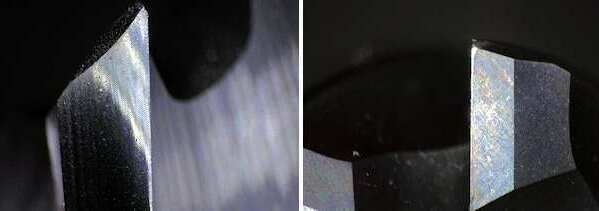
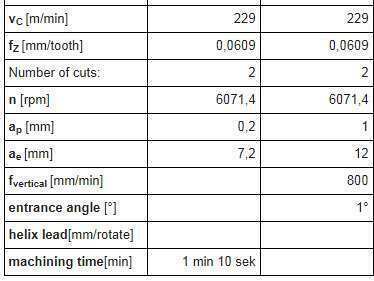
В качестве примера - применение торцевых насадных фрез со сменными пластинами производителя СКИФ-М.
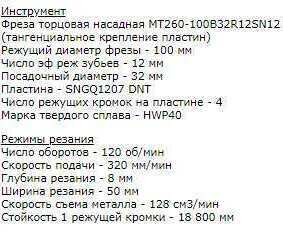
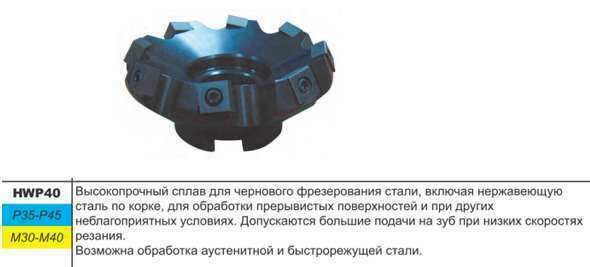
Есть старые методики обработки на универсальных станках с применением инструментов из быстрорежущих сталей повышенной красностойкости. За счет подбора режимов резания и соответствующей заточки инструмента такая обработка возможна.
Ниже приведены вырезки из научных работ, в которых ранее проводились исследования по обработке подобных сталей с применением плазматронов (ПМО), и различных типов пластин.
Физическая сущность процесса плазменно-механической обработки заключается в разупрочнении материала детали, обрабатываемой традиционными методами резания на токарных, карусельных или строгальных станках, с помощью локального дозированного нагрева в пятне плазменной дуги, при этом глубина нагрева регулируется таким образом, что разупрочненный слой удаляется резцом, следующим за пятном нагрева.
В числе таких материалов, при обработке которых используется ПМО можно назвать сталь 22КВД, наплавки ЖСН5, ЗХ2В8, проводились даже эксперименты применения ПМО при обработке титана.
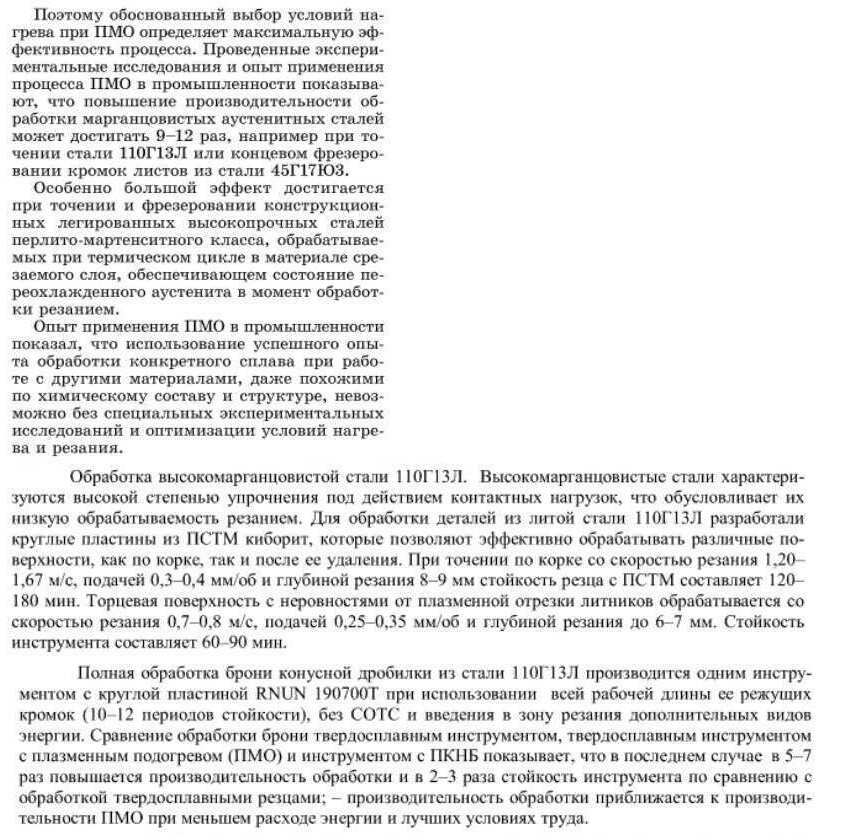
Стоит так же упомянуть о сталях типа Hardox. Довольно часто многие сталкиваются с проблемами при ее обработке.
Hardox – легированная горячекатаная сталь, которая относится к классу конструкционных сталей твердостью от 350 до 650 HB. Изготавливается мелкозернистая сталь Хардокс шведской компанией SSAB Oxelösund AB. В процессе производства сталь проходит закалку и отпуск. Производители сделали упор именно на устойчивость материала ко всем видам износа. Благодаря этому срок эксплуатации изделий и конструкций из Hardox в пять раза выше, чем у аналогичного металлопроката из других марок сталей. Кроме того, эта сталь характеризуется повышенной ударопрочностью и устойчивостью к вибрационным нагрузкам.
