- 8 (812) 407-37-03
- 197348, г. Санкт-Петербург, улица Аэродромная, д. 8, литер А, офис 418
- order@carbidetool.ru
Фрезерование закаленных сталей 48-65 HRC (...или простым языком, о чем редко пишут...)
В данной статье рассмотрим вопрос обработки закаленных материалов методом фрезерования. Для профессионалов возможна данная статья не несет много полезной информации, но все же, возможно что-то и они найдут интересного для себя.
В чем необходимость фрезерования закаленных сталей?
Вот мнение Michael Minton (национальный менеджер по разработке приложений для компании Methods Machine Tool Inc.):
Во-первых, твердое фрезерование может быть более прибыльным. Твердое фрезерование не только исключает дорогостоящие операции чистовой обработки, но и позволяет получать детали более высокого качества по сравнению с традиционными методами обработки.
«За счет обработки после термообработки Вы не только избегаете вторичных операций, но и устраняете
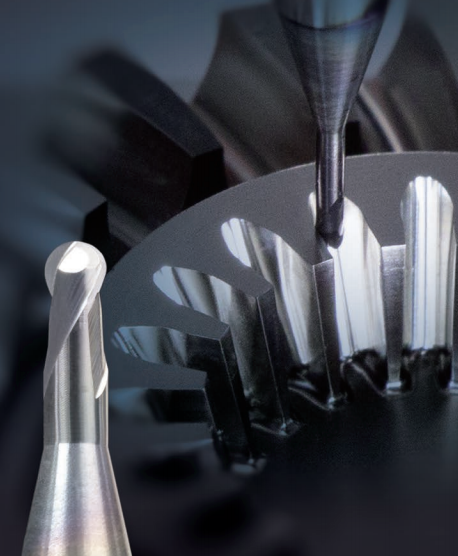
проблемы, связанные с скручиванием, изгибом или иным изменением формы заготовок из-за термической обработки», - сказал Минтон. «Это позволяет изготавливать детали с более высокой точностью и лучшими размерными характеристиками по сравнению с деталями, подвергнутыми термообработке после механической обработки».
Как правило, твердое фрезерование включает резку в основном инструментальной стали или нержавеющей стали с дисперсионным упрочнением, которая была закалена до твердости не менее 50 HRC. После придания начальной формы заготовке в состоянии поставки ее отправляют в печь для закалки, а затем обрабатывают твердосплавными, керамическими или PCBN-инструментами с покрытием. Степень удаления металла в закаленном состоянии минимальна - что делает этот процесс применимым для большинства закаленных деталей.
Однако в зависимости от конфигурации заготовки, объема производства и количества снятия припуска может оказаться целесообразным полностью обработать заготовку из закаленного состояния. Современные станки, передовые материалы для режущего инструмента и сложные программы CAM превращают то, что когда-то было невероятно невероятной обработкой, в операцию, доступную для многих мастерских. По словам Минтона, преимущество механической обработки из закаленного состояния заключается в необходимости резать его только один раз.
Что касаемо инструмента из различных каталогов.....
Нужно понимать, каким бы не был продвинутым тот или иной бренд, но зачастую он не специализируется на проблемах данного типа. Для примера всем известный Sandvik, в большинстве случаев превосходный инструмент, фрезерная обработка закаленных материалов это два основные сплава 4220 (для низкой жесткости СПИД) и 1010 (для хорошей жесткости СПИД). По сути это мелкозернистые тв.сплавы, с покрытием (скорее универсальным). Все что не решает тв.сплав (будь то низкая стойкость инструмента, низкая производительность... или что-то еще не сложилось) значит нужно применять пластины из CBN (а это уже совсем иные цены на инструмент). Если сравнить ассортимент Sandvik монолитного инструмента (фрез) к примеру с ассортиментом каталога Moldino, то выбор явно будет в пользу последнего.
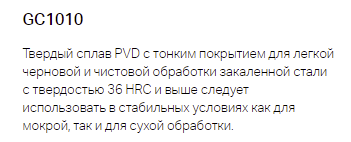
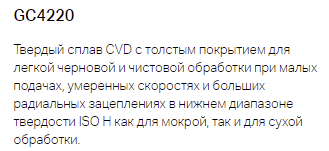

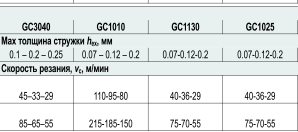
По монолитным фрезам ситуация несколько лучше...
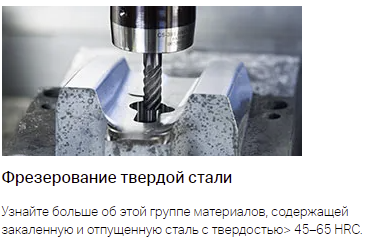
Или возьмем как пример Iscar. Очень хороший инструмент, как и Sandvik во многих случаях. И по каленым материалам работает (но не факт что это оптимальное решение во всех случаях). Как правило для пластин предлагается тоже два сплава 808 и 908, для монолитного инструмента выбор несколько больше. Покрытие многослойное, но чаще на основе TiAlN и AlTiN, и оно скорее универсальное, для решения задач с температурой в зоне резания до 800 градусов С. Причем чаще это PVD покрытие. Инструмент конечно работает при определенных режимах и имеем стойкость и производительность пусть и не самую лучшую, но вполне подходящую для решения многих проблем для определенных материалов при определенной твердости.
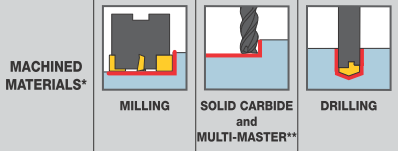
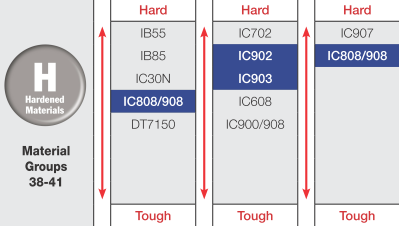

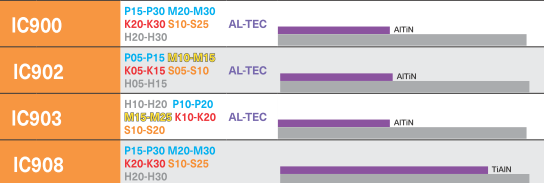
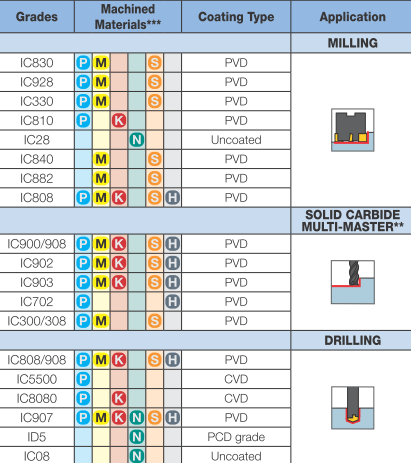
Или вот к примеру Lamina (в некотором роде их универсальные сплавы, согласно концепции производителя для большинства материалов и покрытие типа PVD (TialN)). Их пластины работают и при твердости 60-63 HRC и для мелкосерийного производства вполне сгодится, но не для серийного. По указанной ссылке производитель приводит пример обработки и режимы резания для закаленных материаловhttps://www.lamina-tech.ch/single-post/high-feed-milling-on-hardened-steel . При этом рекомендуются низкая скорость, повышенная подача, высокая жесткость, прочная геометрия пластины и т.д.


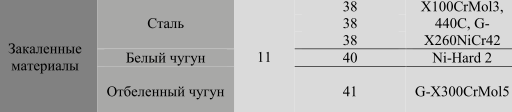
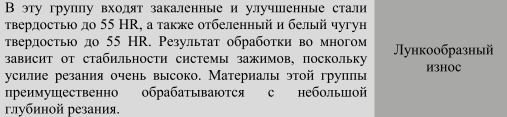
Начиная разбираться с проблемой, хотелось бы для начала определиться с понятием - закаленная (калёная) сталь.
Для кого-то и 40-45 HRC это уже проблема наводящая ужас, а кому-то приходится работать со сталями и под 60-65 HRC.
В литературе часто встречается разбивка по таким диапазонам
- до 42-48 HRC (в некоторых источниках до 50 HRC)
- 48-58 HRC (в некоторых источниках 45-60 HRC)
- более 60 (62-65) HRC
- иногда встречается в литературе еще один диапазон 65-70 HRC и до 90 HRA (это область применения PCBN инструментов)
Нас в большей степени будут интересовать первые три диапазона твердости закаленной стали. Кстати еще нужно оговорится, что и хим.состав закаленных сталей, тоже оказывает существенное влияние на обрабатываемость (но этот материал уже выходит за рамки данной статьи). Так же важно понимать вид термообработки и глубину закаленного слоя - либо это сквозная закалка стали, либо это варианты ХТО (цементация, нитроцементация, азотирование).
К чему всё это...
А дело в том, что незначительное увеличение твердости по шкале HRC вызывает значительное увеличение нагрузки на режущую кромку инструмента. И это важно, в выборе геометрии режущей части инструмента. Ниже, для наглядности, представлена информация с сайта Hoffmann Group.
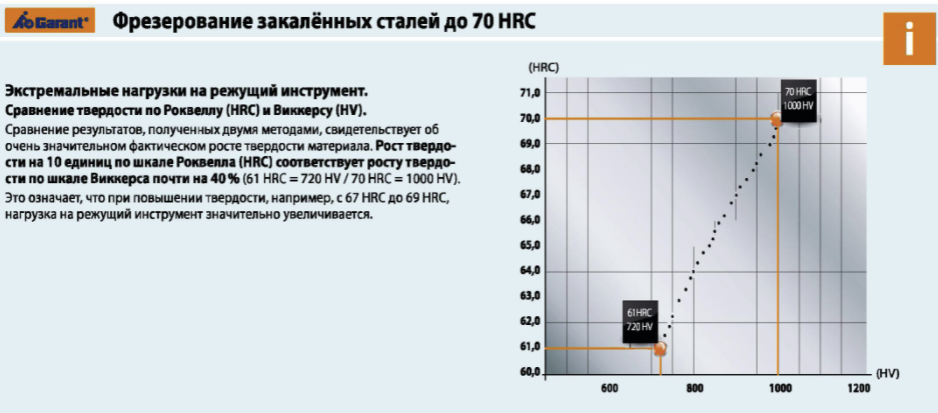

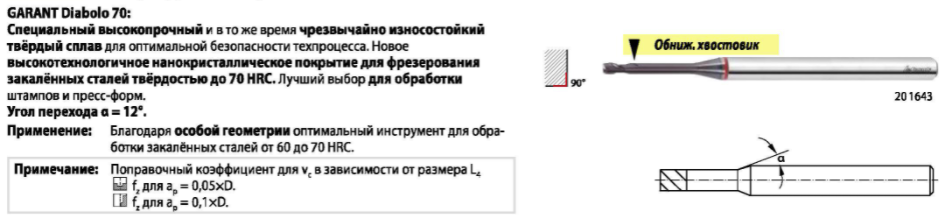
Уильям Дж. Ховард-младший, менеджер по продукции для вертикальных обрабатывающих центров Makino, написал книгу по твердому фрезерованию - «Решения для высокоскоростного твердого фрезерования» от Hanser Gardner Publications.
Он предлагает такие рекомендации, согласно вышеуказанному принципу разбивки по диапазонам твердости.
Если в цехе есть действительно высокопроизводительный станок с более производительным инструментом, и при отсутствии рекомендаций экспертов, предлагающих более конкретные параметры, диапазоны и уравнения, представленные ниже рекомендации, должны дать хорошую отправную точку для применения твердого фрезерование более эффективно.
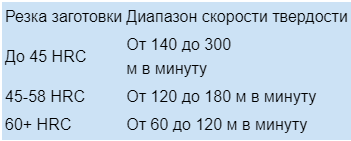
Использование концевой фрезы с шаровой головкой для твердого фрезерования сложных поверхностей штампа и пресс-формы только делает потребность в высокой скорости более вероятной. Когда шарообразный инструмент режет на небольшой осевой глубине резания, инструмент не режет на весь свой диаметр.
Чтобы определить значение частоты вращения, необходимое для достижения необходимого значения sfm с таким инструментом, используйте эффективный диаметр инструмента, который рассчитывается по формуле на рисунке

Нагрузка на кромку или скорость подачи в мм на зуб можно приблизительно определить как функцию от фактического диаметра инструмента. В качестве отправной точки для подачи жесткого фрезерования используйте следующие диапазоны:
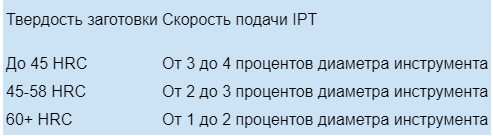
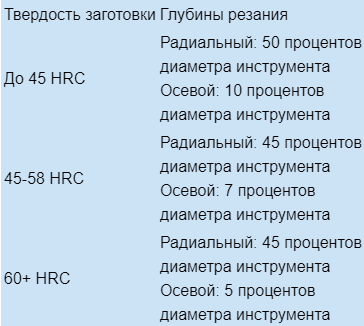
Глубина резания зависит от твердости материала - до определенной степени. Более важным фактором, влияющим на ступенчатость (или радиальную глубину резания), может быть желаемая чистота поверхности детали. Это максимальная глубина резания, которая должна использоваться при твердом фрезеровании.
Эти максимальные значения продлевают срок службы инструмента. Однако, когда целью твердого фрезерования является также гладкость поверхности, может потребоваться еще меньшая радиальная глубина.
Само требование к чистоте поверхности может быть использовано для расчета этого более легкого перехода. Это потому, что значение шероховатости поверхности является показателем высоты неровностей между проходами, а высота неровностей между соседними проходами может быть математически определена по радиусу шара.
Формула, связывающая радиальную глубину резания с чистотой поверхности с помощью сферического инструмента, показана на рисунке. Термин косинус отражает возможность обработки углов уклона или конических или наклонных поверхностей. «А» - это средний угол зацепления между инструментом и наклонной поверхностью.

Скорость подачи также влияет на качество поверхности. Проход каждой режущей кромки по мере продвижения инструмента создает собственный «острие». Следовательно, если целью является гладкая поверхность, то то же значение, вычисленное как предел радиальной глубины, также должно применяться в качестве верхнего предела скорости подачи инструмента в мм на зуб.
Ключом к стойкости инструмента и качеству обработки при фрезеровании, и особенно высокоскоростном фрезеровании закаленной стали, является поддержание постоянной стружкодробной нагрузки на режущие кромки фрезерного инструмента.
Нагрузка на кромку широко варьируется; если нагрузка слишком мала или слишком велика, инструмент либо изнашивается слишком быстро, либо выкрашивается, либо ломается. Многочисленные проходы с высокой скоростью и подачей с небольшой глубиной резания - лучший способ обеспечить качество продукции.
Из практики, даже казалось бы на первый взгляд такие не существенные моменты.
Одна и таже фреза при одинаковых ....станок, деталь, оснастка, скорость резания.... но работая по разным составленным управляющим ЧПУ программам дает различную стойкость.
В первом случае это были обычные проходы фрезой (по сути строчками), при этом стойкость инструмента составила в пределах 20-25 минут рабочего времени.
Во втором случае это была изменена программа, с траекторией движения инструмента обеспечивающий плавный вход по дуге в заготовку, постоянство припуска (нагрузки) на режущей кромке, сглаживание траектории движения и отсутствие выводов инструмента из материала до конца обработки...при этом стойкость инструмента составила более часа рабочего времени.
Еще из практики, по поводу оснастки для установки инструмента.
Одна и таже фреза при одинаковых...станок, деталь, режимы...но зажатая в различной шпиндельной оснастке (применялась стратегия скоростной обработки)
В первом случае это была термооправка, и на фрезе, довольно быстро, появлялись микросколы на кромке и требовалась коррекция по скорости резания (хотя казалось бы, термооправка, хорошая жесткость закрепления). Во втором случае это был цанговый патрон ER типа повышенной точности, при этом фреза работала даже спокойнее, чем в первом случае, при умеренных режимах.
И в третьем случае, это был гидропластовый патрон, его применение позволило даже увеличить скорости резания (а следовательно и производительность), улучшило не только стойкость инструмента, но и чистоту обработанной поверхности.
Нужно напомнить, что существует и стратегия ВСО со своими особенностями, о которых ранее речь шла в статье по указанной ссылке https://carbidetool.ru/high_speed_cutting .
Обработка с применением ВСО стратегии накладывает свои требования и на инструмент, и на оборудование, и на управляющие программы
Также способствует снижению проблем с обработкой закаленных и твердых материалов применение станков с технологией Ultrasonic https://carbidetool.ru/ultrasonic_technology
Что касаемо покрытий....
Многие возразят: какая разница какое покрытие, лишь бы толстое и на износ хорошо работало.
И это тоже отчасти верное утверждение в определенных случаях. Если Вы работаете на невысоких режимах при хорошей СПИД, и температура в зоне резания не высока, и при этом в обработке материал по твердости близкий к 60 HRC, то зачастую пластины с многослойным СVD покрытием, в составе которого есть толстый слой типа Al2O3 и ультрамелкозернистой основой дадут вполне хороший результат. Для материалов 40-55 HRC предпочтительна более острая кромка инструмента и PVD покрытие.
Применение скоростной стратегии обработки инструментом с универсальным покрытием малоэффективна, т.к. температура в зоне резания может быть близка или даже выше 600-800 градусов, и стойкость подобного покрытия (и самого инструмента) будет крайне не высокой.
Для понимания сути проблемы хорошо бы иметь наглядность, какой тип износа преобладает с повышением температуры в зоне резания.
Вот два рисунка, один из каталога Hoffmann Group, другой из книги профессора А.Д. Макарова.
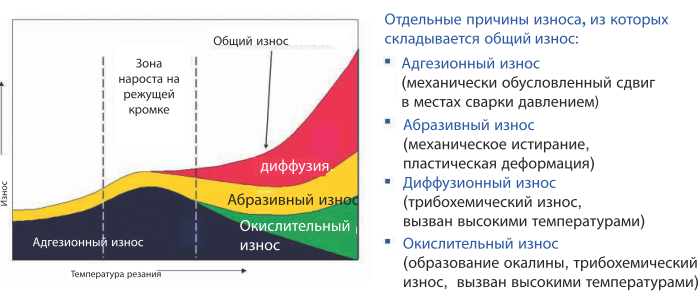
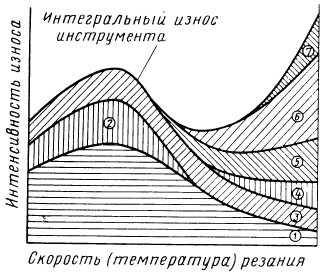
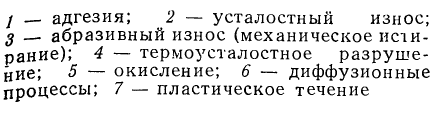
Различные виды покрытий имеют не только разный хим.состав, толщину, коэф.трения и т.д., но разную износостойкость при определенной температуре резания. При этом для обработки закаленных сталей покрытие должно не только хорошо работать на износ при высокой температуре, но и воспринимать знакопеременные нагрузки, перепады температур и иметь малую склонность к диффузии.
Чисто для примера типы покрытий из каталогов Silmax (Италия) и HGT (Тайвань) для монолитного инструмента.