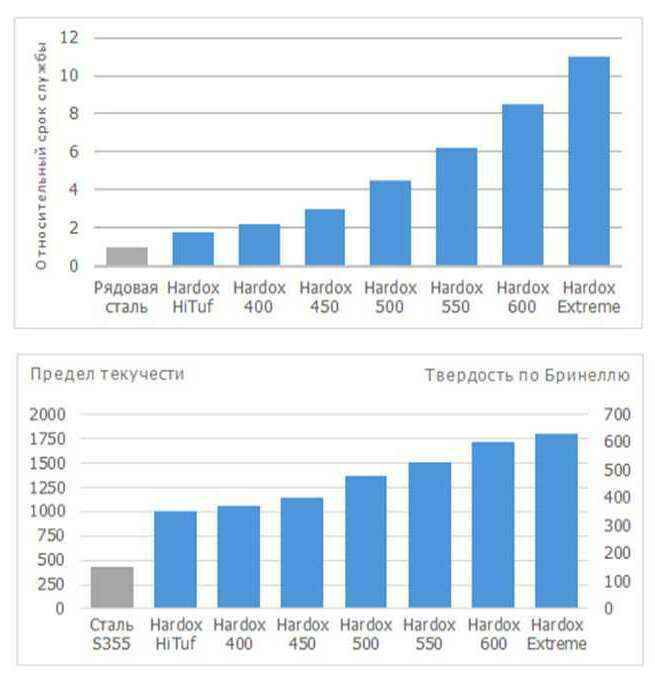
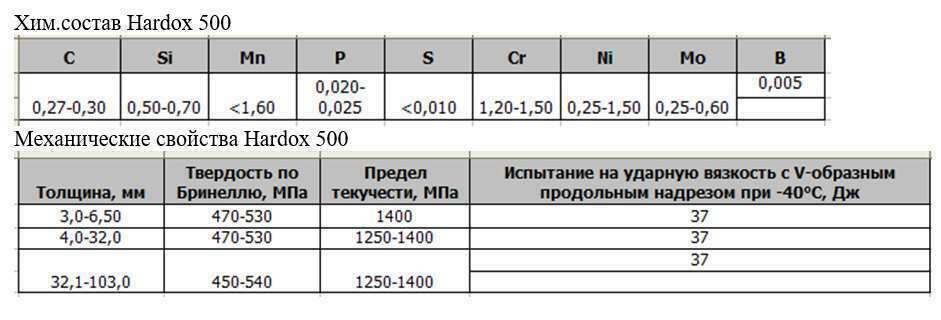
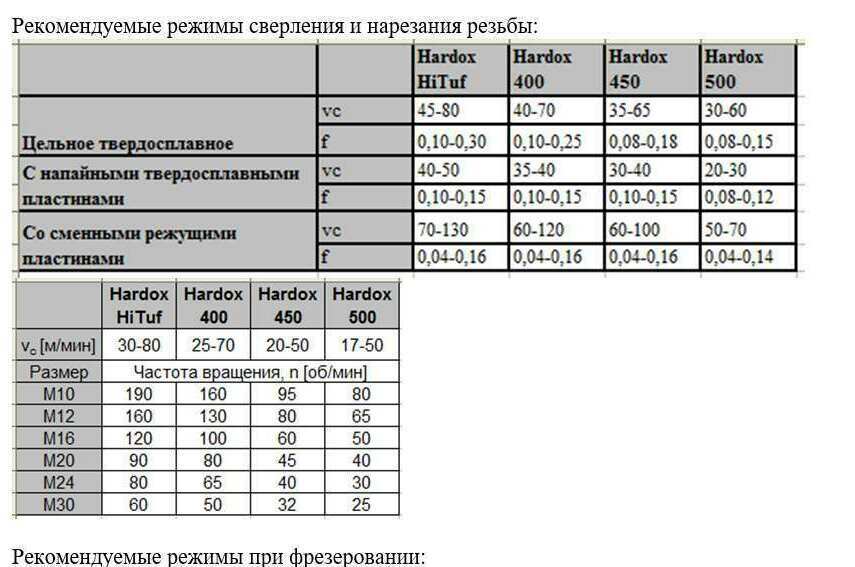
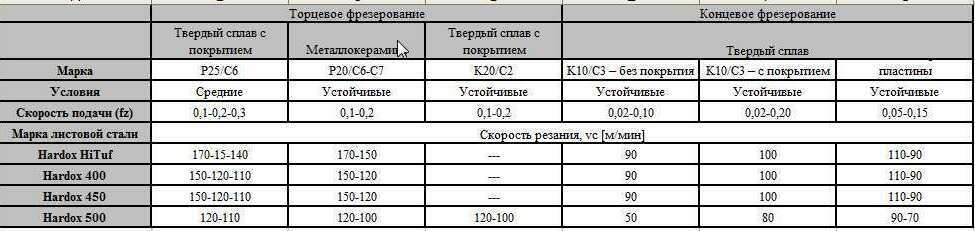
Рекомендации SSAB по обработке материалов Hardex
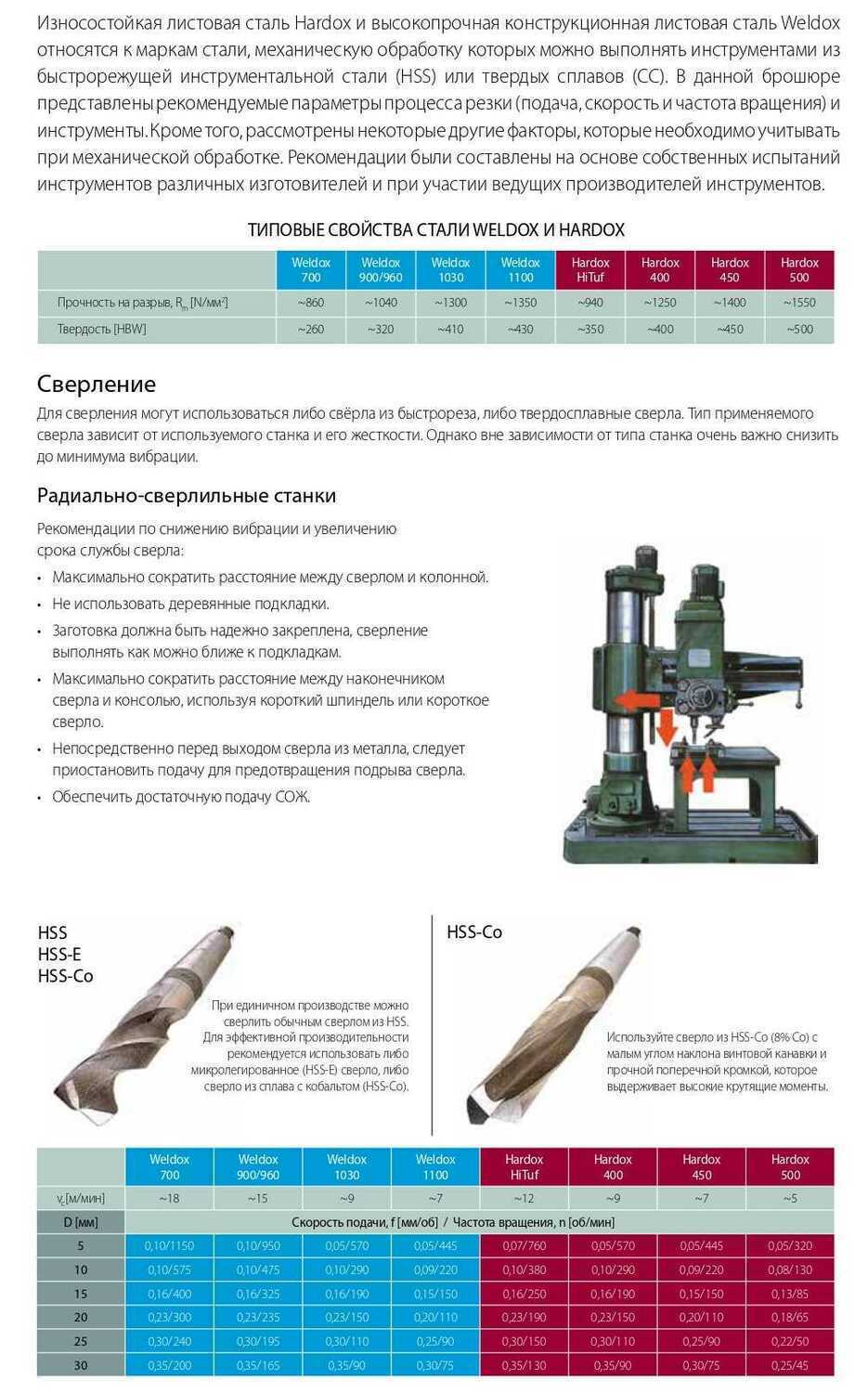

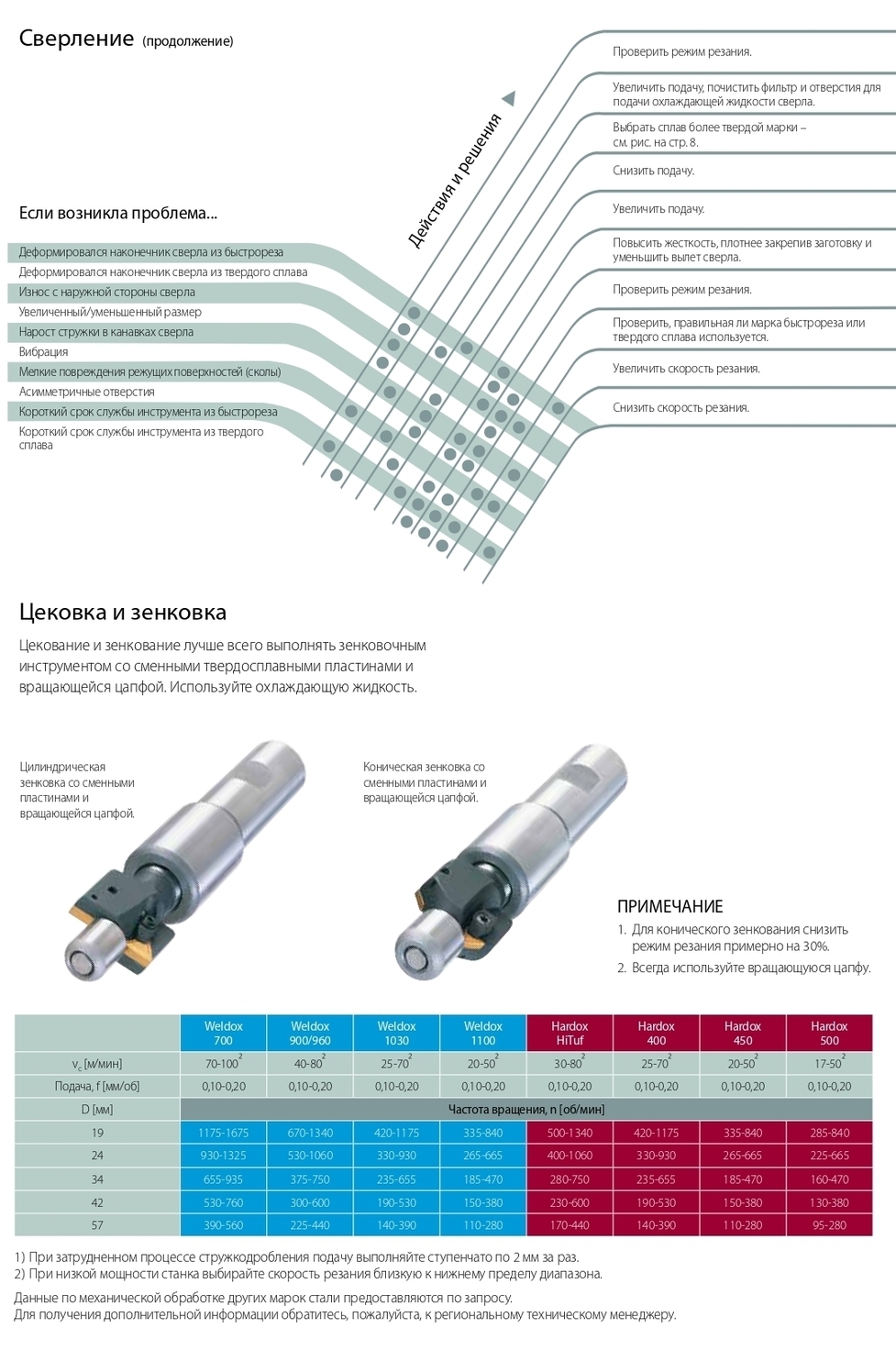
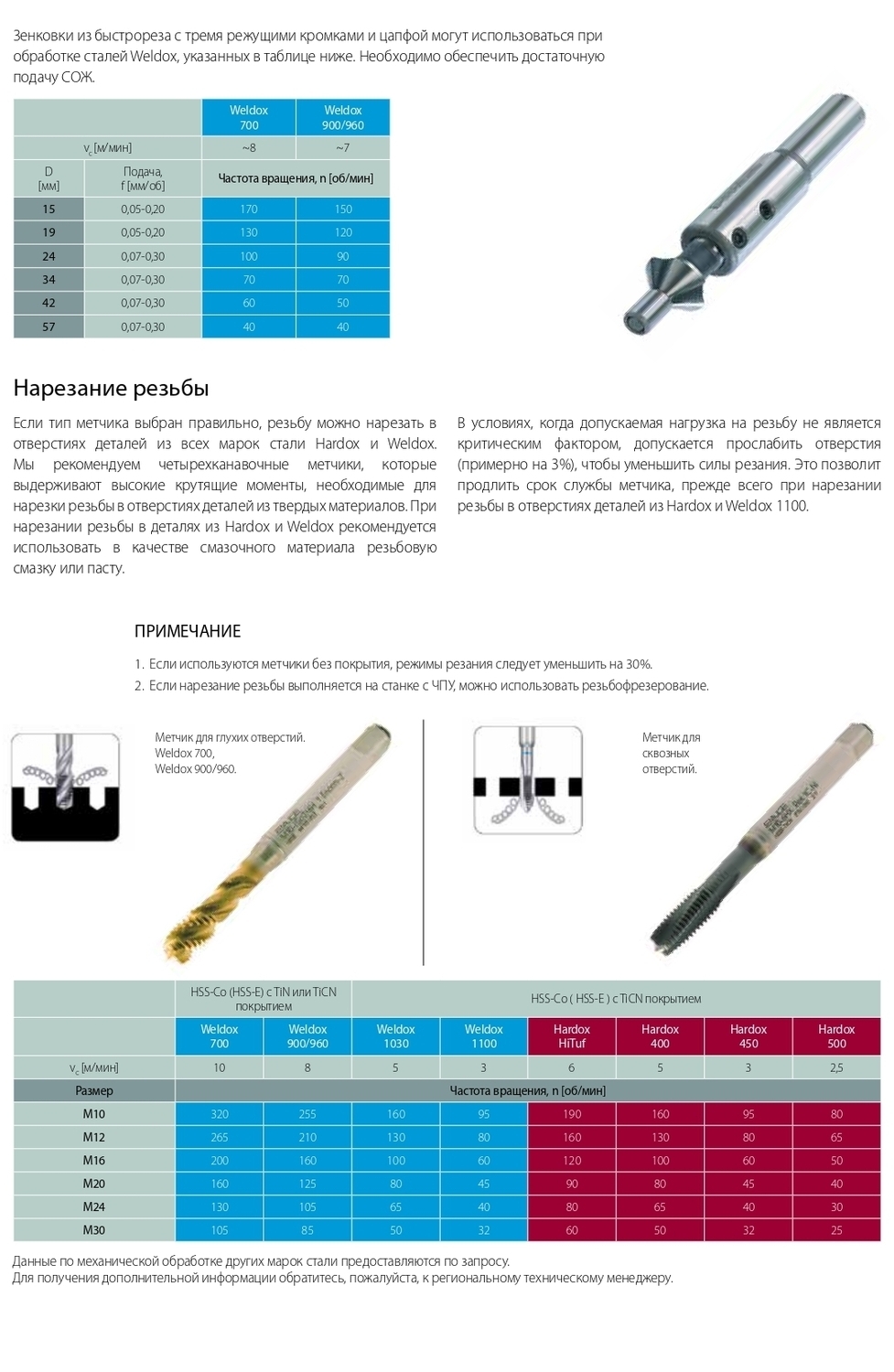
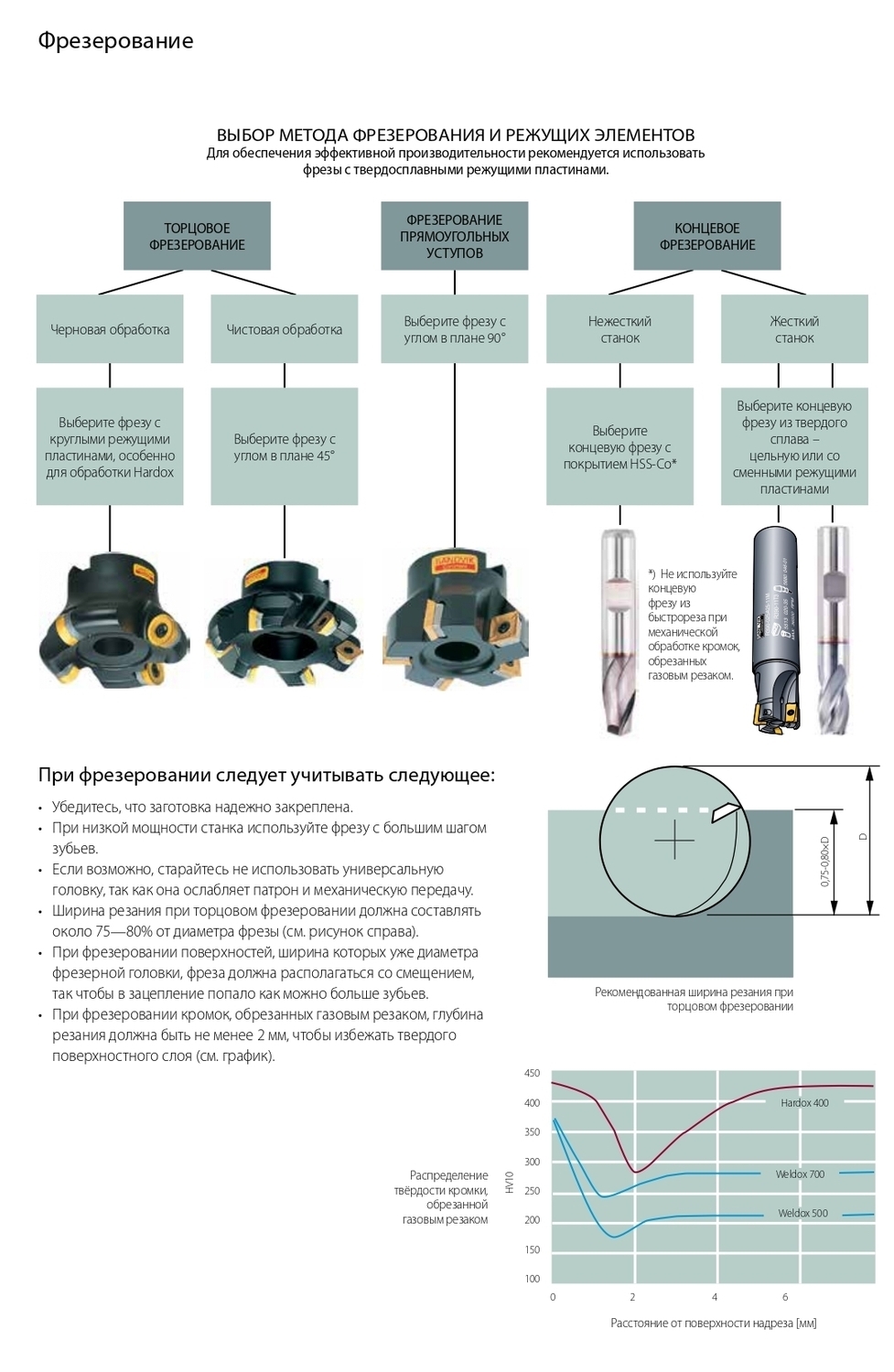
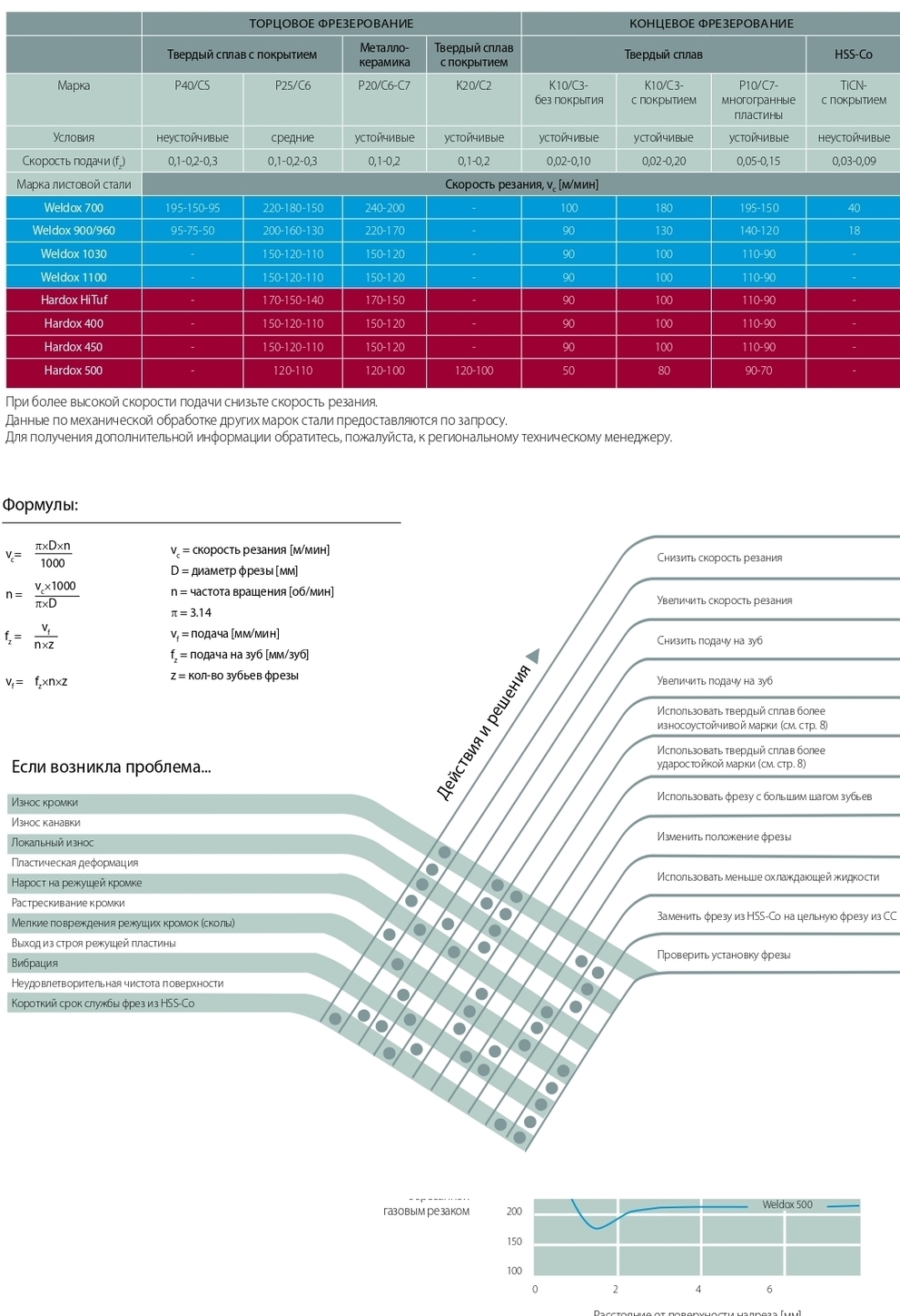
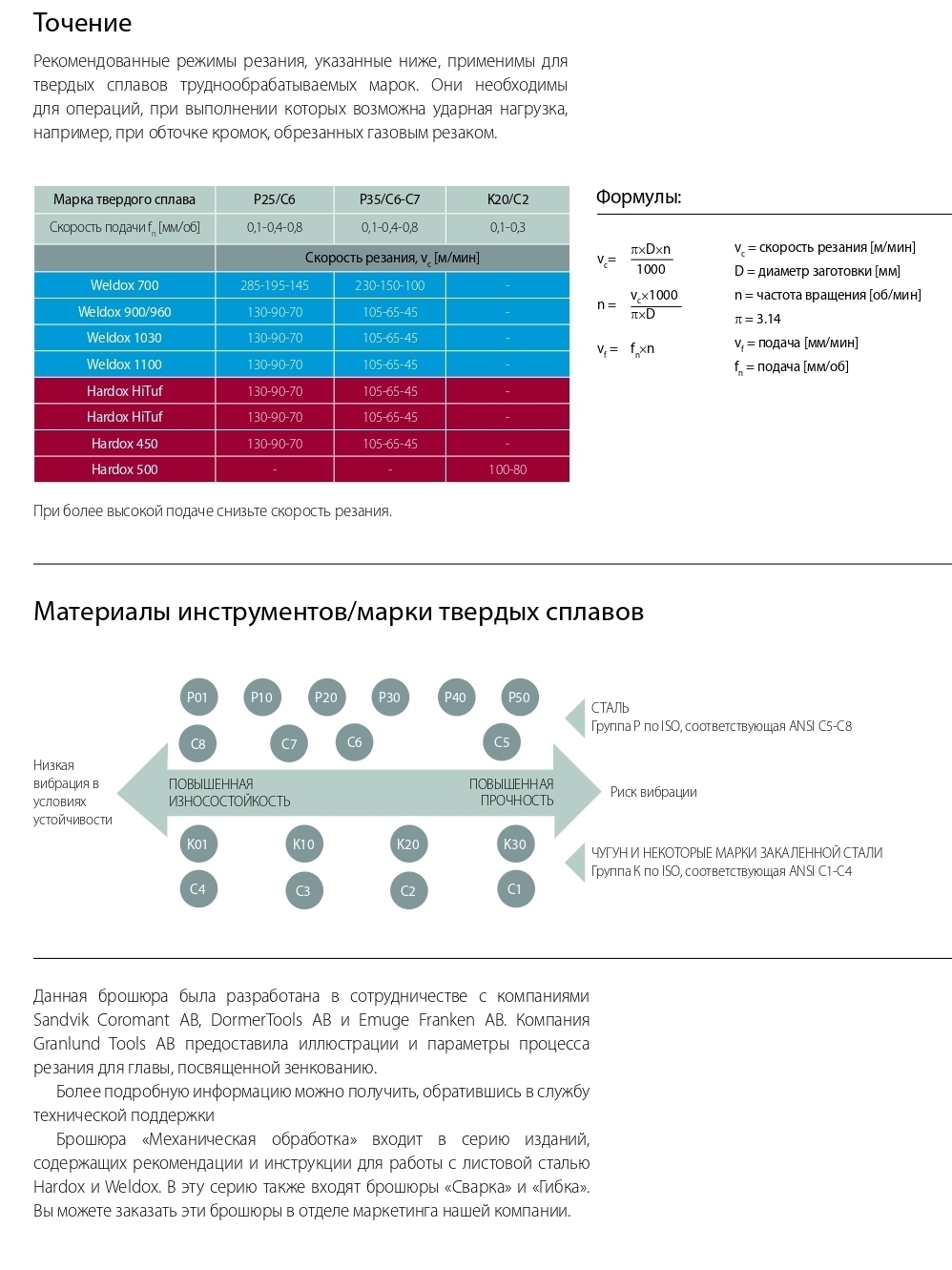
Нажмите на картинку для увеличения
Дополнительная информация к вопросу обрабатываемости сталей