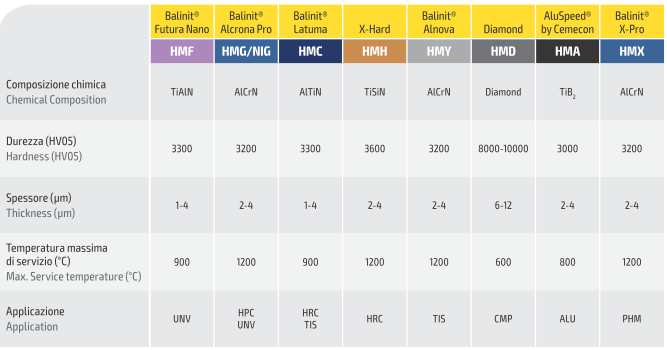
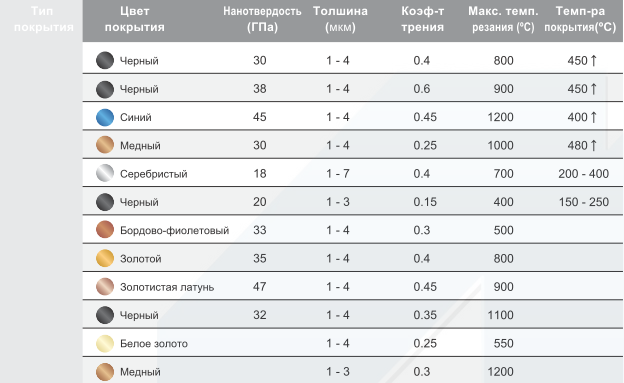
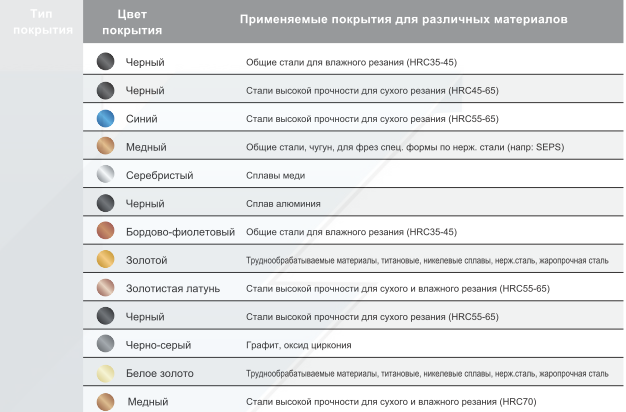
Назревает вопрос: "А какой и чей инструмент тогда целесообразно применять для фрезерования закаленных материалов?"
Вот тут советы раздавать сложно, не хочется плохо говорить о любых производителях инструмента, но выделить более интересных видимо стоит.
На ряду с известными брендами такими как Seco, Fraisa, Emuge Franke и т.д. хотелось бы выделить:
Японский производитель инструмента Hitachi, ныне это часть фирмы с наименованием Moldino http://www.moldino.com/ - это не только монолитный осевой инструмент высокого качество и большим ассортиментом, с вылетом до 90 L/D, но и фрезы со сменными пластинами, сверла и т.д. Производитель ориентирован на инструмент для производства именно штампов и пресс-форм.
При этом инструмент этого производителя правильно понимает твердости выше 60HRC+.
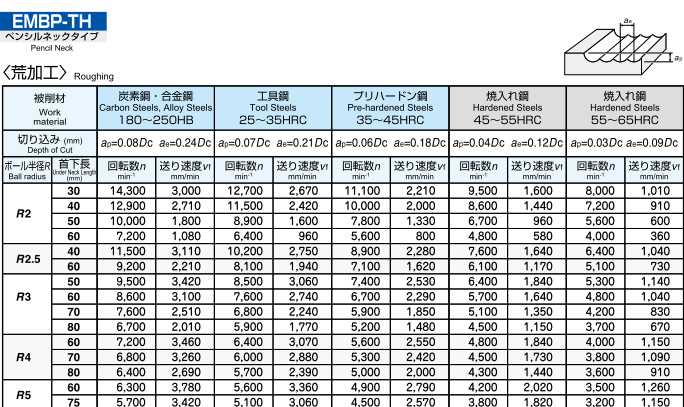
Инструмент со сменными тв.сплавными пластинами

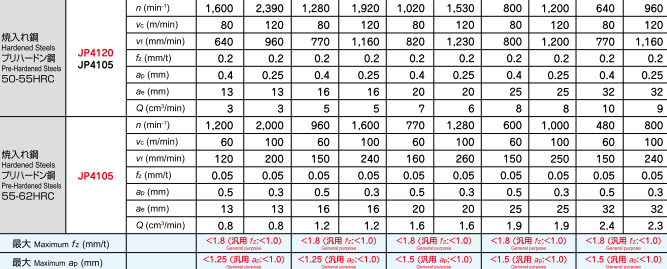
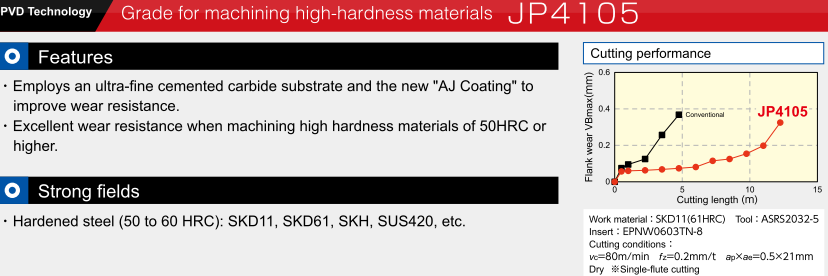
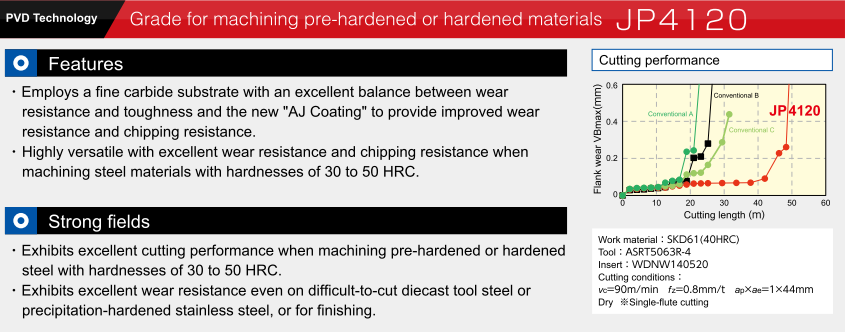
Для увеличения нажмите на картинку
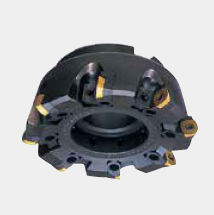
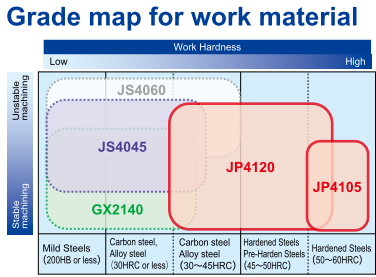
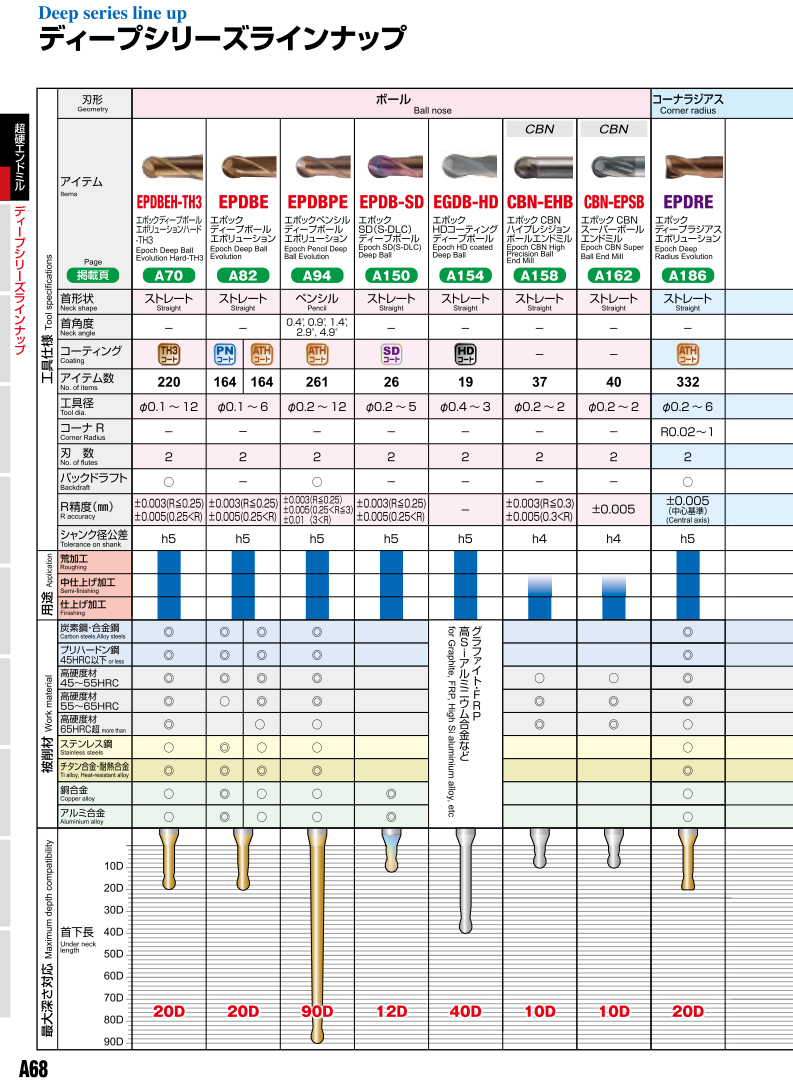
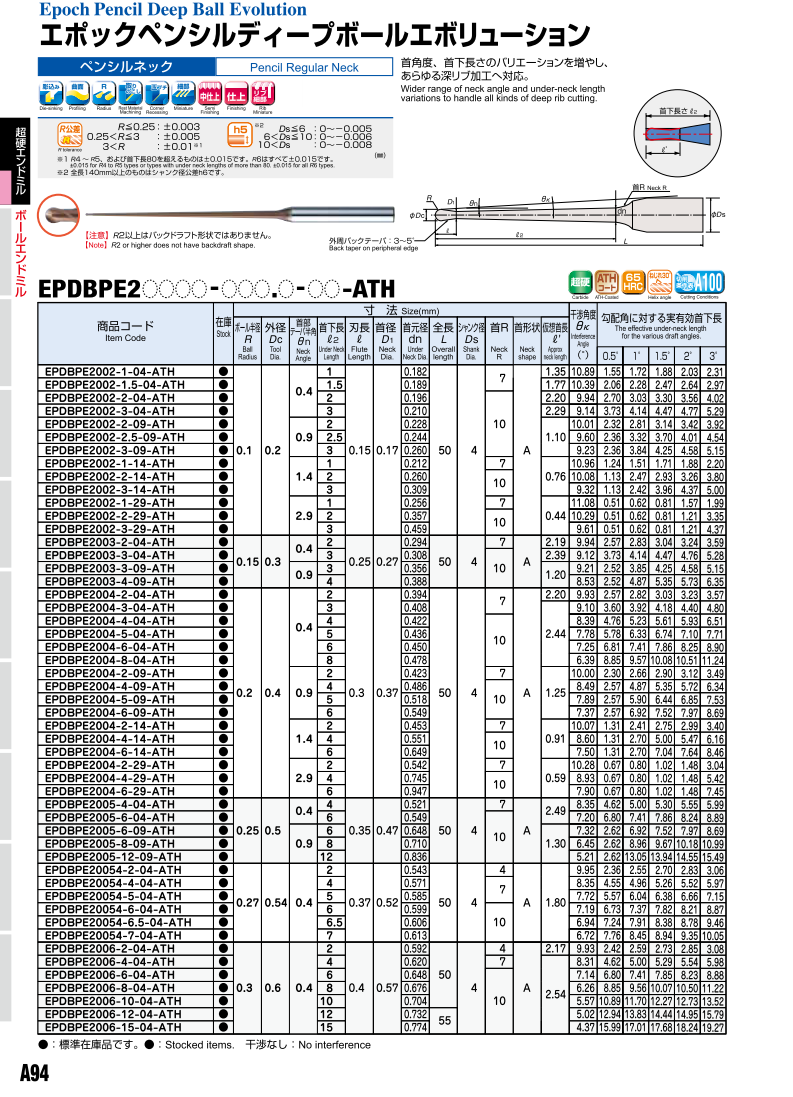
Не безынтересным является и инструмент другого японского производителя Dijet https://www.dijet.co.jp/english/
Фрезерные тв.сплавные пластины производителя тоже хорошо справляются с материалами твердости выше 60HRC+
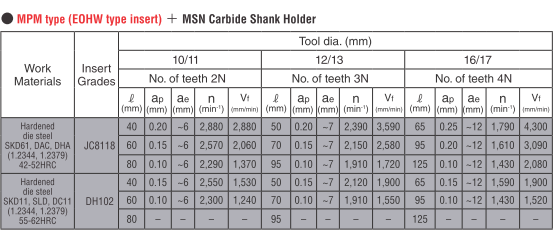


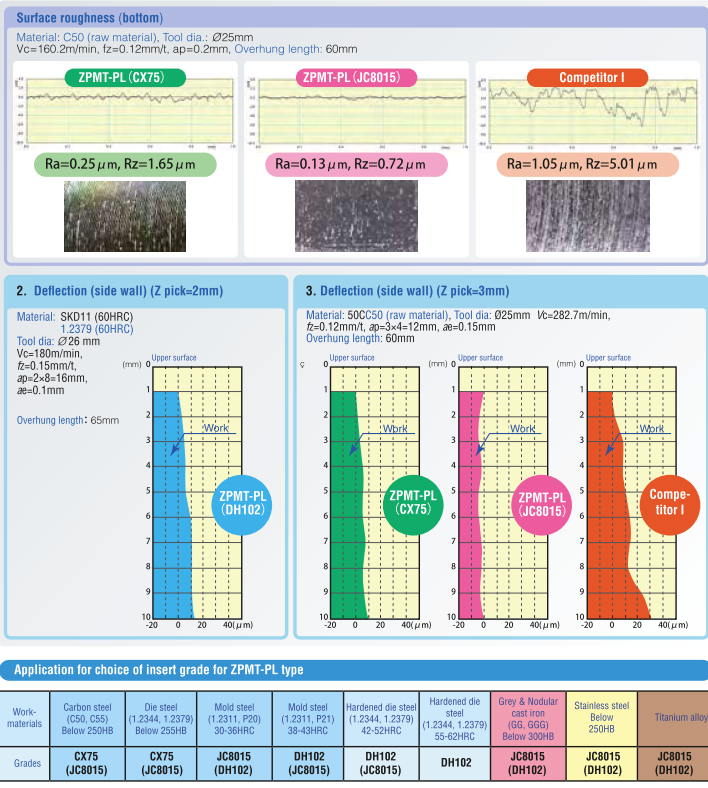

Для увеличения нажмите на картинку
Монолитные фрезы
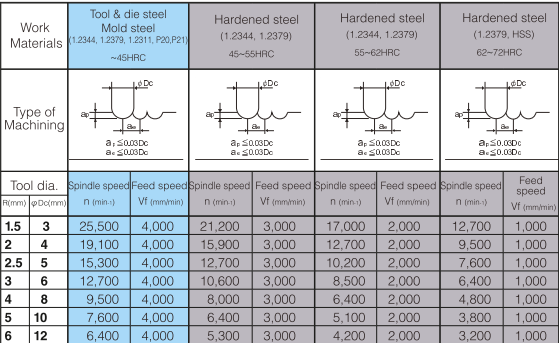
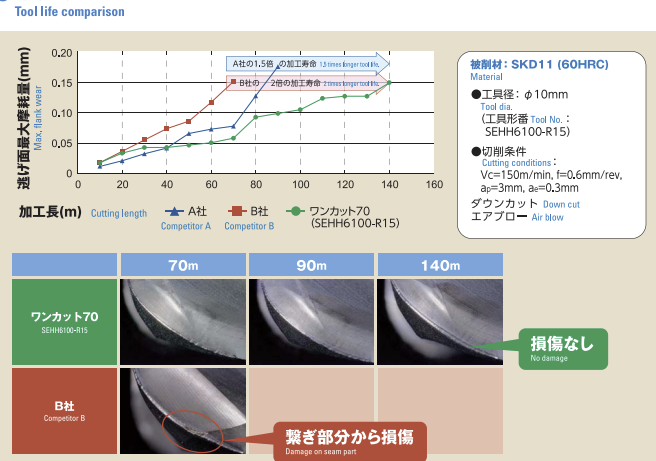
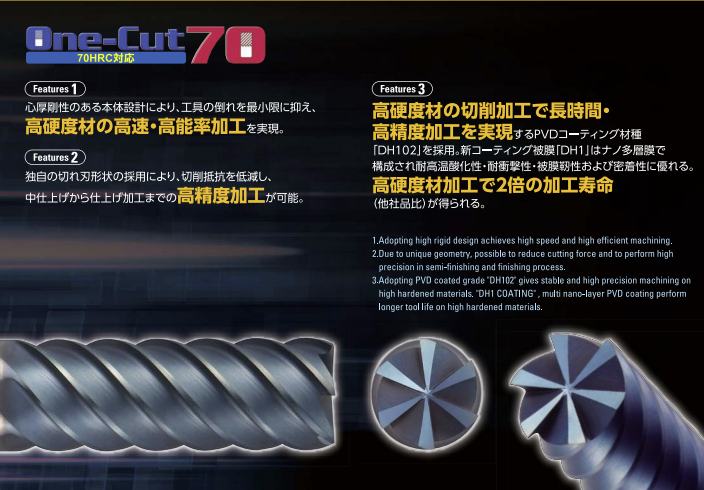
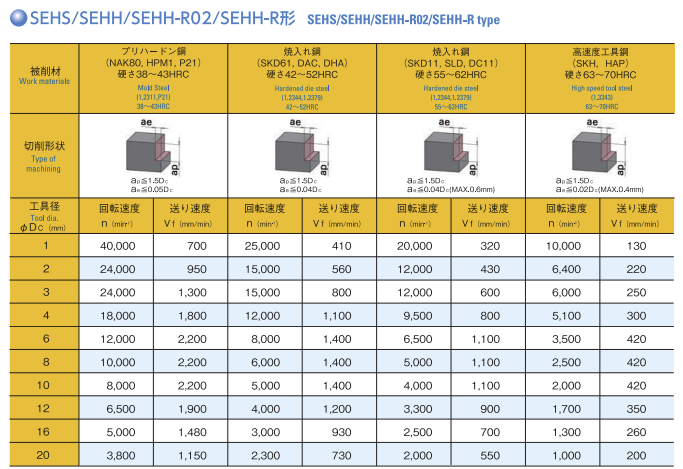
Производителей осевого монолитного инструмента для фрезерования закаленных сталей довольно много, можно применять даже фрезы китайского фабричного или тайваньского производств. Но вот когда речь заходит о высокой производительности процесса, высокой технологической повторяемости, то многие такие дешевые инструменты становятся не целесообразны.