При выборе режима резания обычно используется показатель, характеризующий интенсивность изнашивания рабочих поверхностей инструмента при обработке данного материала по сравнению с интенсивностью изнашивания эталонного материала в тех же условиях. Поэтому в нормативах и рекомендациях по режимам резания обрабатываемость материала чаще всего характеризуется с помощью поправочного коэффициента Км , который одновременно является поправочным коэффициентом к выбираемой скорости резания Км = Vx / Vэт. Коэффициент обрабатываемости Км , выступающий в нормативах в роли поправочного коэффициента, характеризует только марку и химический состав обрабатываемого материала, поскольку конкретные физико-механические свойства материала (твердость или прочность) обычно учитываются в нормативах дополнительным поправочным коэффициентом.
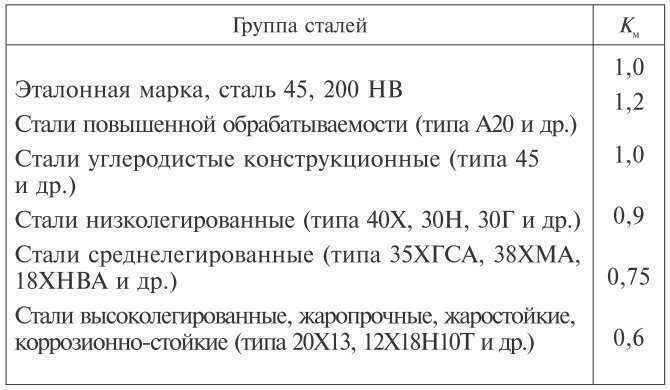
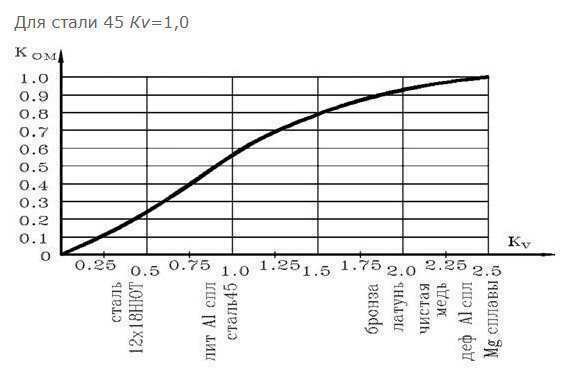
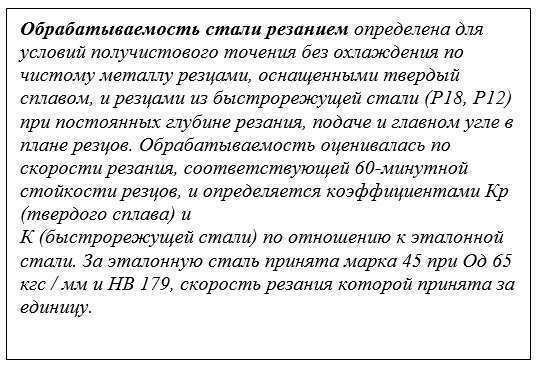
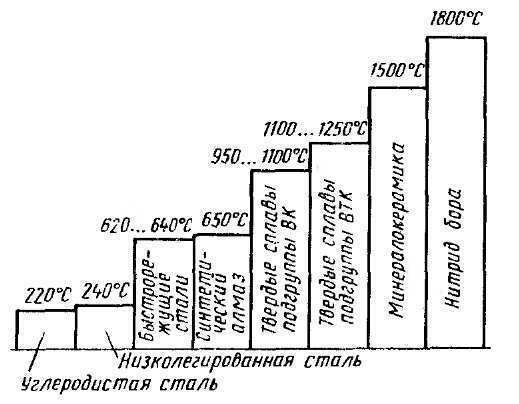
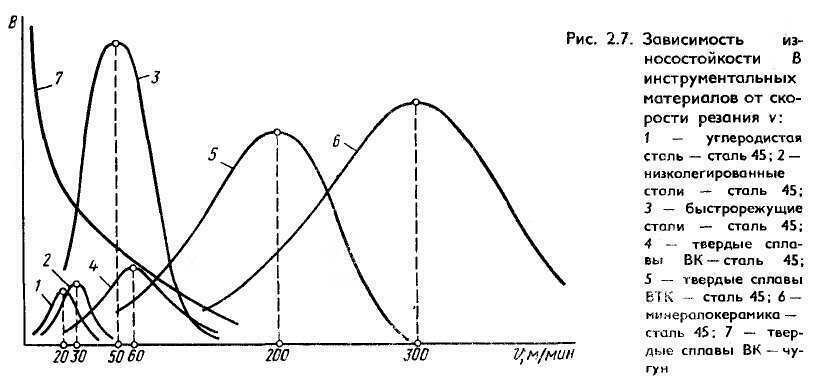
Ведение обработки при оптимальной производительности и стойкости инструмента одна из самых непростых задач. Весьма интересной является методика, предложенная доктором тех. наук, профессором Макаровым А.Д. - оптимизации по оптимальной температуре резания в зоне контакта, при которой для разных групп инструмент и обрабатываемая деталь, есть оптимальная температура в зоне резания, при которой скорость износа режущей части инструмента, так же является оптимальной. Причем значение скорости резания, глубины, подачи разные для различных их соотношений в зависимости от вида обработки, при этом каждому выбранному типу обработки соответствует своя оптимальная температура в зоне резания, при которых наблюдается наименьшая интенсивность износа инструмента, обусловленная различными факторами.
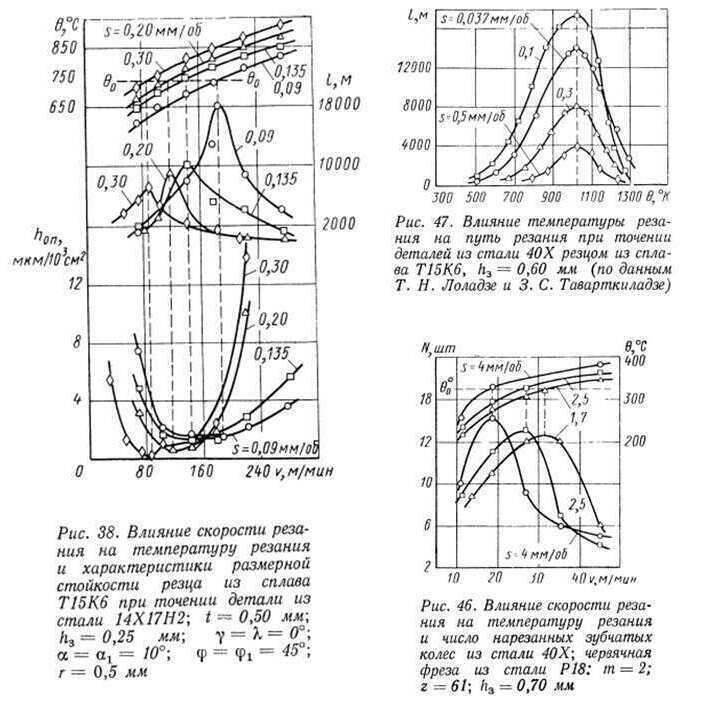
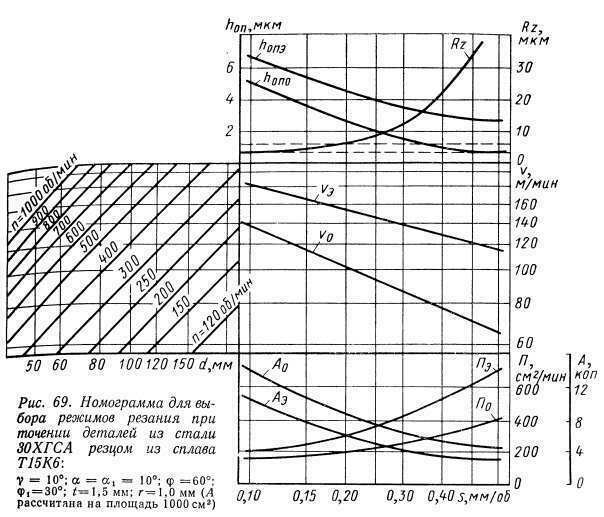
Макаров А.Д. "Оптимизация процессов резания", Москва, Машиностроение, 1976г.
Влияние на формирование стружки режимов резания и конструктивных особенностей режущей части инструмента.
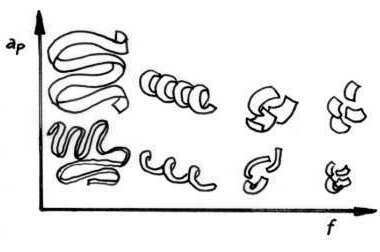
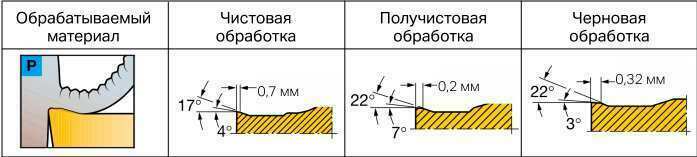
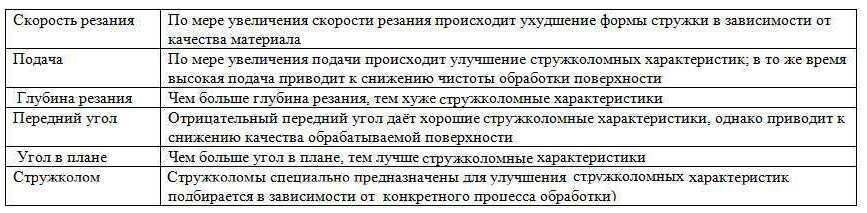
Физические основы образования нароста.
В процессе стружкообразования слои материала заготовки, образующие после отделения пограничный слой между передней поверхностью режущего инструмента и нижней стороной стружки, подвергаются значительной пластической деформации. В процессе обработки металлов резанием при неблагоприятных условиях возможна сварка давлением. Поэтому, в особенности при низких скоростях резания существует опасность интенсивного образования наростов на режущей кромке.
Нарост на режущей кромке появляется вследствие значительной деформации и затвердевания материала заготовки (наклёп), и выполняет функцию режущей кромки. В зависимости от режима резания, от нароста на режущей кромке по нижней стороне стружки периодически отделяются частицы материала. Это оказывает отрицательное влияние на качество режущей кромки инструмента (появление зазубрин) и заготовки (снижение чистоты обработки поверхности, точности соблюдения размеров). Предотвращение нежелательного трения в области контактных поверхностей и, вследствие этого, их перегрева возможно за счёт применения соответствующей конкретному процессу обработки оптимальной геометрии режущей кромки, а также
за счёт оптимизации параметров резания. В частности, с целью предотвращения образования наростов на режущей кромке могут быть приняты следующие меры:
• повышение скорости резания;
• увеличение переднего угла;
• применение покрытий;
• применение эффективного метода охлаждения.
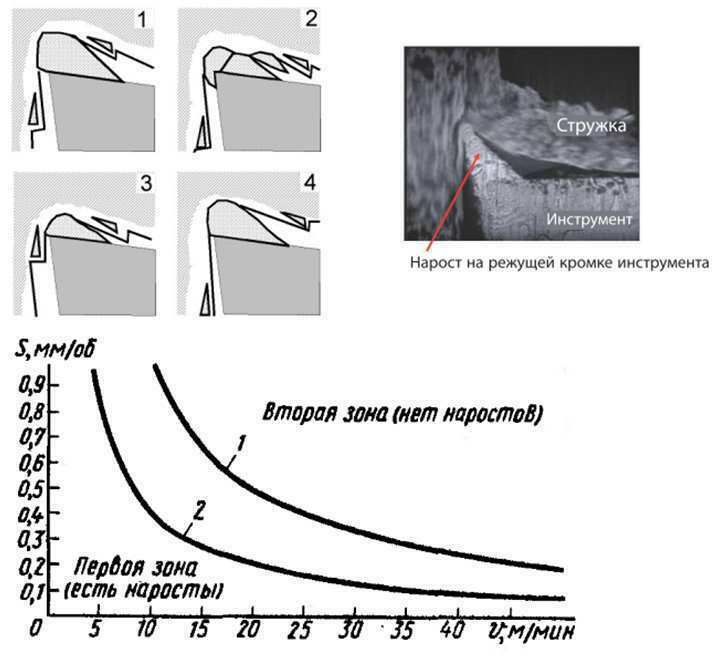
Виды износа, причины и решения.