Отдельно хотелось бы выделить несколько брендов довольно интересных для данной темы
Union Tool https://www.uniontool.com/catalogues/tungsten-carbide-end-mills-catalogues/ это не только высококачественные тв.сплавные фрезы, но и мелкоразмерные фрезы из CBN
инструмент для обработки материалов твердостью до 95 HRA
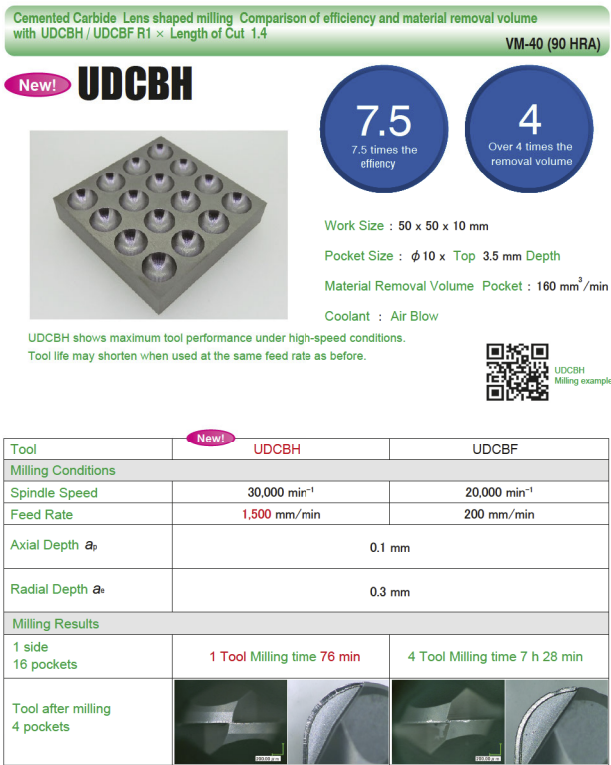
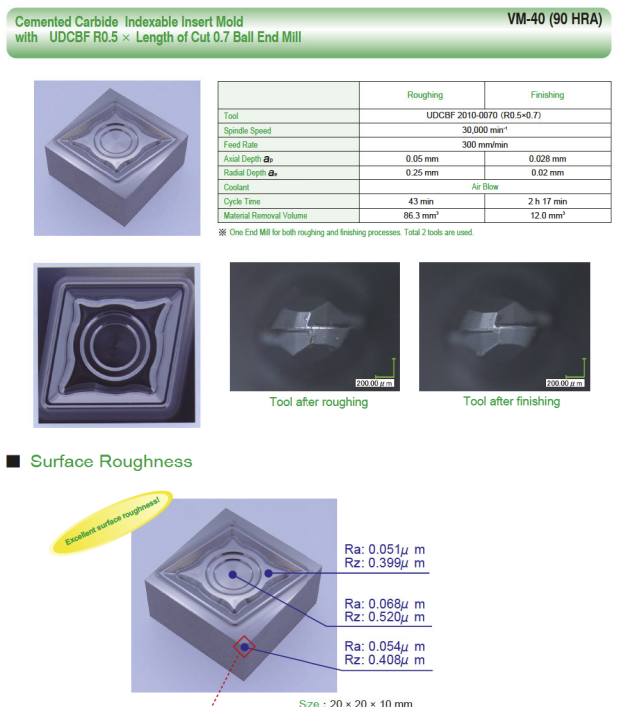
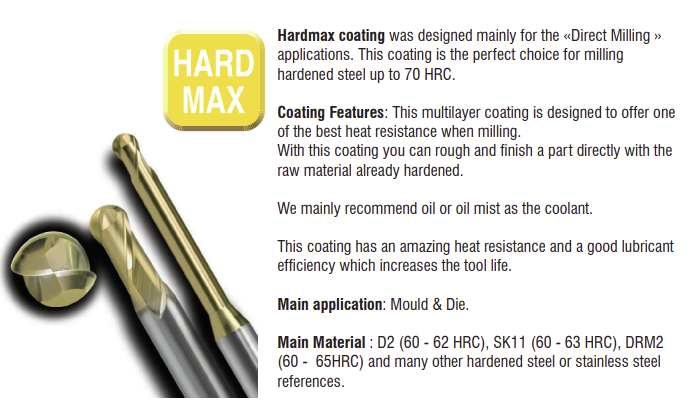
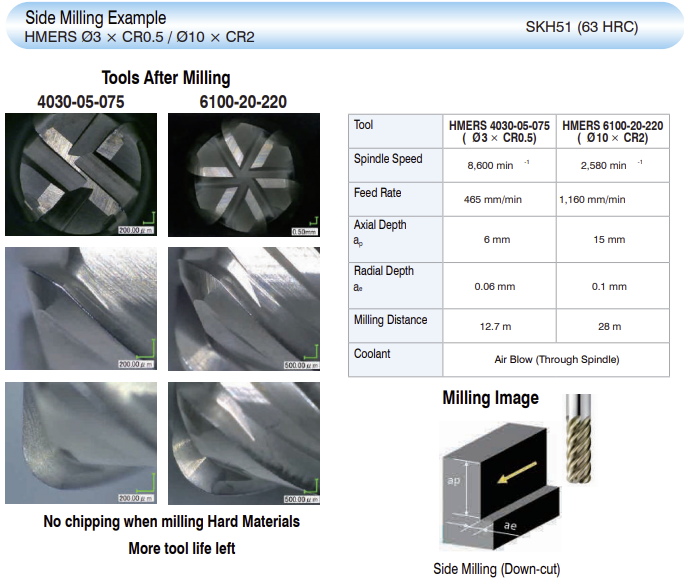
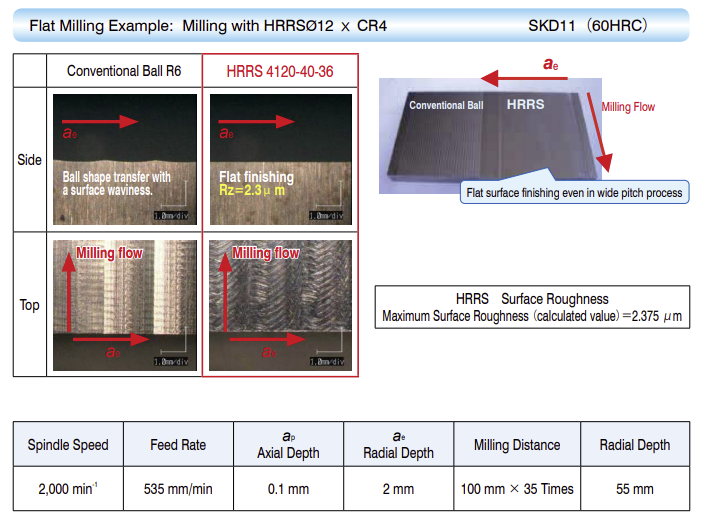
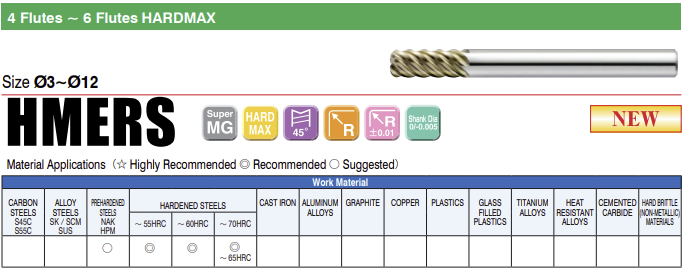
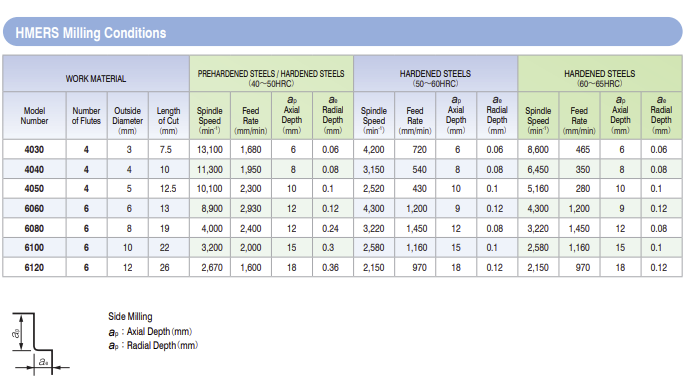
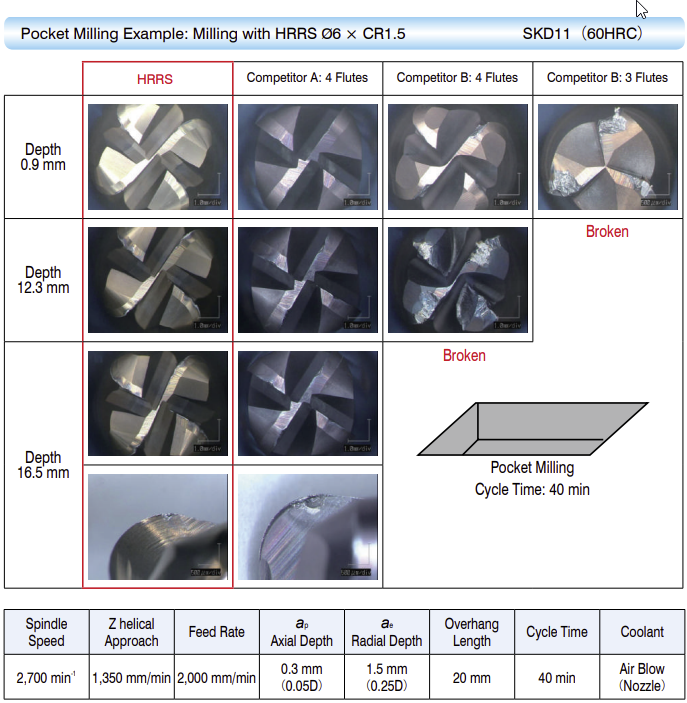
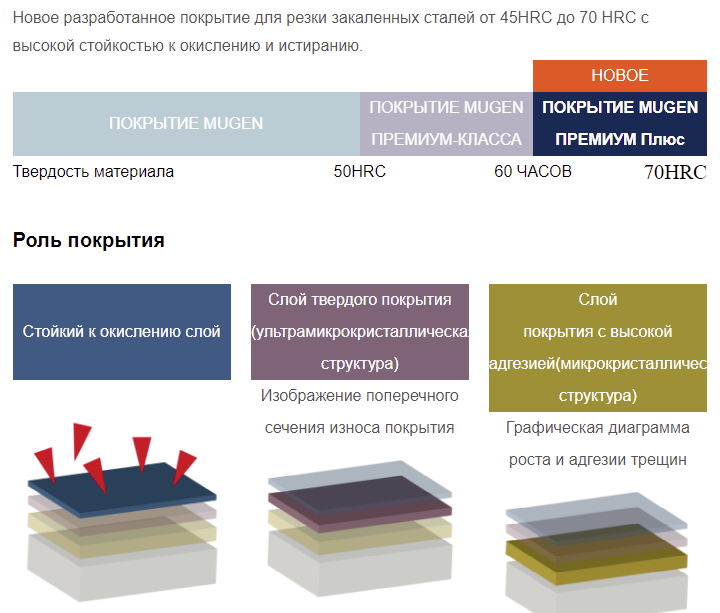
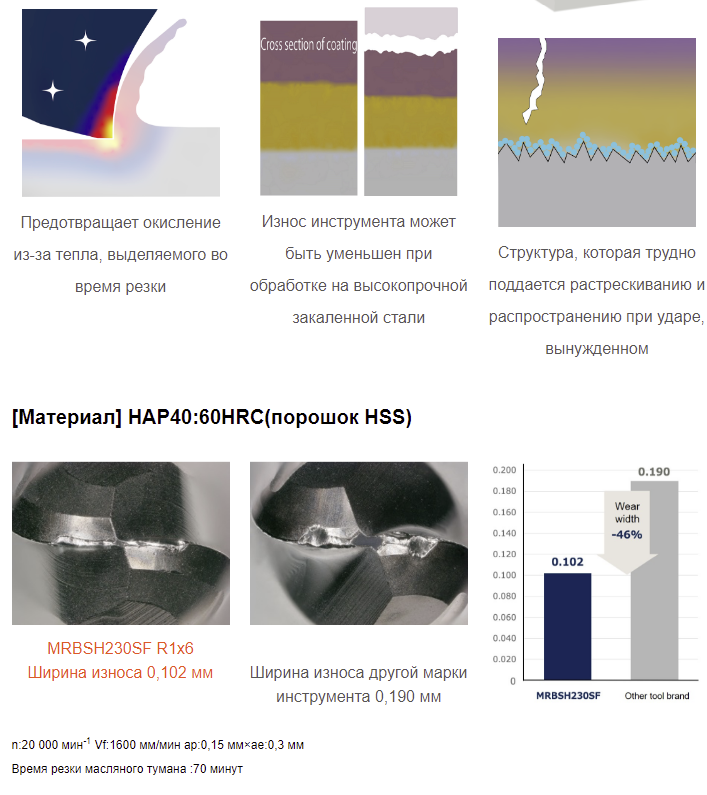
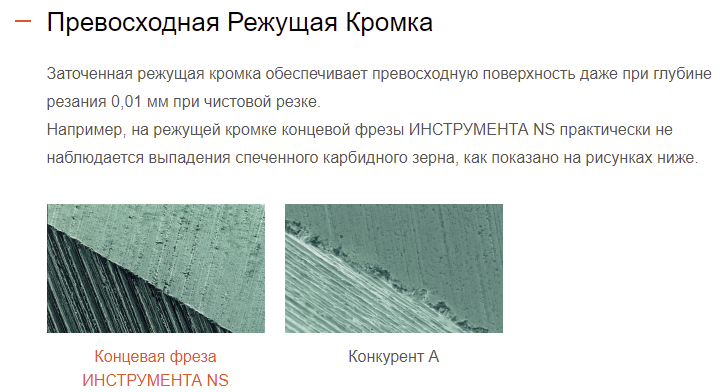
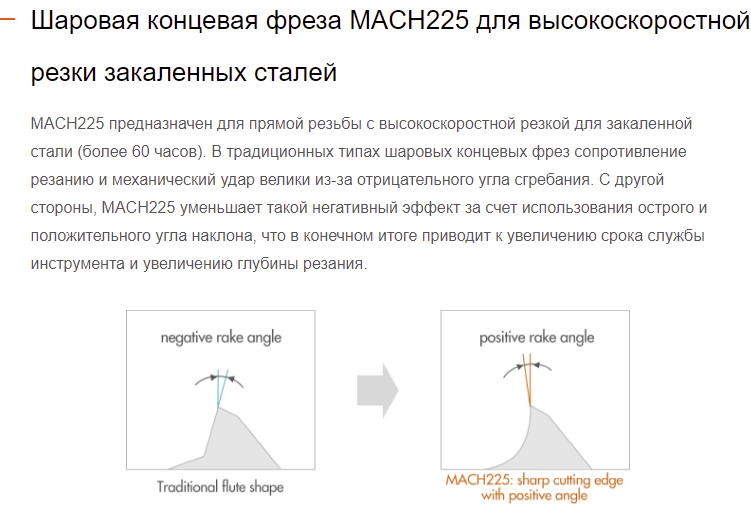
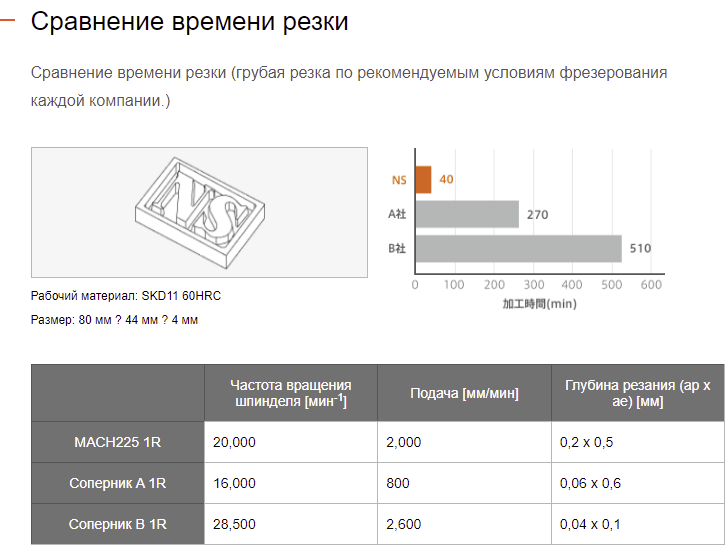
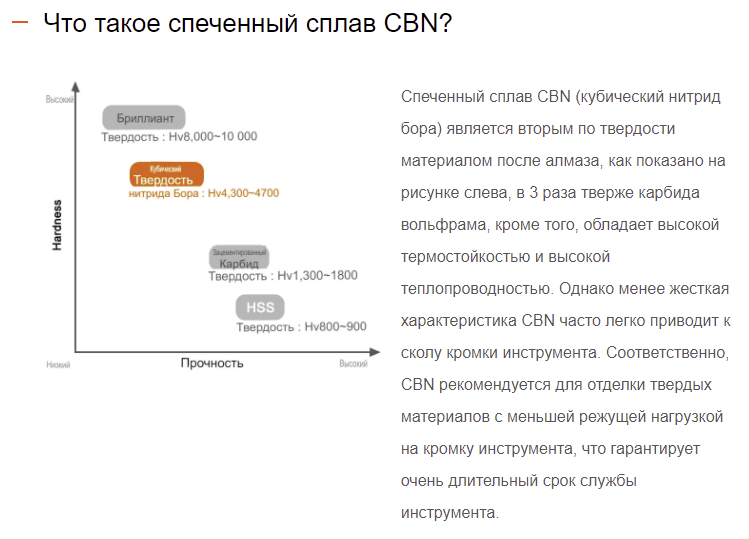
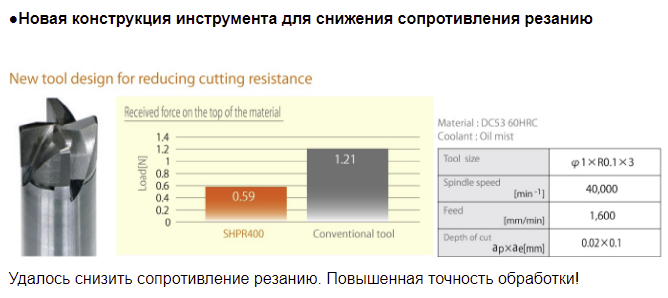
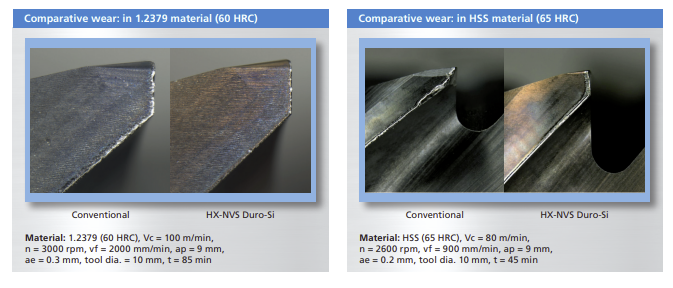
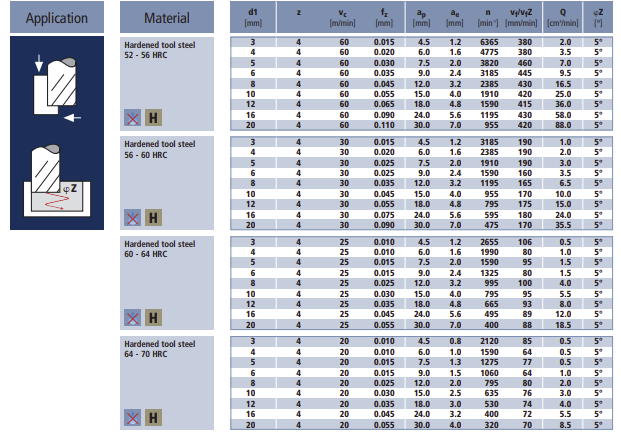
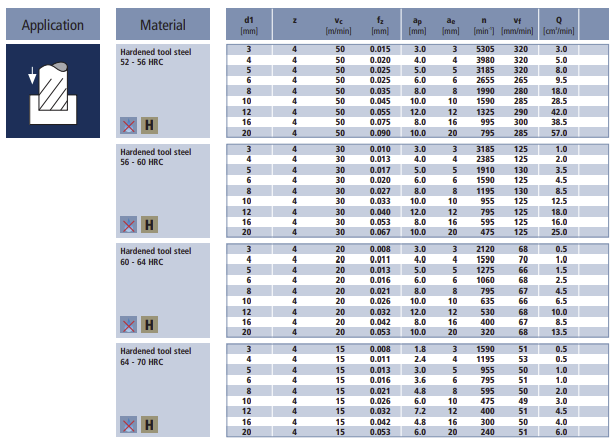
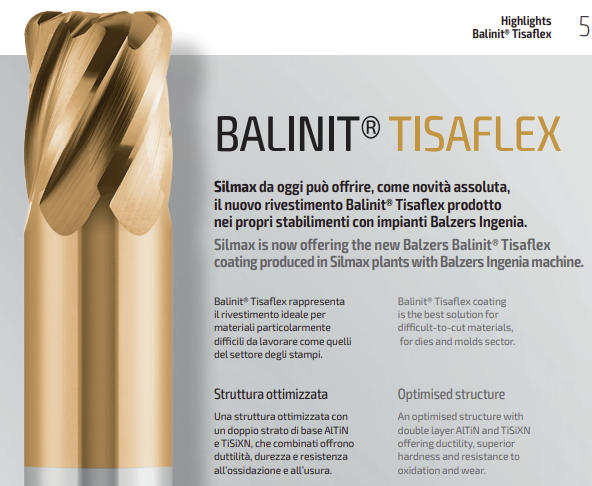
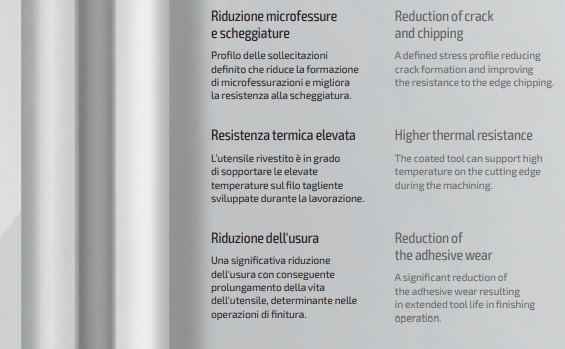
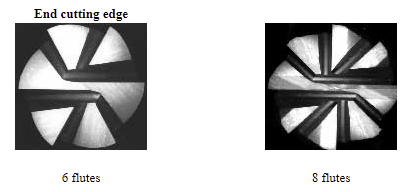
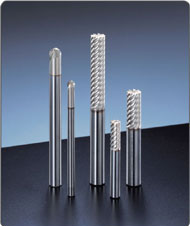
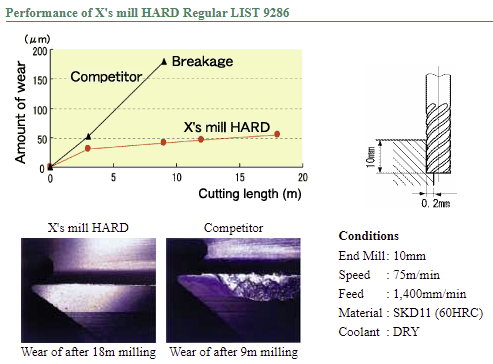
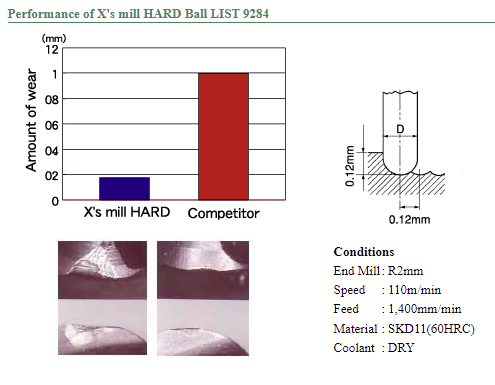
Говоря про корпусные фрезы со сменными тв.сплавными пластинами, нужно отметить, что не все фрезы и формы и геометрии пластин подходят для обработки закаленных сталей. Наибольшей популярностью пользуются круглые пластины и пластины для фрез для больших подач. Но при этом для обработки закаленных материалов такие пластины имеют соответствующую геометрию режущей кромки, сплав и износостойкое покрытие.