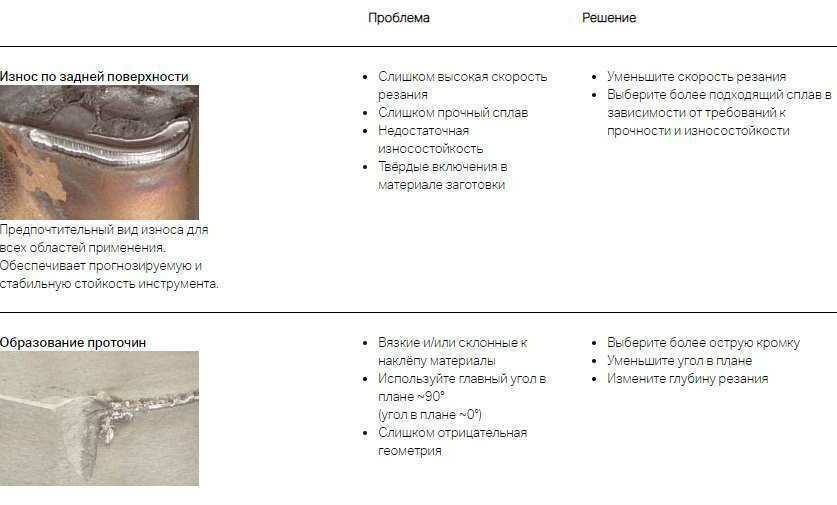
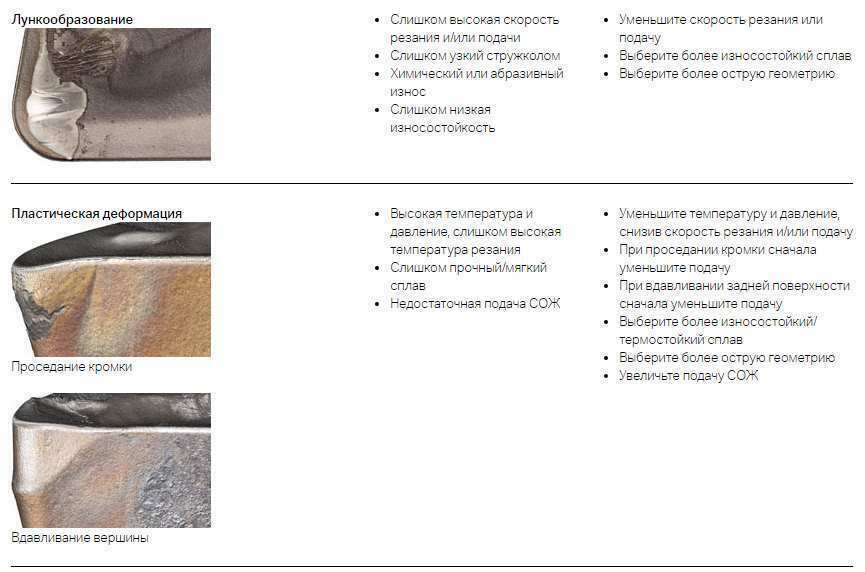
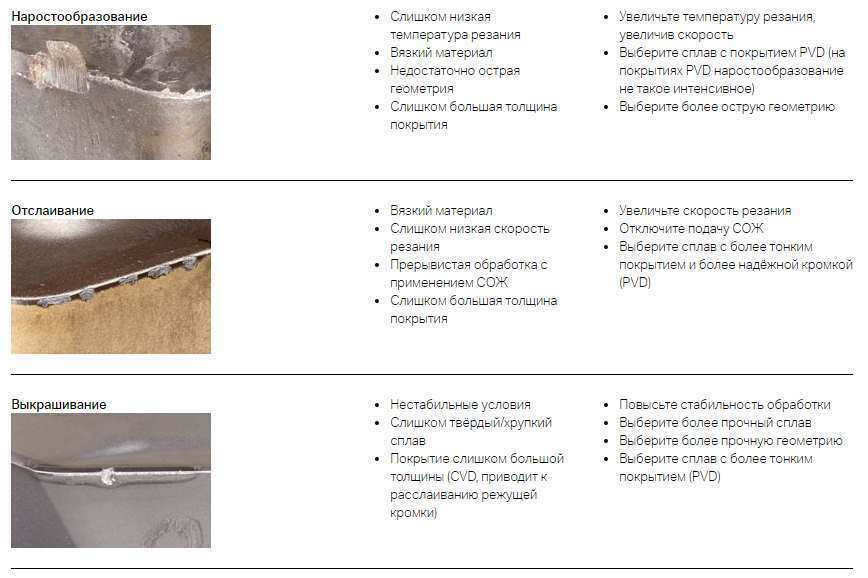
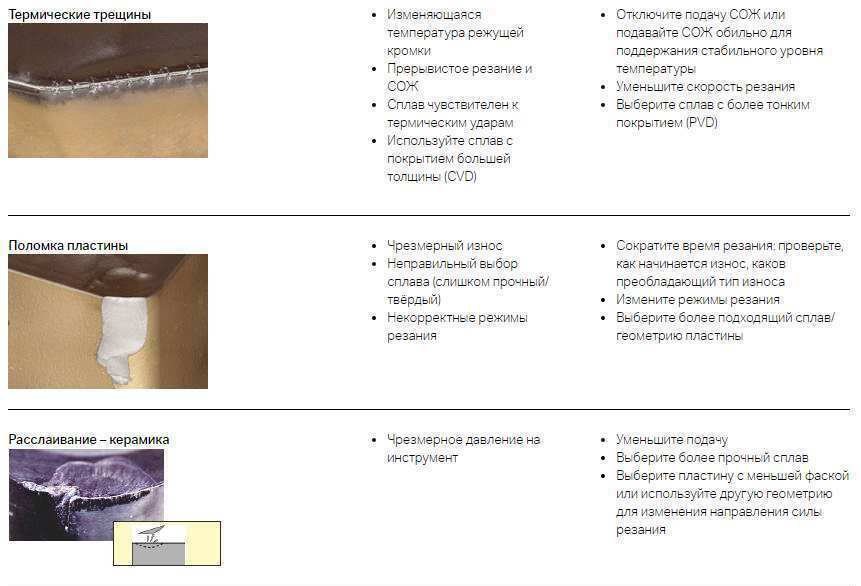
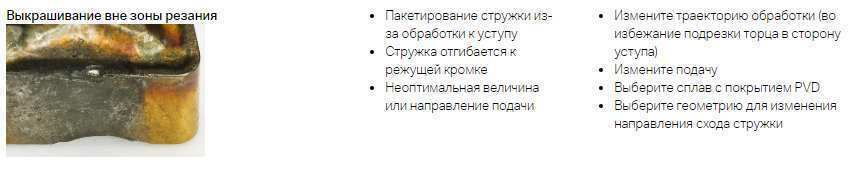
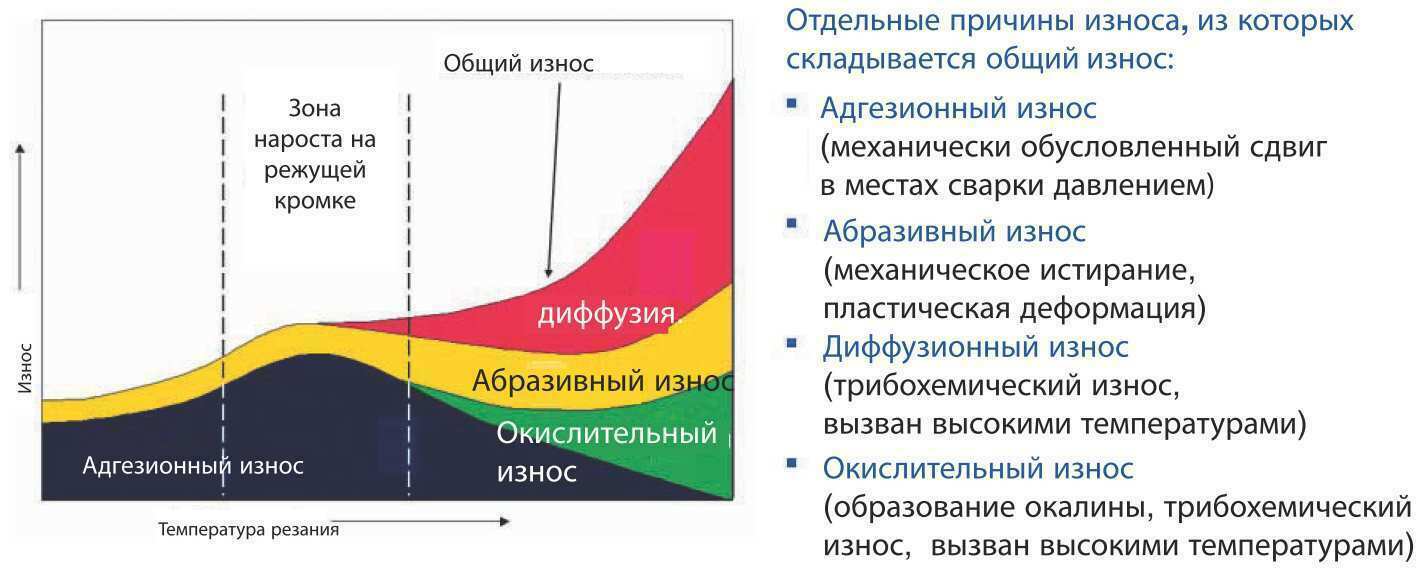
По применимости для легирования можно выделить три группы элементов. Применимость для легирования различных элементов определяется не столько физическими, сколько, в основном, экономическими соображениями.