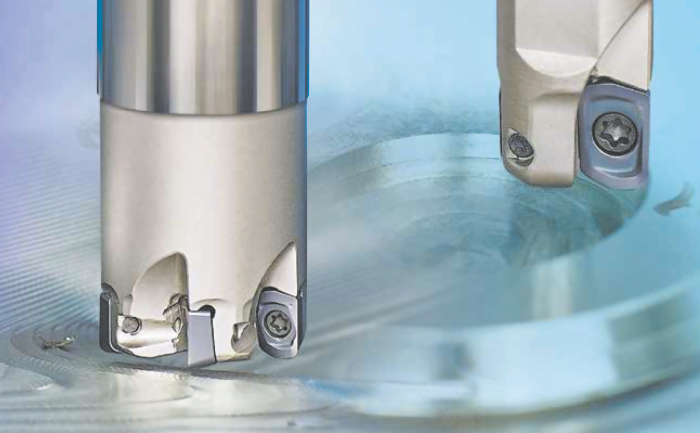

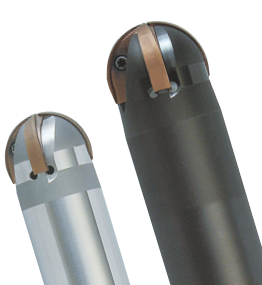
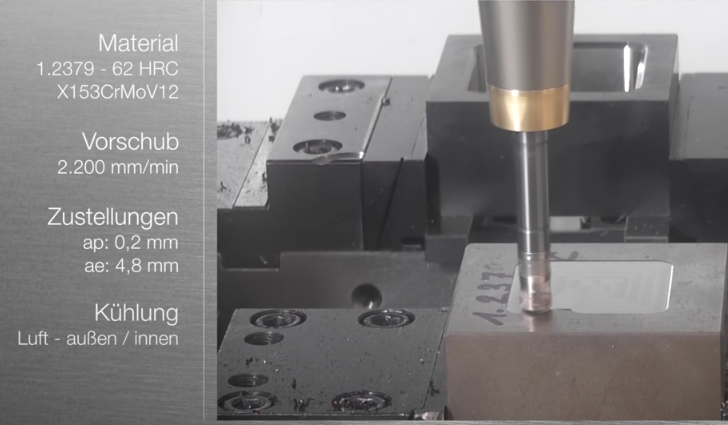
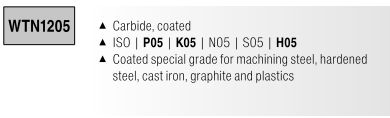
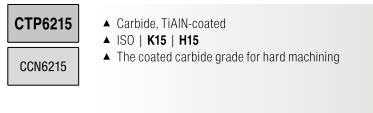
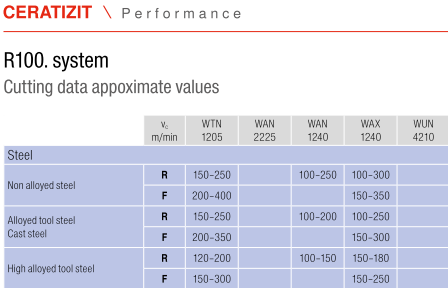
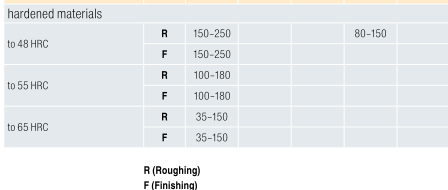
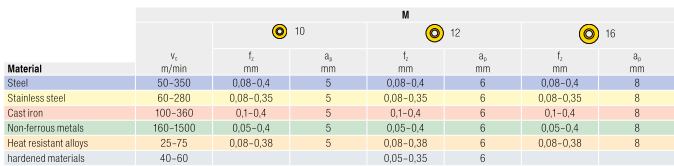
Но как бы не совершенствовались тв.сплавные инструменты, какие бы покрытия не применялись...но применение инструментов из PCBN и керамики, на материалах с твердостью выше 60 HRC наиболее целесообразно с точки зрения повышения производительности обработки (но при этом дополнительно накладываются требования более высокой жесткости СПИД), а на материалах с твердостью выше 63-65 HRC керамика и PCBN являются единственным возможным решением данной проблемы.
Из-за высокого уровня энергии, необходимого для создания стружки в закаленной стали, и абразивного действия заготовки, нужен инструмент из ультрамелкозернистой тв.сплавной заготовки с минимальным содержанием кобальта, чтобы выдерживать высокие нагрузки и температуры, наблюдаемые при сухой обработке.
Карбиды с покрытием обеспечивают хороший компромисс между термостойкостью и износостойкостью, а также между прочностью и вязкостью. Керамика и PCBN определенно обладают хорошими тепловыми и износостойкими свойствами, но они более хрупкие, когда дело касается ударов и неблагоприятных условий резания.
Керамика плохо себя чувствует в ситуациях, когда возникает вибрация (чрезмерный вылет инструмента и менее жесткие шпиндели или приспособления). Повреждения инструмента из керамики обычно носит механический характер. Даже при нормальных условиях фрезерования керамический инструмент изгибается при входе в резание и выходе из него.Этот изгиб вызывает скалывание режущей кромки на микроскопическом уровне. То, что выглядит как износ по задней поверхности, на самом деле является микросколом, вызванным прогибом и усилиями, действующими на инструмент. По мере распространения микросколов инструмент в конечном итоге выходит из строя.
Однако, несмотря на это, керамика широко применяется для фрезерования закаленных сталей, чугуна и жаропрочных сплавов. Это связано с тем, что кобальтовая связка карбида начинает размягчаться при температуре около 800 ° С, в то время как керамика может эффективно работать при температурах примерно до 2000 ° С. «Керамика и PCBN появляются там, где карбид исчезает», чем выше твердость, тем больше тепло, выделяемое во время обработки.
Поскольку керамика более безразлична к нагреву, скорость резки может быть намного выше. Во многих случаях твердость карбидов позволяет увеличить нагрузку на зуб, но значительное увеличение скорости с применением керамических инструментов, обеспечивает более высокую производительность. Все сводится к экономике...
Керамическими могут быть не только пластины для фрез, но сами монолитные фрезы (при этом они обеспечивают стойкость по времени соразмерную с тв.сплавными фрезами, но ведут обработку на скорости в 10-15 раз выше, чем тв.сплавные фрезы). Повышение температуры в зоне резания позволяет вести скоростную обработку при меньших силах резания.