Mn,Si,Cr,B;
Ni,Mo;
V, Ti, Nb, W, Zr и др.
Легирующие элементы по механизму их воздействия на свойства сталей и сплавов можно разделить на три группы:
влияние на полиморфные (альфа-Fe -> гамма-Fe) превращения;
образование с углеродом карбидов (Сг,Fе)7С3; (Сг,Ре)23С6; Мо2С и др.;
образование интерметаллидов (интерметаллических соединений) с железом - Fе7Мо6; Fe3Nb и др.
По характеру влияния на полиморфные превращения легирующие элементы можно разделить на две группы:
элементы (Cr, W, Mo, V, Si, Al и др.), достаточное содержание которых обеспечивает существование в сталях при всех температурах легированного феррита (ферритные ставы);
элементы (Ni, Mn и др.), стабилизирующие при достаточной концентрации легированный аустенит при всех температурах (аустенитные сплавы). Сплавы, только частично претерпевающие превращение гамма -> альфа, называются, соответственно, полуаустенитными или полуферритными.
Легирование феррита сопровождается его упрочнением. Наиболее значительно влияют на его прочность марганец и хром. Причем чем мельче зерно феррита, тем выше его прочность.
Многие легирующие элементы способствуют измельчению зерен феррита и перлита в стали, что значительно увеличивает вязкость стали. Однако все легирующие элементы, за исключением никеля, при содержании их в растворе выше определенного предела снижают ударную вязкость, трещиностойкость и повышают порог хладноломкости. Никель понижает порог хладноломкости.
Легированный аустенит парамагнитен, обладает большим коэффициентом теплового расширения. Легирующие элементы, в том числе азот и углерод, растворимость которого в аустените при нормальной температуре достигает 1%, повышают его прочность при нормальной и высокой температурах, уменьшают предел текучести.
Легированный аустенит является основной составляющей многих коррозионностойких, жаропрочных и немагнитных сплавов. Он легко наклепывается, то есть быстро и сильно упрочняется под действием холодной деформации.
Легирующие элементы (исключение кобальт), повышая устойчивость аустенита, снижают критическую скорость закалки и увеличивают прокаливаемость. Для многих аустенитных сплавов критическая скорость закалки снижается до 20°С/с и ниже, что имеет большое практическое значение.
Карбидообразующие элементы: Fe - Mn - Cr - Mo - W - Nb - V - Zr - Ti (за исключением марганца) препятствуют росту зерна аустенита при нагреве. Сталь, легированная этими элементами, при одинаковой температуре сохраняет более высокую дисперсность карбидных частиц, и соответственно большую прочность.
Интерметаллиды образуются при высоком содержании легирующих элементов между этими элементами или с железом. Примером таких соединений могут служить Fe7Mo6, Fe3Nb2 и др. Интерметаллиды, как правило, отличают повышенные твердость и хрупкость.
Влияние легирующих элементов в химическом составе стали на различные показатели.
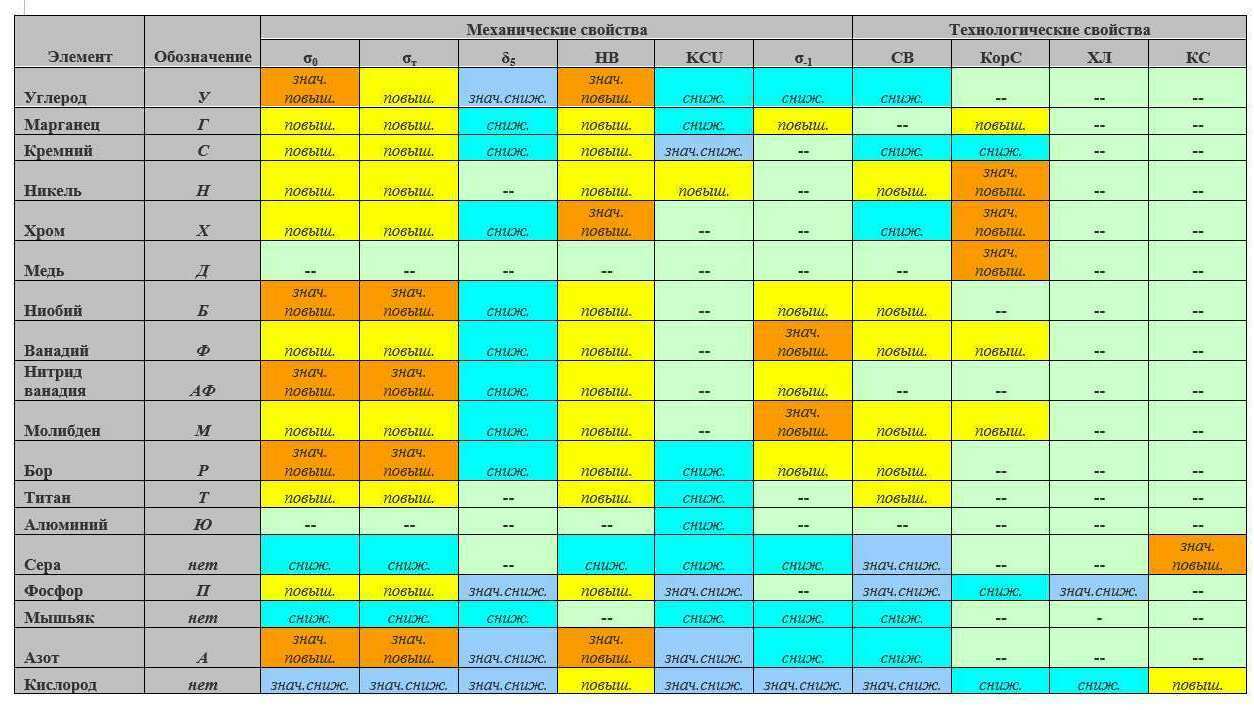
Примечания: σ0-предел прочности; σт- предел текучести; δ5- относительное удлинение; HB – твёрдость; KCU - ударная вязкость; σ-1 - усталостная прочность; СВ - свариваемостьКоррС - коррозионная стойкость; ХЛ – хладноломкость; КС - красностойкостьТаблица показывает примерное влияние отдельных компонентов стали в количествах, содержащихся в малоуглеродистой и низколегированной стали без учета совместного действия нескольких компонентов.Знаки обозначают: (повыш.) - повышает; (знач. повыш.) - значительно повышает; (сниж.) - снижает; (знач.сниж.) - значительно снижает; (--) - не оказывает заметного влияния.
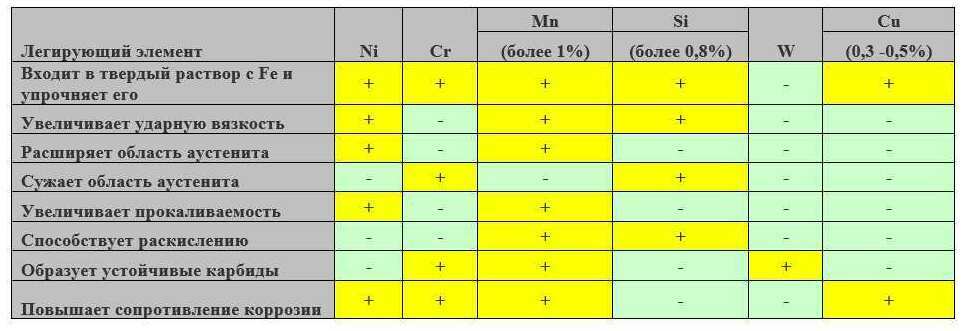
Использование материалов сайта возможно только с письменного разрешения администрации сайта и активной гиперссылкой на источник.
Свяжитесь с нами
Оставьте свое сообщение и мы свяжемся с вами, чтобы предложить лучшие условия сотрудничества!
Звоните: (812) 407-37-03
Пишите: order@carbidetool.ru
ООО «ТУЛЭКС» ИНН 7838092179, г. Санкт-Петербург, улица Аэродромная, д. 8, литер А, офис 418