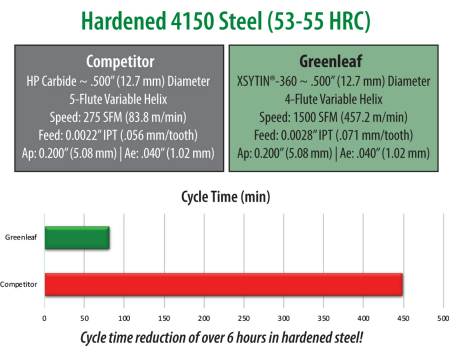
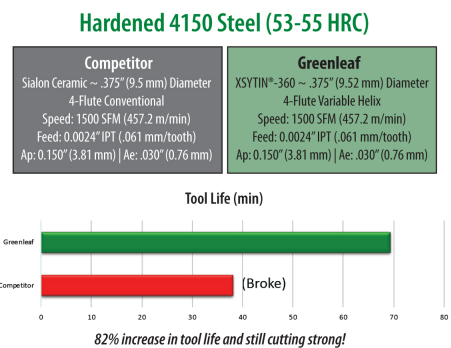
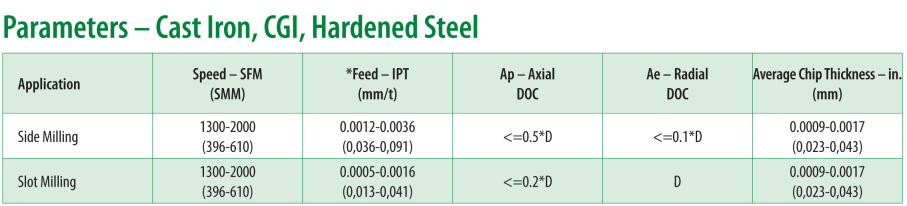
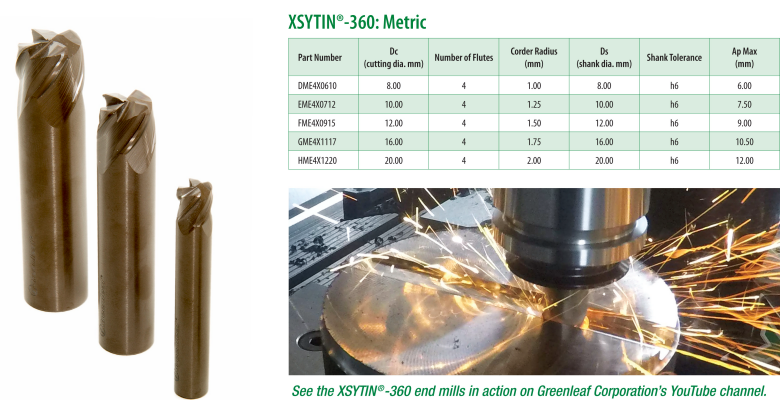
Среди производителей инструмента из керамики и PCBN (фрезы, пластины) хотелось бы отметить ряд брендов.
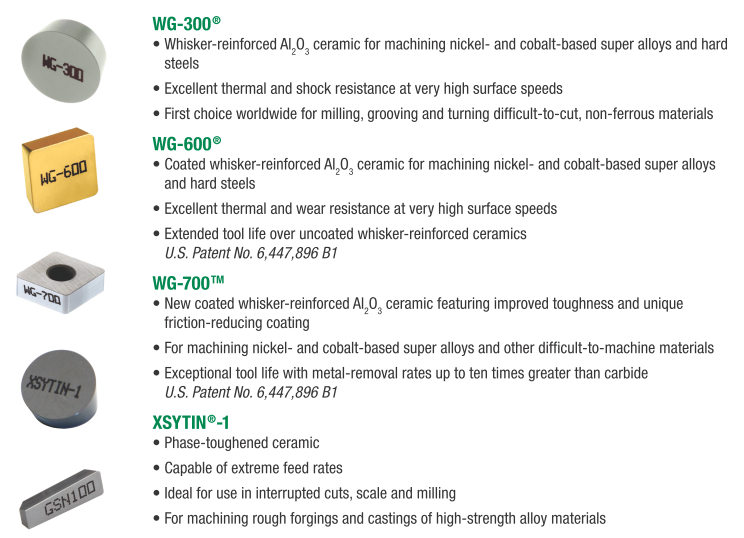
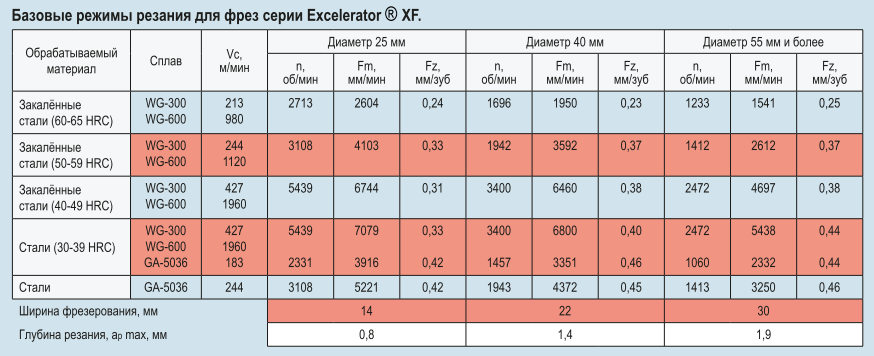
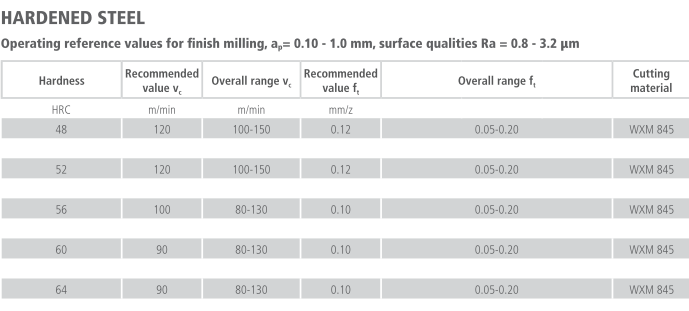
Ssangyong (Union Materials) http://www.ssym.com/eng/html/main.html Южно Корейский производитель керамического инструмента и CBN
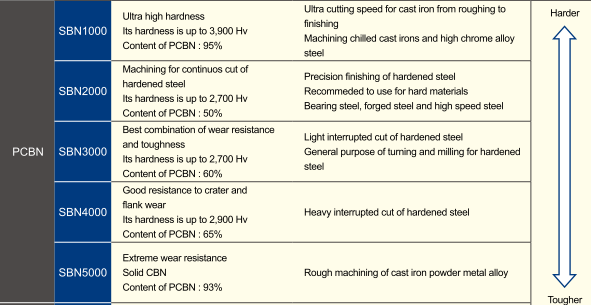

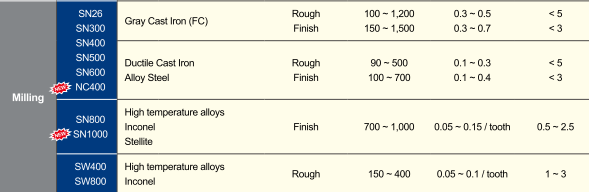
Производителей инструментов из CBN очень много, отдельно на них останавливаться не будем, при желании можно ознакомиться с ними по ссылкам в данной статье https://carbidetool.ru/superhard_material_tools
Основное применение малоразмерных фрез из CBN твердое фрезерование миниатюрных полостей пресс-форм.
PCBN минимум в два раза тверже любого керамического или карбидного материала. Компромисс - прочность: чем тверже резак, тем он менее прочен. Это ограничивает применение PCBN, особенно при прерывистом резании.
PCBN может стоить в 10 раз дороже, чем сопоставимые керамика и карбиды. Однако, срок службы инструмента из PCBN в 3-5 раз выше. Т.е на первый взгляд это не выгодно.
PCBN позволяет выдерживать очень жесткие допуски с минимальным износом.
Это означает, что, например, на больших пресс-формах можно обработать всю полость с помощью одного инструмента PCBN и избежать необходимости совмещения в середине реза после смены инструмента.
Как и у керамики, режущие кромки инструментов из PCBN расположены под отрицательным углом к заготовке. Подготовка кромок имеет первостепенное значение при использовании PCBN, инструмент шлифуется (образуется требуемая фаска или скругление), в зависимости от операции. К сожалению, инструменты из PCBN также страдают от тех же отказов, что и керамика. Они лучше всего работают в жестких, предсказуемых условиях резания и обладают меньшей прочностью по сравнению с твердосплавными сплавами. По этой причине они обычно используются только для чистовой обработки и зарезервированы для самых требовательных операций, таких как чрезвычайно тяжелая обработка, требования жестких допусков и длительные производственные циклы.
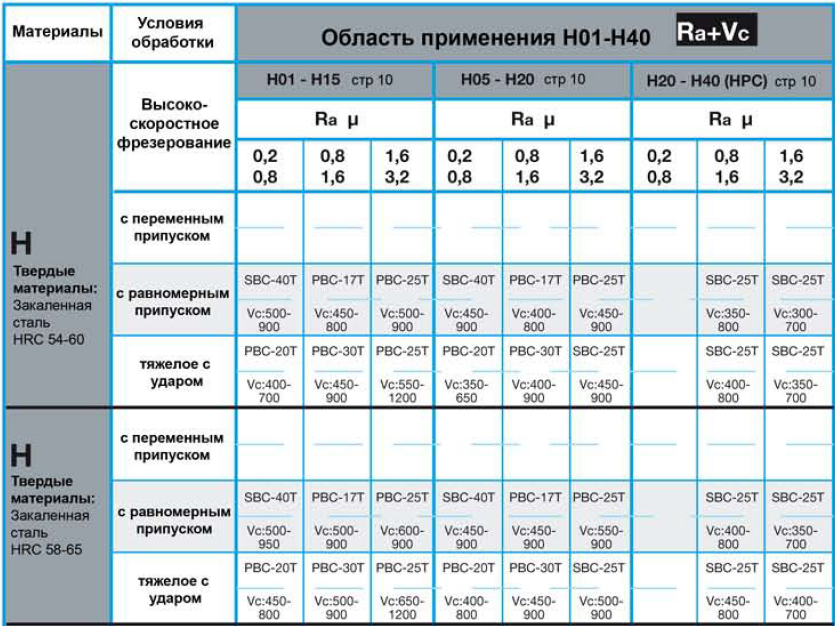
Использование материалов сайта возможно только с письменного разрешения администрации сайта и активной гиперссылкой на источник.
Свяжитесь с нами
Оставьте свое сообщение и мы свяжемся с вами, чтобы предложить лучшие условия сотрудничества!
Звоните: (812) 407-37-03
Пишите: order@carbidetool.ru
ООО «ТУЛЭКС» ИНН 7838092179, г. Санкт-Петербург, улица Аэродромная, д. 8, литер А, офис 418